Pyrolysis is a thermochemical process that begins with the heating of organic materials, such as biomass or plastic waste, in the absence of oxygen. This process breaks down long-chain molecules into smaller molecules due to thermal vibration at high temperatures, typically ranging from 300°C to 900°C. The absence of oxygen prevents combustion, allowing the material to decompose into gases, liquids, and solids, which can be further refined into valuable products like fuel oil, syngas, and biochar. The process starts with the preparation of the feedstock, including pre-treatment to remove impurities and grinding to the required size. The material is then loaded into a pyrolysis chamber, heated, and decomposed into its constituent components, which are subsequently separated and processed.
Key Points Explained:
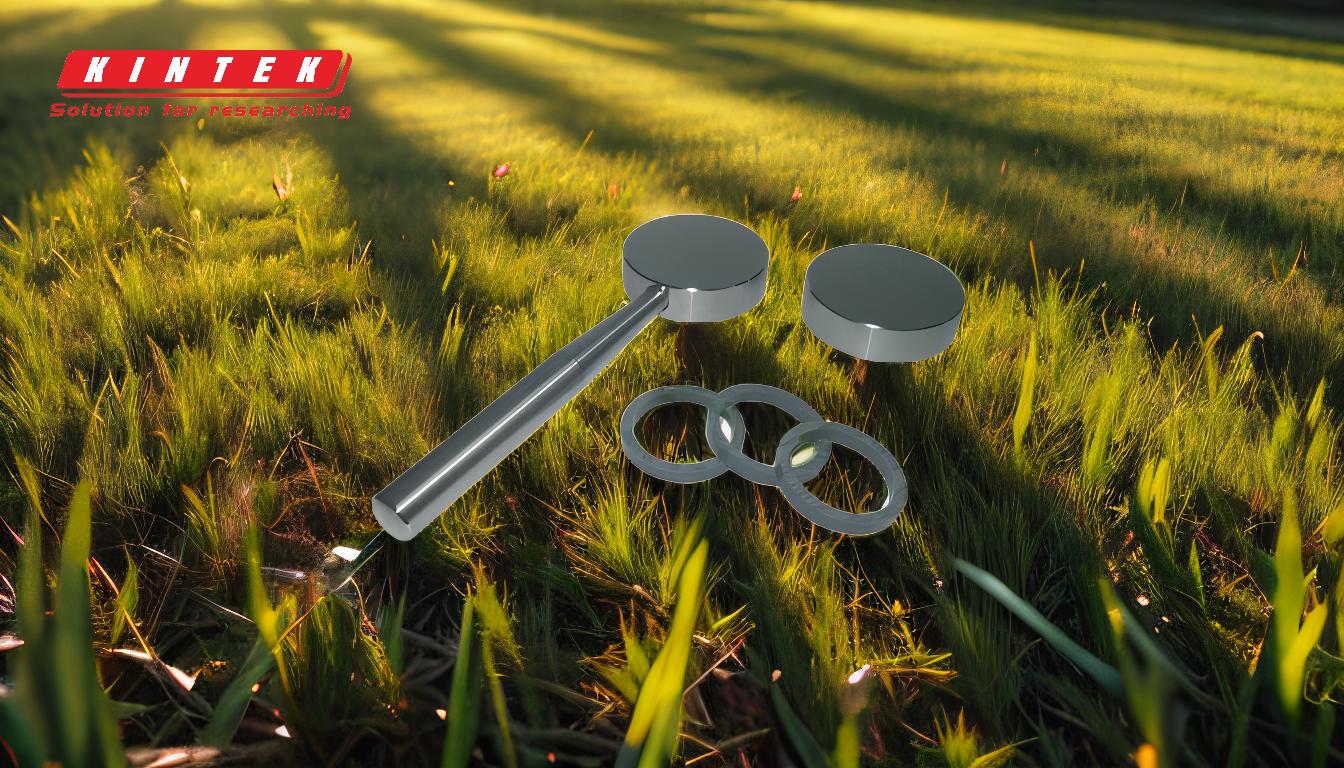
-
Definition and Mechanism of Pyrolysis:
- Pyrolysis is the thermal decomposition of materials at elevated temperatures in an inert (oxygen-free) atmosphere.
- The process breaks down long-chain molecules into smaller molecules due to excessive thermal vibration.
- The term "pyrolysis" comes from the Greek words "pyro" (fire/heat) and "lysis" (separation), indicating the separation of materials through heat.
-
Temperature Range:
- Pyrolysis typically occurs at temperatures between 300°C and 900°C.
- The specific temperature depends on the material being processed and the desired end products.
- Higher temperatures generally lead to more complete decomposition and the production of gases, while lower temperatures may favor the formation of liquids and solids.
-
Absence of Oxygen:
- A critical aspect of pyrolysis is the absence of oxygen, which prevents combustion.
- Without oxygen, the material decomposes rather than burns, allowing for the production of useful byproducts like bio-oil, syngas, and biochar.
-
Feedstock Preparation:
- The pyrolysis process begins with the preparation of the feedstock.
- For biomass or plastic waste, this involves pre-treatment to remove impurities (e.g., metals, dirt) and grinding the material to a uniform size.
- Proper preparation ensures efficient decomposition and optimal product yield.
-
Loading into the Pyrolysis Chamber:
- The prepared feedstock is loaded into a pyrolysis reactor or chamber.
- The chamber is designed to maintain an inert atmosphere and withstand high temperatures.
- In some cases, a catalyst may be added to enhance the decomposition process.
-
Heating and Decomposition:
- The material is heated to the required temperature, causing it to melt and vaporize.
- The thermal energy breaks the chemical bonds in the material, leading to the formation of smaller molecules.
- The decomposition products include gases (syngas), liquids (bio-oil), and solids (biochar).
-
Separation of Products:
- After decomposition, the products are separated based on their physical state.
- Gases and vapors are condensed into liquid form (bio-oil), while non-condensable gases (syngas) are collected.
- Solid residues (biochar) settle at the bottom of the reactor and are removed for further processing or use.
-
Applications of Pyrolysis Products:
- Bio-oil: Can be refined and used as fuel or as a feedstock for chemical production.
- Syngas: Can be used as a fuel or converted into other chemicals.
- Biochar: Used as a soil amendment, carbon sequestration agent, or in filtration systems.
-
Energy Requirements and Challenges:
- Pyrolysis is an energy-intensive process, requiring significant heat input.
- The process must be carefully controlled to optimize product yields and minimize energy consumption.
- Challenges include managing heat distribution, ensuring consistent feedstock quality, and handling byproducts safely.
-
Industrial Implementation:
- In industrial settings, pyrolysis reactors are designed to handle large volumes of feedstock.
- Systems often include a combustion chamber for heat supply, a cyclotron for product separation, and recycling mechanisms for non-condensable gases.
- The process is scalable and can be adapted for various materials, including biomass, plastics, and tires.
By understanding these key points, one can appreciate the complexity and potential of pyrolysis as a method for converting waste materials into valuable resources. The process begins with careful preparation and heating of the feedstock, followed by the controlled decomposition and separation of products, all while maintaining an oxygen-free environment to prevent combustion.
Summary Table:
Key Aspect | Details |
---|---|
Definition | Thermal decomposition in an oxygen-free atmosphere. |
Temperature Range | 300°C to 900°C, depending on feedstock and desired products. |
Key Products | Bio-oil, syngas, and biochar. |
Feedstock Preparation | Pre-treatment to remove impurities and grinding to uniform size. |
Process Steps | Heating, decomposition, and separation of gases, liquids, and solids. |
Applications | Fuel production, chemical feedstock, soil amendment, and carbon capture. |
Challenges | Energy-intensive, heat distribution, feedstock consistency, and byproduct handling. |
Ready to explore how pyrolysis can turn waste into valuable resources? Contact us today to learn more!