PVD (Physical Vapor Deposition) coatings are renowned for their exceptional durability, making them one of the most robust finishes available today. These coatings are significantly harder than traditional finishes like chrome, offering superior resistance to scratches, corrosion, and wear. The lifespan of a PVD coating can range from 10 years to hundreds of years, depending on factors such as the substrate material, coating thickness, bond strength, and environmental conditions. PVD coatings are widely used in industries like jewelry, automotive, and aerospace due to their ability to maintain vibrant colors and resist fading over time. Proper application and maintenance further enhance their longevity, making them a reliable choice for high-durability applications.
Key Points Explained:
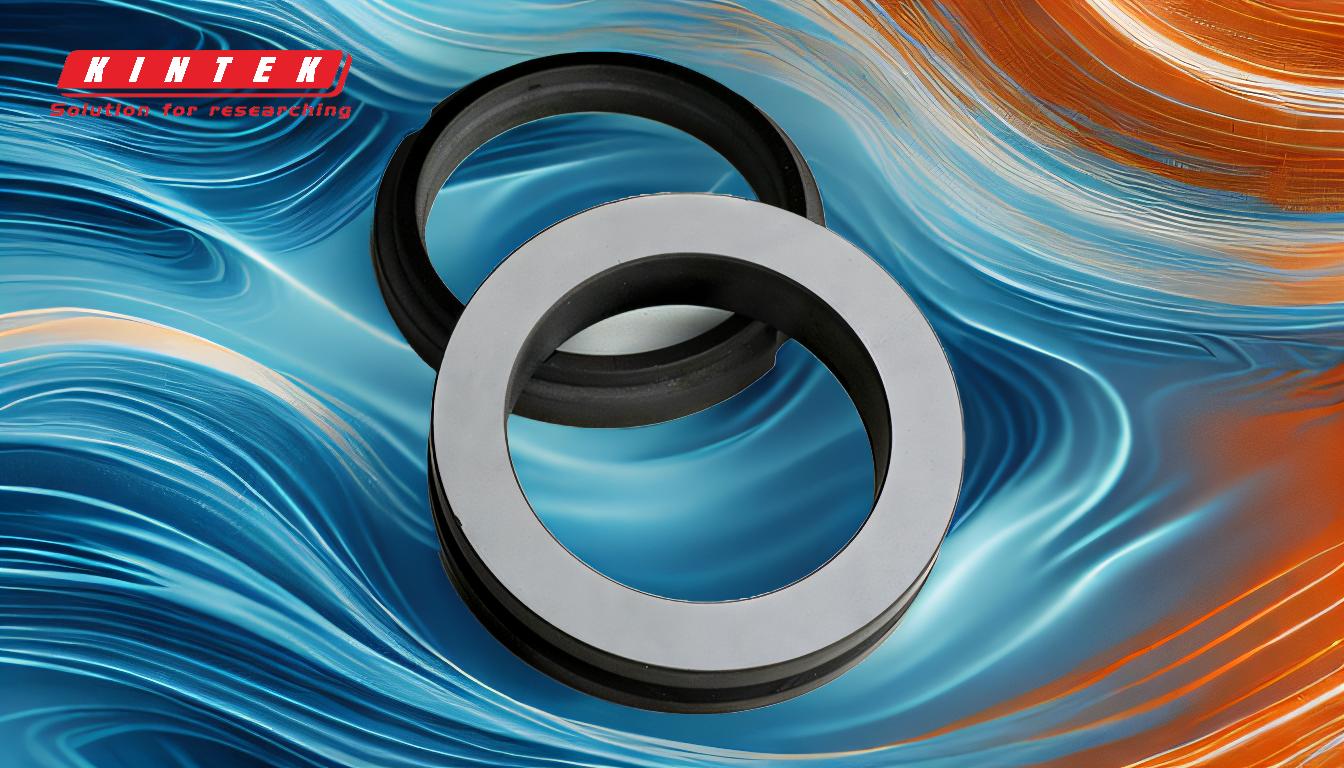
-
Superior Hardness and Scratch Resistance:
- PVD coatings are four times harder than chrome, making them extremely resistant to scratches and wear.
- This hardness ensures that the finish remains intact even under harsh conditions, such as frequent use or exposure to abrasive materials.
-
Resistance to Fading and Discoloration:
- PVD coatings are highly resistant to fading, ensuring that the finish retains its bright and vibrant appearance for years.
- This makes PVD coatings ideal for applications where aesthetics are important, such as in jewelry or decorative hardware.
-
Longevity and Durability:
- The lifespan of PVD coatings can range from 10 years to hundreds of years, depending on various factors.
- Key factors influencing durability include the type of substrate, coating thickness, bond strength, and exposure to environmental conditions like high temperatures or corrosive substances.
-
Application-Specific Durability:
- In the jewelry industry, PVD coatings can last up to 10 years with proper application and maintenance.
- In more demanding applications, such as automotive or aerospace, PVD coatings can last significantly longer due to their robust properties.
-
Environmental and Wear Resistance:
- PVD coatings exhibit excellent resistance to corrosion, abrasion, and impact, making them suitable for use in harsh environments.
- These properties ensure that the coating remains effective even under extreme conditions, such as exposure to chemicals or high mechanical stress.
-
Comparison to Traditional Finishes:
- PVD coatings are far more durable than traditional finishes like chrome or electroplating.
- They offer superior quality and longevity, ensuring that they outlast other types of coatings in terms of both performance and appearance.
-
Factors Affecting Coating Lifespan:
- Substrate Material: The type of material being coated can influence how well the PVD coating adheres and performs over time.
- Coating Thickness: Thicker coatings generally offer better durability and protection.
- Bond Strength: A strong bond between the coating and the substrate is crucial for long-term durability.
- Environmental Conditions: Exposure to high temperatures, corrosive substances, or mechanical wear can affect the coating's lifespan.
-
Maintenance and Proper Application:
- Proper application techniques and regular maintenance can significantly extend the lifespan of PVD coatings.
- Ensuring that the coating is applied uniformly and that the substrate is properly prepared can enhance the coating's durability.
In summary, PVD coatings are among the most durable finishes available, offering superior hardness, resistance to wear and corrosion, and long-lasting vibrancy. Their durability makes them suitable for a wide range of applications, from jewelry to industrial uses, and their lifespan can be maximized through proper application and maintenance.
Summary Table:
Key Feature | Description |
---|---|
Superior Hardness | 4x harder than chrome, offering exceptional scratch and wear resistance. |
Fade Resistance | Retains vibrant colors and resists discoloration for years. |
Lifespan | Ranges from 10 years to hundreds of years, depending on application and care. |
Environmental Resistance | Resists corrosion, abrasion, and impact, even in harsh conditions. |
Applications | Widely used in jewelry, automotive, and aerospace industries. |
Factors Affecting Durability | Substrate material, coating thickness, bond strength, and environmental exposure. |
Maximize the durability of your products with PVD coatings—contact us today to learn more!