DLC (Diamond-Like Carbon) coatings are highly durable due to their unique combination of properties, including high hardness (1500–3000 HV), low coefficient of friction, and resistance to wear, corrosion, and chemicals. These coatings are widely used in demanding applications such as automotive components, machinery, medical implants, and optical devices. Their durability is further enhanced by their ability to maintain performance under extreme conditions, such as high temperatures and corrosive environments. The deposition methods, such as PECVD and PACVD, ensure strong adhesion and uniform coating, making DLC a reliable choice for long-lasting protection and performance enhancement in various industries.
Key Points Explained:
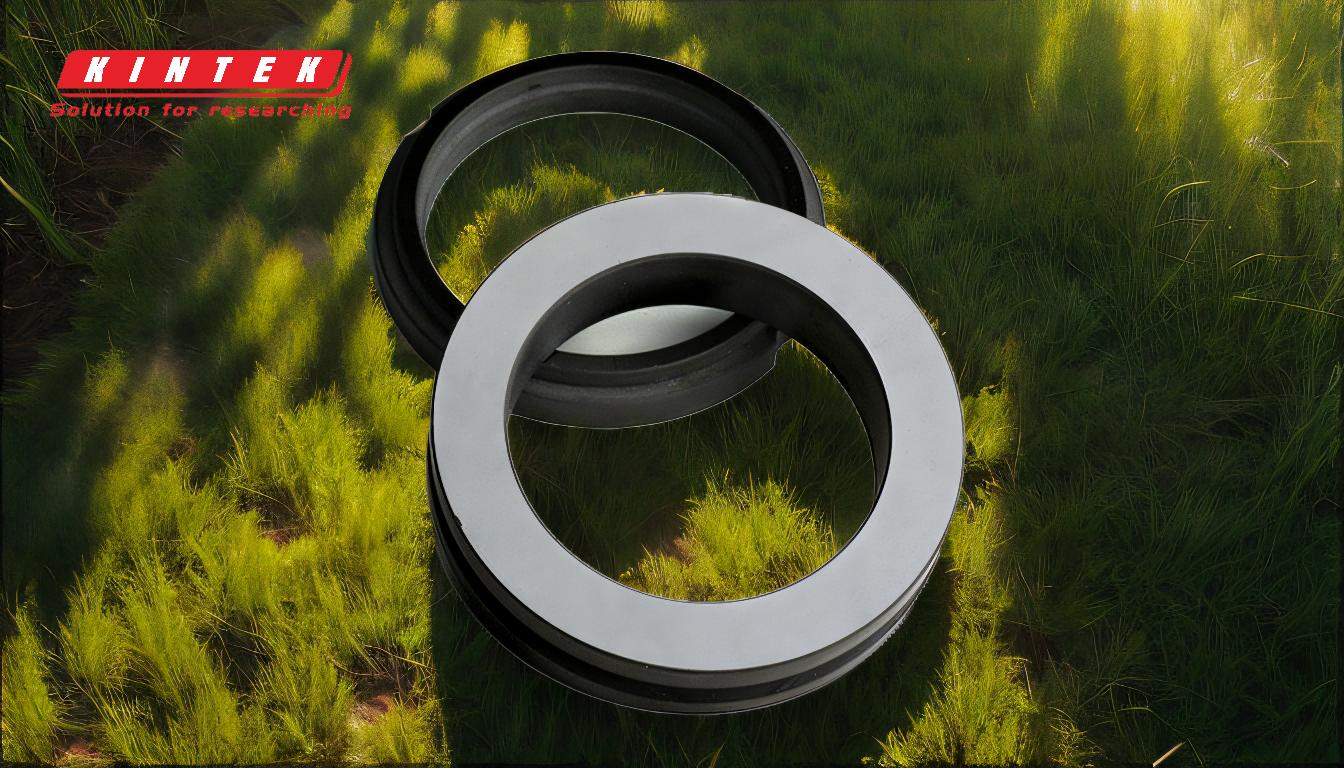
-
High Hardness and Wear Resistance:
- DLC coatings exhibit a hardness range of 1500–3000 HV, making them comparable to diamond in terms of durability.
- This high hardness translates to excellent wear resistance, which is critical for applications like automotive components (e.g., camshafts, bearings) and industrial tools.
- The wear resistance ensures that the coating maintains its integrity even under high-stress conditions, reducing the need for frequent replacements.
-
Low Coefficient of Friction:
- DLC coatings have a low coefficient of friction, which minimizes wear and tear during sliding or rolling movements.
- This property is particularly beneficial in tribological systems, such as engines and machinery, where reducing friction leads to energy savings and longer component lifespans.
-
Chemical and Corrosion Resistance:
- DLC coatings are chemically inert, making them resistant to corrosion and degradation in harsh environments.
- This property is essential for applications in medical implants, where biocompatibility and resistance to bodily fluids are crucial, as well as in industrial settings exposed to corrosive substances.
-
Adhesion and Uniformity:
- Deposition methods like PECVD (Plasma-Enhanced Chemical Vapor Deposition) and PACVD (Plasma-Assisted Chemical Vapor Deposition) ensure strong adhesion of DLC coatings to substrates.
- These methods also allow for uniform coating thickness, which is vital for maintaining consistent performance across the entire surface.
-
Versatility in Applications:
- DLC coatings are used in a wide range of industries, including automotive, medical, optical, and decorative applications.
- Their durability makes them suitable for high-precision tools, optical components, and even luxury items like watches, where both functionality and aesthetics are important.
-
Thermal Stability:
- DLC coatings maintain their properties at high temperatures, which is essential for applications like engine components that operate under extreme heat.
- This thermal stability ensures that the coating does not degrade or lose its protective qualities over time.
-
Biocompatibility:
- In medical applications, DLC coatings are biocompatible, meaning they do not react adversely with human tissues or bodily fluids.
- This makes them ideal for use in implants and prostheses, where long-term durability and safety are paramount.
-
Deposition Techniques:
- PECVD and PACVD are commonly used to produce DLC coatings, offering advantages such as lower deposition temperatures and high deposition rates.
- These techniques allow for the coating of sensitive substrates, such as polymers, without causing distortion or damage.
-
Barrier Properties:
- DLC coatings provide excellent barrier properties, protecting substrates from environmental factors like moisture and gases.
- This is particularly useful in packaging films and optical sensing applications, where precise control over thickness and refractive index is required.
-
Challenges and Limitations:
- While DLC coatings are highly durable, challenges remain in scaling up production for certain applications, such as barrier packaging films.
- Ongoing research and development are focused on overcoming these challenges to further enhance the durability and applicability of DLC coatings.
In summary, DLC coatings are exceptionally durable due to their high hardness, low friction, chemical resistance, and strong adhesion. These properties make them suitable for a wide range of demanding applications, ensuring long-lasting performance and protection. The choice of deposition method further enhances their durability, making DLC coatings a reliable solution for industries requiring high-performance materials.
Summary Table:
Property | Description |
---|---|
High Hardness | 1500–3000 HV, comparable to diamond, ensuring excellent wear resistance. |
Low Friction | Minimizes wear and tear, ideal for engines and machinery. |
Chemical Resistance | Resistant to corrosion and degradation in harsh environments. |
Adhesion & Uniformity | PECVD and PACVD methods ensure strong adhesion and uniform coating thickness. |
Thermal Stability | Maintains properties at high temperatures, suitable for extreme conditions. |
Biocompatibility | Safe for medical implants, resistant to bodily fluids. |
Barrier Properties | Protects against moisture and gases, ideal for packaging and optical applications. |
Enhance your applications with durable DLC coatings—contact our experts today!