The production of iron in an induction furnace involves using electromagnetic induction to melt metallic charges, such as scrap iron or pig iron, into a liquid state. The process begins with charging the furnace with raw materials, followed by heating them to high temperatures (around 1650°C) using an induction coil powered by electricity. Once the metal is molten, it is tapped into a ladle for further refining or casting. This method is efficient, energy-saving, and environmentally friendly compared to traditional blast furnaces. Below, the process is broken down into key steps and explained in detail.
Key Points Explained:
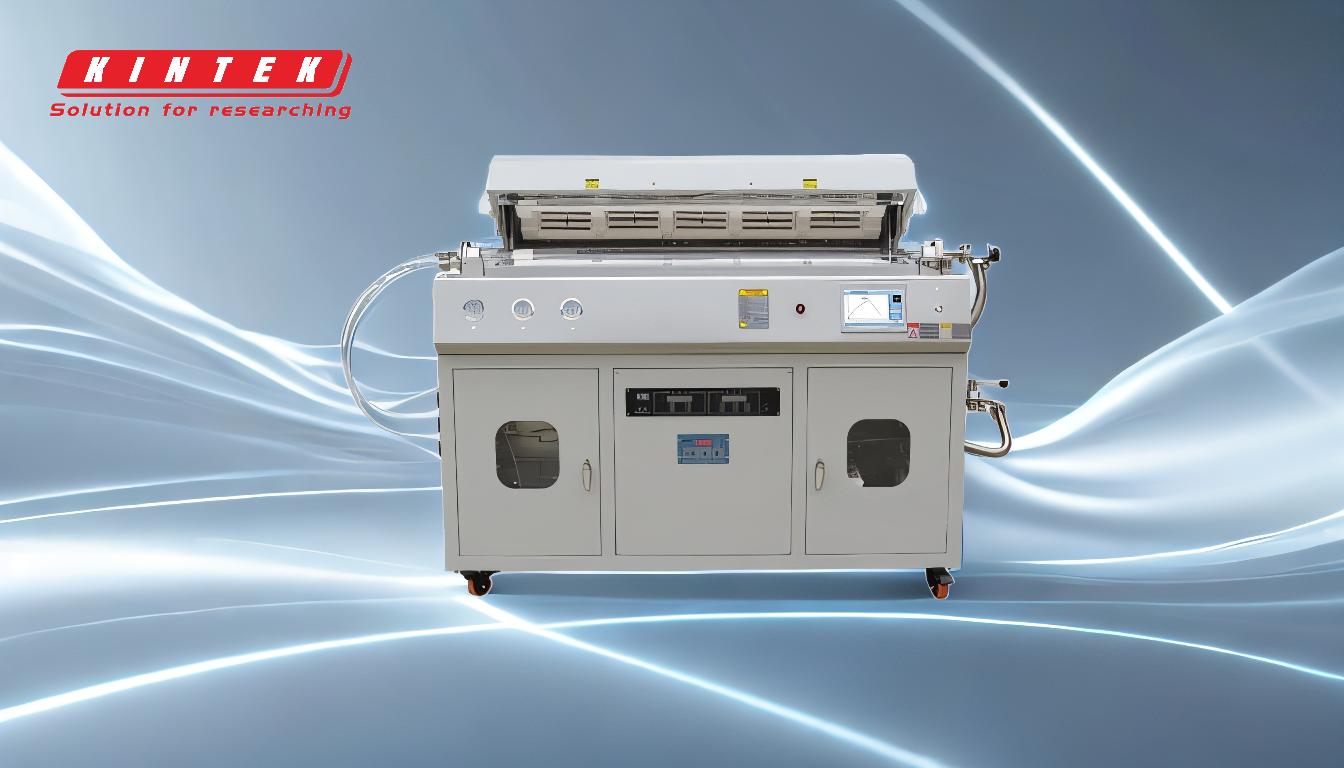
-
Introduction to Induction Furnaces:
- Induction furnaces are widely used in steel and iron production due to their efficiency and precision. They rely on electromagnetic induction to generate heat within the metallic charge, making them suitable for melting and refining iron and steel.
- The furnace typically consists of a crucible surrounded by an induction coil, which is powered by an IGBT induction furnace. IGBT (Insulated Gate Bipolar Transistor) technology ensures precise control over the heating process, making it ideal for modern steel manufacturing.
-
Charging the Furnace:
- The process begins with charging the furnace with raw materials, which can include scrap iron, pig iron, or other iron-containing materials. These materials are carefully selected based on the desired composition of the final product.
- The charge is loaded into the crucible, which is designed to withstand high temperatures and chemical reactions during the melting process.
-
Melting Process:
- Once the furnace is charged, the induction coil is activated, generating a high-frequency alternating magnetic field. This field induces eddy currents within the metallic charge, causing it to heat up and eventually melt.
- The temperature inside the furnace can reach up to 1650°C, which is sufficient to melt iron and other alloying elements. The use of an IGBT induction furnace ensures efficient energy transfer and precise temperature control.
-
Refining and Alloying:
- During the melting process, impurities such as sulfur and phosphorus are removed through chemical reactions. Fluxes like limestone or dolomite may be added to facilitate slag formation, which captures impurities and floats to the surface.
- Alloying elements, such as carbon, manganese, or chromium, can be added to achieve the desired steel or iron composition. The induction furnace allows for precise control over the alloying process, ensuring consistent quality.
-
Tapping and Casting:
- Once the molten iron reaches the desired temperature and composition, it is tapped from the furnace into a steel ladle. The tapping process involves tilting the furnace or opening a tap hole to pour the molten metal.
- The ladle is then transported to the next stage of production, which may include continuous casting, ingot casting, or further refining in secondary metallurgy processes.
-
Advantages of Induction Furnaces:
- Induction furnaces offer several advantages over traditional blast furnaces, including:
- Energy Efficiency: The direct heating of the charge reduces energy losses.
- Precision: The use of IGBT induction furnace technology allows for precise control over temperature and composition.
- Environmental Benefits: Induction furnaces produce fewer emissions compared to blast furnaces, making them more environmentally friendly.
- Flexibility: They can handle a wide range of raw materials and produce various grades of steel and iron.
- Induction furnaces offer several advantages over traditional blast furnaces, including:
-
Applications in Modern Steel Manufacturing:
- Induction furnaces are commonly used in small to medium-scale steel production, as well as in foundries for casting iron and steel components. Their ability to produce high-quality metal with minimal environmental impact makes them a preferred choice in modern manufacturing.
By following these steps, iron is efficiently produced in an induction furnace, leveraging advanced technologies like IGBT induction furnace to ensure high-quality output. This method is not only cost-effective but also aligns with sustainable manufacturing practices.
Summary Table:
Step | Description |
---|---|
1. Charging | Raw materials (scrap iron, pig iron) are loaded into the crucible. |
2. Melting | Induction coil generates heat, melting the charge at up to 1650°C. |
3. Refining | Impurities are removed, and alloying elements are added for desired composition. |
4. Tapping & Casting | Molten iron is tapped into a ladle for further refining or casting. |
5. Advantages | Energy-efficient, precise, eco-friendly, and flexible for various applications. |
Discover how induction furnaces can revolutionize your metal production—contact us today for expert guidance!