Plasma Vapor Deposition (PVD) is a sophisticated thin-film coating technique widely used in various industries, including electronics, optics, and automotive. It involves the use of plasma to deposit thin layers of material onto a substrate. The process begins by creating a plasma environment, typically through the ionization of a gas, which then interacts with a target material, causing it to vaporize. The vaporized material is then transported and deposited onto the substrate, forming a thin, uniform layer. This method is highly valued for its ability to produce coatings with excellent adhesion, durability, and precise control over thickness and composition. PVD is particularly advantageous for applications requiring high-performance coatings, such as wear resistance, corrosion protection, and enhanced optical properties.
Key Points Explained:
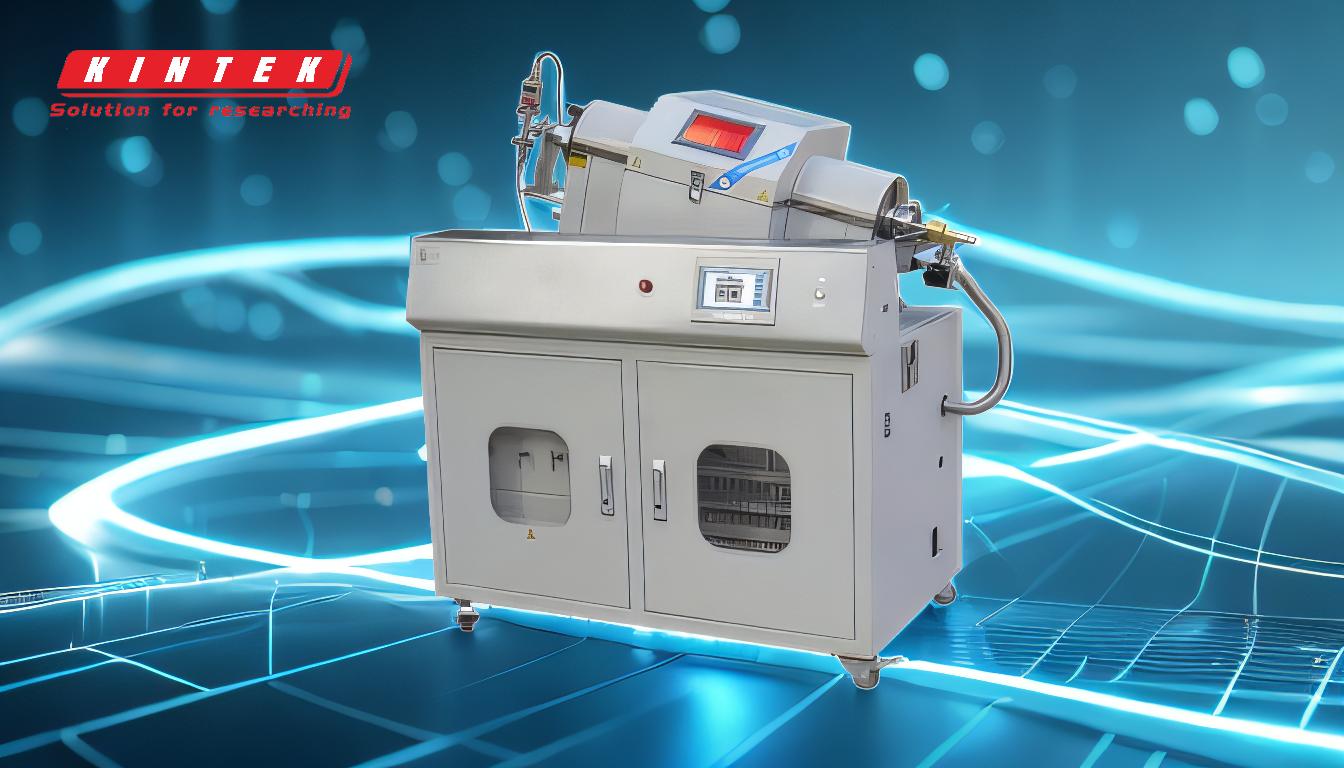
-
Creation of Plasma Environment:
- The first step in PVD is the creation of a plasma environment. This is typically achieved by introducing a gas, such as argon, into a vacuum chamber and then ionizing it using an electric field or high-energy sources like lasers or electron beams. The ionization process strips electrons from the gas atoms, creating a plasma composed of ions and free electrons. This plasma is essential for the subsequent steps in the PVD process.
-
Target Material Vaporization:
- Once the plasma is established, the target material, which is the substance to be deposited, is introduced into the chamber. The high-energy ions in the plasma collide with the target material, causing it to vaporize. This vaporization can occur through several mechanisms, including sputtering, where ions physically knock atoms off the target, or evaporation, where the target is heated to the point of vaporization. The choice of mechanism depends on the specific PVD technique being used, such as sputter deposition or arc vapor deposition.
-
Transport of Vaporized Material:
- The vaporized material is then transported through the plasma environment to the substrate. This transport is facilitated by the kinetic energy of the vaporized atoms and the electric fields present in the plasma. The atoms or molecules of the vaporized material move in a directed manner towards the substrate, ensuring a controlled and uniform deposition process.
-
Deposition on Substrate:
- Upon reaching the substrate, the vaporized material condenses and forms a thin film. The deposition process is influenced by several factors, including the energy of the vaporized atoms, the temperature of the substrate, and the presence of any reactive gases in the chamber. These factors can be adjusted to control the properties of the deposited film, such as its thickness, composition, and microstructure. The result is a high-quality coating with excellent adhesion and uniformity.
-
Advantages of PVD:
- PVD offers several advantages over other coating techniques. It allows for the deposition of a wide range of materials, including metals, ceramics, and composites, with precise control over the film's properties. The coatings produced by PVD are highly durable, with excellent wear and corrosion resistance, making them ideal for demanding applications. Additionally, PVD is an environmentally friendly process, as it typically does not involve hazardous chemicals and produces minimal waste.
-
Applications of PVD:
- PVD is used in a variety of industries for different applications. In the electronics industry, it is used to deposit thin films for semiconductor devices, solar cells, and displays. In the optics industry, PVD is employed to create anti-reflective coatings, mirrors, and filters. The automotive industry uses PVD for decorative and functional coatings on components such as engine parts, wheels, and trim. Other applications include medical devices, cutting tools, and aerospace components, where the high-performance coatings provided by PVD are essential for durability and functionality.
In summary, Plasma Vapor Deposition is a versatile and precise method for applying thin-film coatings with superior properties. Its ability to produce high-quality, durable coatings makes it a preferred choice in many high-tech industries.
Summary Table:
Step | Description |
---|---|
1. Plasma Creation | Ionization of gas (e.g., argon) in a vacuum chamber using electric fields or lasers. |
2. Target Vaporization | High-energy ions collide with the target material, causing it to vaporize. |
3. Material Transport | Vaporized material is transported through plasma to the substrate. |
4. Deposition | Vapor condenses on the substrate, forming a thin, uniform film. |
5. Advantages | Precise control, durability, wear resistance, and eco-friendly process. |
6. Applications | Electronics, optics, automotive, medical devices, aerospace, and more. |
Discover how PVD can enhance your products—contact our experts today for tailored solutions!