Calcination is a thermal treatment process used to induce chemical or physical changes in materials by heating them to high temperatures, typically below their melting points, in the absence or limited supply of air or oxygen. This process is widely employed in industries such as metallurgy, ceramics, and chemical manufacturing to achieve objectives like thermal decomposition, removal of volatile substances, or phase transitions. For example, it is used to extract metals from ores, decompose calcium carbonate into calcium oxide and carbon dioxide, or remove bound moisture from materials like borax. The calcination process is critical for producing inorganic materials and purifying substances by eliminating impurities.
Key Points Explained:
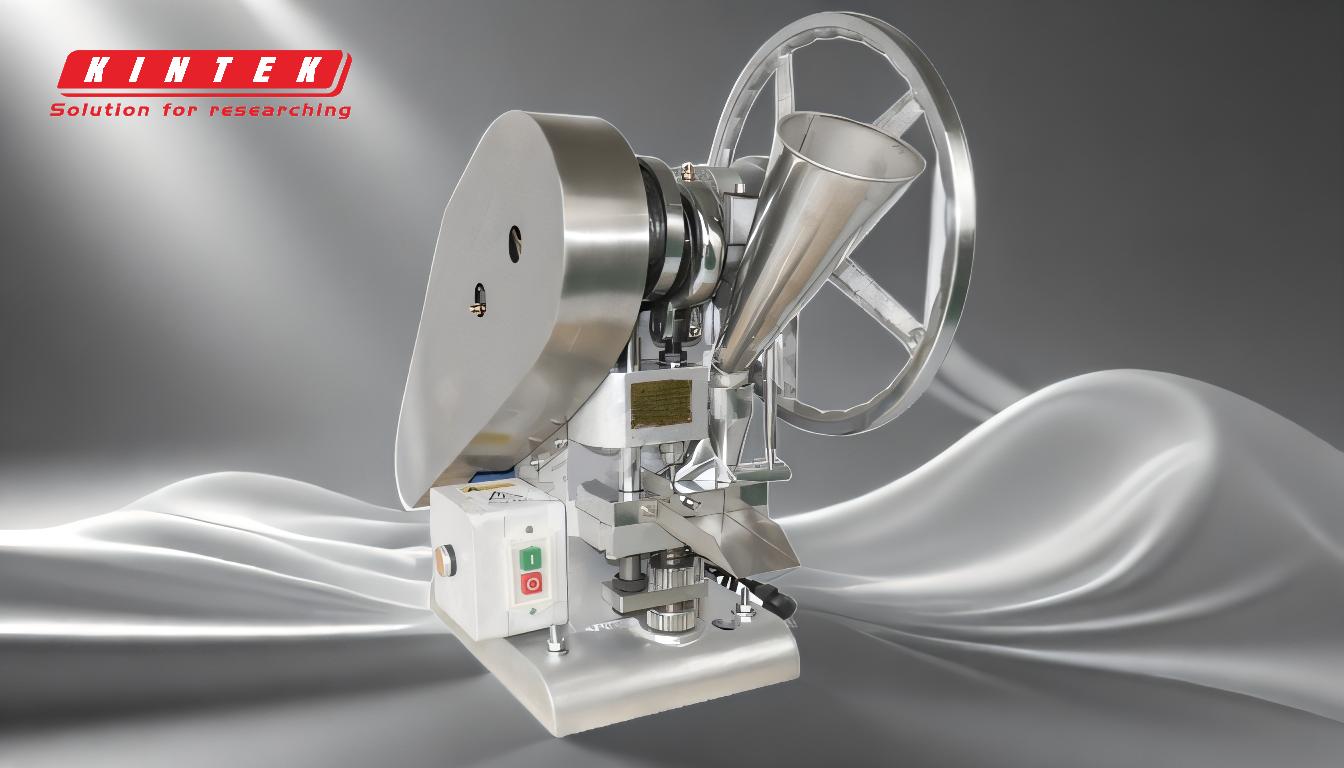
-
Definition and Purpose of Calcination:
- Calcination is a heat treatment process where materials are heated to high temperatures, just below their melting points, to induce thermal decomposition or remove volatile components.
- The primary purposes of calcination include:
- Thermal decomposition of compounds (e.g., calcium carbonate into calcium oxide and carbon dioxide).
- Removal of volatile substances (e.g., water, carbon dioxide, or sulfur dioxide).
- Phase transitions or oxidation of materials.
- Extraction of metals from ores by eliminating impurities.
-
Key Conditions for Calcination:
- Temperature: The material is heated to a temperature below its melting point to avoid liquefaction while achieving the desired chemical or physical changes.
- Atmosphere: Calcination is typically carried out in the absence of air or with a limited supply of oxygen to prevent unwanted oxidation or combustion.
- Duration: The heating duration depends on the material and the specific objectives of the process.
-
Mechanisms of Calcination:
- Thermal Decomposition: Many compounds decompose into simpler substances when heated. For example, calcium carbonate (CaCO₃) decomposes into calcium oxide (CaO) and carbon dioxide (CO₂) at high temperatures.
- Removal of Volatile Components: Calcination can remove bound moisture, carbon dioxide, or other volatile impurities from materials. For instance, borax loses its water of crystallization during calcination.
- Oxidation or Reduction: In some cases, calcination can involve partial or complete oxidation of a substance, depending on the availability of oxygen.
-
Applications of Calcination:
- Metallurgy: Calcination is used to extract metals from ores by removing volatile impurities. For example, metal oxides are often produced from carbonate or hydroxide ores through calcination.
- Ceramics and Inorganic Materials: Calcination is essential for producing materials like cement, lime, and ceramics. It helps in transforming raw materials into usable forms by removing moisture and decomposing carbonates.
- Chemical Manufacturing: Calcination is used to produce inorganic chemicals, such as calcium oxide from limestone or magnesium oxide from magnesium carbonate.
- Purification: The process is employed to purify materials by eliminating unwanted volatile components or impurities.
-
Examples of Calcination Reactions:
- Decomposition of Calcium Carbonate: [ \text{CaCO}_3 \xrightarrow{\text{Heat}} \text{CaO} + \text{CO}_2 ] This reaction is fundamental in the production of lime for construction and industrial applications.
- Dehydration of Borax: [ \text{Na}_2\text{B}_4\text{O}_7 \cdot 10\text{H}_2\text{O} \xrightarrow{\text{Heat}} \text{Na}_2\text{B}_4\text{O}_7 + 10\text{H}_2\text{O} ] Calcination removes the water of crystallization from borax, making it anhydrous.
- Oxidation of Metal Sulfides: [ 2\text{ZnS} + 3\text{O}_2 \xrightarrow{\text{Heat}} 2\text{ZnO} + 2\text{SO}_2 ] This reaction is used in the extraction of zinc from its sulfide ores.
-
Equipment Used in Calcination:
- Calcination Furnaces: These are specialized furnaces designed to heat materials to the required temperatures in controlled atmospheres. They can be rotary kilns, muffle furnaces, or fluidized bed reactors, depending on the application.
- Rotary Kilns: Commonly used for large-scale calcination processes, such as in cement production or metal extraction.
- Muffle Furnaces: Used for smaller-scale or laboratory calcination, where precise temperature control is required.
-
Advantages of Calcination:
- Efficient removal of volatile impurities and moisture.
- Production of high-purity materials.
- Enables the transformation of raw materials into useful industrial products.
- Facilitates the extraction of metals from ores.
-
Challenges and Considerations:
- Energy-intensive process due to high temperatures required.
- Proper control of temperature and atmosphere is critical to avoid unwanted reactions or material degradation.
- Environmental concerns, such as the release of carbon dioxide or sulfur dioxide, must be managed.
By understanding the principles, mechanisms, and applications of calcination, industries can optimize this process for material purification, decomposition, and transformation, ensuring high-quality outputs for various applications.
Summary Table:
Aspect | Details |
---|---|
Definition | Heat treatment process below melting point to induce chemical/physical changes. |
Purpose | Thermal decomposition, removal of volatiles, phase transitions, metal extraction. |
Key Conditions | Temperature below melting point, limited oxygen, controlled duration. |
Mechanisms | Thermal decomposition, removal of volatiles, oxidation/reduction. |
Applications | Metallurgy, ceramics, chemical manufacturing, purification. |
Equipment | Calcination furnaces, rotary kilns, muffle furnaces. |
Advantages | High-purity materials, efficient impurity removal, metal extraction. |
Challenges | Energy-intensive, requires precise temperature/atmosphere control. |
Optimize your calcination process with expert guidance—contact us today!