Diamond coating is a specialized process that involves depositing a thin layer of diamond onto a substrate to enhance its properties, such as hardness, wear resistance, and thermal conductivity. The most common method for applying diamond coatings is through chemical vapor deposition (CVD), which includes techniques like microwave plasma CVD (MPCVD), DC arc plasma spray CVD (DAPCVD), and hot wire CVD (HFCVD). These methods involve creating a plasma environment where carbon-containing gases decompose, allowing diamond to form on the substrate. Pretreatment of the substrate is crucial, especially for complex shapes, as it ensures proper adhesion of the diamond coating. However, current pretreatment technologies are more effective for simpler shapes, leaving room for improvement in handling intricate geometries like tools and molds.
Key Points Explained:
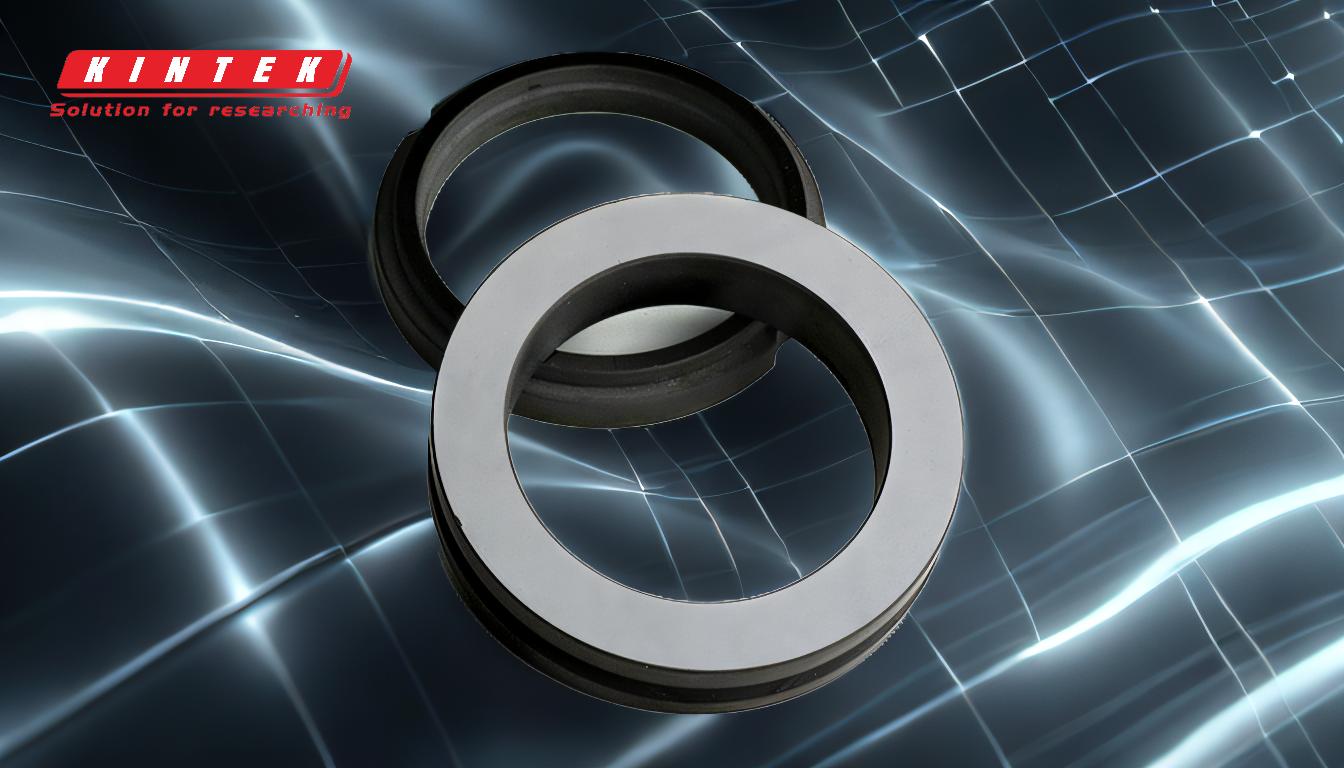
-
Chemical Vapor Deposition (CVD) as the Primary Method:
- Diamond coatings are predominantly applied using CVD techniques. This process involves introducing a carbon-containing gas (e.g., methane) into a vacuum chamber, where it is ionized into plasma. The plasma breaks down the gas, releasing carbon atoms that form diamond crystals on the substrate.
- CVD is favored for its ability to produce high-quality, uniform diamond coatings with excellent adhesion and purity.
-
Types of CVD Methods:
- Microwave Plasma CVD (MPCVD): This method uses microwave energy to generate plasma, which dissociates the carbon-containing gas. MPCVD is known for its ability to produce high-purity diamond coatings and is widely used in industrial applications.
- DC Arc Plasma Spray CVD (DAPCVD): In this method, a high-energy DC arc creates plasma, which is then sprayed onto the substrate. DAPCVD is suitable for large-scale applications and can coat complex geometries.
- Hot Wire CVD (HFCVD): This technique uses a heated filament to decompose the gas, forming diamond on the substrate. HFCVD is cost-effective and can be used for coating a variety of materials.
-
Importance of Substrate Pretreatment:
- Pretreatment is a critical step in diamond coating to ensure strong adhesion between the diamond layer and the substrate. Common pretreatment methods include surface cleaning, roughening, and seeding with diamond particles.
- For substrates with simple shapes, pretreatment is relatively straightforward. However, for tools and molds with complex geometries, achieving uniform pretreatment is challenging, which can affect the quality and durability of the coating.
-
Challenges in Coating Complex Shapes:
- Current pretreatment technologies are optimized for substrates with general shapes, such as flat surfaces or simple curves. When it comes to intricate geometries, like those found in cutting tools or molds, the pretreatment process often falls short.
- Uneven pretreatment can lead to poor adhesion, delamination, or inconsistent coating thickness, limiting the effectiveness of the diamond coating.
-
Future Directions for Improvement:
- Research is ongoing to develop advanced pretreatment techniques tailored for complex shapes. These include precision surface modification, advanced seeding methods, and innovative plasma treatments.
- Improving pretreatment for complex geometries will expand the applications of diamond coatings, particularly in industries like aerospace, automotive, and manufacturing, where precision tools and molds are essential.
By understanding the CVD process and the challenges associated with substrate pretreatment, manufacturers can better optimize diamond coating techniques for a wide range of applications, including those requiring complex geometries.
Summary Table:
Aspect | Details |
---|---|
Primary Method | Chemical Vapor Deposition (CVD) |
CVD Techniques | MPCVD, DAPCVD, HFCVD |
Key Benefits | Enhanced hardness, wear resistance, thermal conductivity |
Pretreatment Importance | Ensures strong adhesion; critical for complex geometries |
Challenges | Uneven pretreatment for intricate shapes, leading to adhesion issues |
Future Improvements | Advanced pretreatment for complex geometries, expanding industrial applications |
Interested in optimizing diamond coating for your applications? Contact our experts today to learn more!