Biochar is produced through a process called pyrolysis, which involves heating biomass in the absence of oxygen to thermally decompose it into biochar, bio-oil, and combustible gases. The process is particularly effective for slow pyrolysis, where lower temperatures (around 400°C) and longer residence times are used. The biomass is first prepared by drying and grinding, then heated in a pyrolysis reactor. The resulting biochar settles at the bottom of the reactor, while gases and liquids are condensed into bio-oil. The energy required for the process can be partially covered by the combustion of the gaseous byproducts. This method is widely used for converting organic waste into valuable biochar, which has applications in agriculture, carbon sequestration, and energy production.
Key Points Explained:
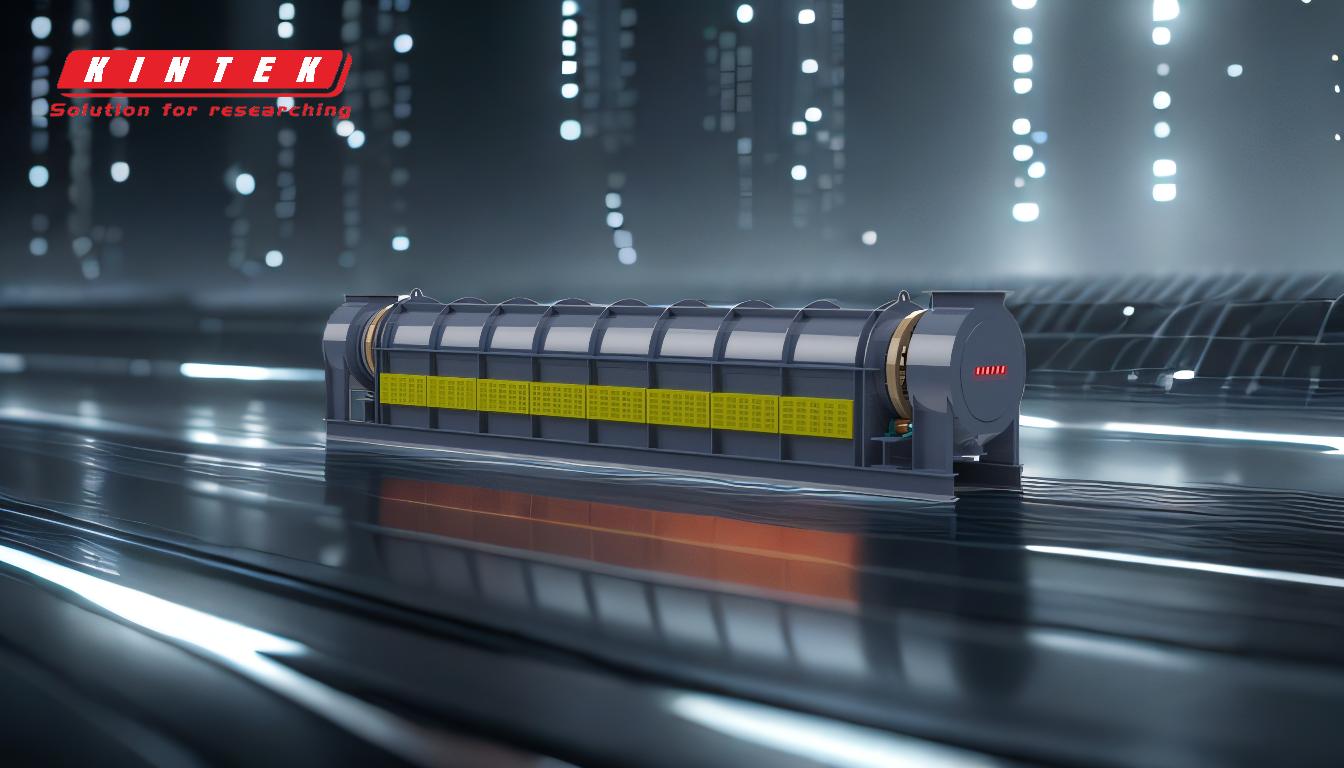
-
What is Pyrolysis?
- Pyrolysis is a thermochemical process that decomposes organic materials, such as biomass, in the absence of oxygen. This process occurs at high temperatures (typically between 200-900°C) and produces three main products: biochar, bio-oil, and combustible gases.
- The absence of oxygen prevents combustion, ensuring that the biomass is thermally decomposed rather than burned.
-
Types of Pyrolysis for Biochar Production
- Slow Pyrolysis: This is the most common method for biochar production. It involves lower temperatures (around 400°C) and longer residence times (several hours). The slow heating rate maximizes biochar yield while producing bio-oil and gases as byproducts.
- Fast Pyrolysis: This method uses higher temperatures and shorter residence times, favoring the production of bio-oil over biochar.
- Gasification: While not strictly pyrolysis, gasification also produces biochar but at higher temperatures and with a focus on generating syngas.
-
Steps in the Pyrolysis Process
- Pre-Treatment: Biomass is dried to reduce moisture content and mechanically comminuted (crushed or ground) to ensure uniform heating.
- Pyrolysis Reaction: The dried and ground biomass is loaded into a pyrolysis reactor. The reactor is heated to the desired temperature (around 400°C for slow pyrolysis) in the absence of oxygen. The biomass undergoes thermal decomposition, producing biochar, bio-oil, and gases.
- Separation: After pyrolysis, the biochar settles at the bottom of the reactor. The gases and liquids are condensed into bio-oil, while non-condensable gases (syngas) are often recycled to provide energy for the process.
- Cooling and Cleaning: The biochar is cooled and discharged, while exhaust gases are de-dusted to reduce harmful substances.
-
Energy Balance and Sustainability
- The energy required for pyrolysis can be partially or fully covered by the combustion of the gaseous byproducts (syngas). This makes the process energy-efficient and sustainable.
- The use of renewable biomass as feedstock further enhances the environmental benefits of biochar production.
-
Applications of Biochar
- Agriculture: Biochar improves soil fertility, water retention, and nutrient availability. It also enhances microbial activity in the soil.
- Carbon Sequestration: Biochar is stable and can store carbon for hundreds to thousands of years, making it a valuable tool for mitigating climate change.
- Energy Production: The bio-oil and syngas produced during pyrolysis can be used as fuels or further refined for industrial applications.
-
Industrial Pyrolysis Process
- In industrial settings, the pyrolysis process is optimized for efficiency and scalability. Dry biomass is fed into a pyrolysis reactor with controlled oxygen levels. Heat is supplied via a combustion chamber, and the decomposed materials are separated using cyclones or other separation technologies. Biochar is collected at the bottom, while gases and liquids are quenched to form bio-oil.
By understanding these key points, a purchaser of equipment or consumables for biochar production can make informed decisions about the type of pyrolysis system to invest in, the feedstock to use, and the potential applications of the biochar produced.
Summary Table:
Key Aspect | Details |
---|---|
Process | Pyrolysis: Heating biomass in the absence of oxygen. |
Types of Pyrolysis | Slow Pyrolysis (400°C, longer times), Fast Pyrolysis, Gasification. |
Steps | Pre-treatment, Pyrolysis Reaction, Separation, Cooling & Cleaning. |
Energy Efficiency | Gaseous byproducts (syngas) provide energy for the process. |
Applications | Agriculture, Carbon Sequestration, Energy Production. |
Ready to explore biochar production solutions? Contact us today to get started!