Diamond coating is a specialized process used to apply a thin layer of diamond or diamond-like carbon (DLC) onto surfaces, typically for enhancing hardness, wear resistance, or thermal conductivity. The most common methods involve Chemical Vapor Deposition (CVD) and Physical Vapor Deposition (PVD). CVD techniques, such as hot-filament, microwave plasma, and arcjet-torch methods, use hydrogen and methane gases in a high-temperature chamber to deposit a pure diamond film. PVD, on the other hand, involves evaporating a source material to form a DLC coating. These processes are widely used for coating carbide tools and other industrial applications.
Key Points Explained:
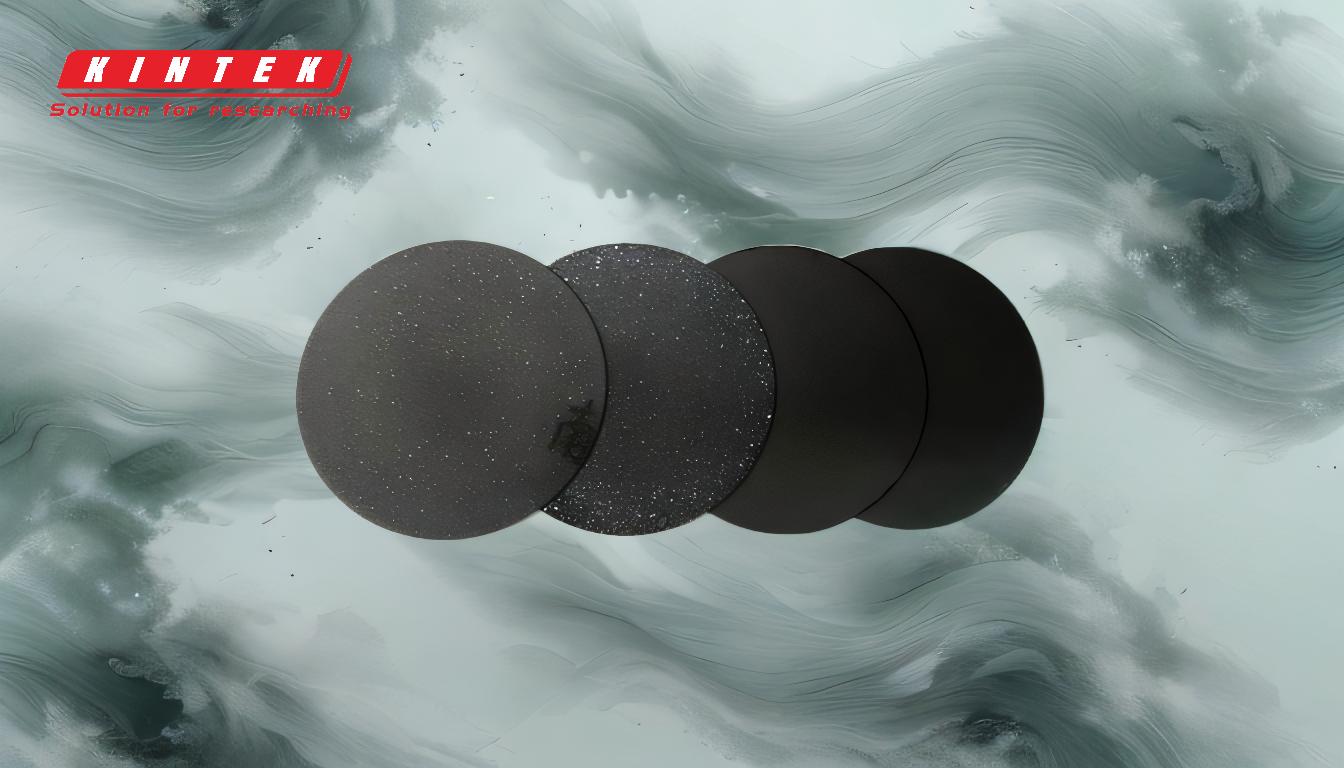
-
Overview of Diamond Coating Methods:
- Diamond coatings are applied using two primary methods: Chemical Vapor Deposition (CVD) and Physical Vapor Deposition (PVD).
- CVD is the most common method for creating pure diamond films, while PVD is used for Diamond-Like Carbon (DLC) coatings.
-
Chemical Vapor Deposition (CVD) Process:
- Setup: The process begins by loading the tools or substrates into a chamber filled with hydrogen and methane gases.
- Energy Source: Tungsten wires heated to over 2,300°C (4,172°F) provide the energy required to break down the gas molecules.
- Reaction: The high temperature activates carbon atoms from the methane, which then recombine to form a pure diamond film on the tool surface.
- Temperature: The tools are heated to over 750°C (1,382°F) to facilitate the deposition process.
- Applications: CVD is commonly used for coating tungsten carbide (WC-Co) tools, as it provides a durable and wear-resistant diamond layer.
-
Types of CVD Techniques:
- Hot-Filament CVD (HFCVD): Uses heated tungsten filaments to activate the gas mixture.
- Microwave Plasma CVD (MPCVD): Utilizes microwave energy to create a plasma for diamond deposition.
- DC Arc Plasma Spray CVD (DAPCVD): Employs an electric arc to generate plasma for coating.
- Arcjet-Torch CVD: Uses a high-velocity plasma jet for deposition.
-
Physical Vapor Deposition (PVD) Process:
- Setup: PVD involves placing the tool in a vacuum chamber with a source material.
- Evaporation: The source material is evaporated using high-energy methods such as sputtering or laser ablation.
- Condensation: The vaporized material condenses onto the tool surface, forming a thin DLC coating.
- Thickness: The resulting DLC layer is typically 0.5 to 2.5 microns thick.
- Applications: PVD is often used for coating carbide tools with amorphous diamond-like carbon, which provides a balance of hardness and low friction.
-
Historical Context and Development:
- Early methods for diamond coating, such as those developed by Matsumoto et al. in 1982, combined hydrogen presence with CVD techniques in custom-built chambers.
- These advancements laid the groundwork for modern CVD and PVD methods, enabling the widespread use of diamond coatings in industrial applications.
-
Key Considerations for Equipment and Consumable Purchasers:
- Method Selection: Choose between CVD and PVD based on the desired coating properties (e.g., pure diamond vs. DLC) and application requirements.
- Tool Compatibility: Ensure the substrate material (e.g., tungsten carbide) is suitable for the chosen coating method.
- Temperature Tolerance: Verify that the tools can withstand the high temperatures required for CVD processes.
- Coating Thickness: Consider the optimal thickness for the application, as thicker coatings may offer greater durability but could affect tool dimensions.
- Cost and Efficiency: Evaluate the cost-effectiveness of the coating method, including equipment, consumables, and processing time.
By understanding these key points, purchasers and users of diamond-coated tools can make informed decisions about the most suitable coating methods and processes for their specific needs.
Summary Table:
Aspect | Details |
---|---|
Primary Methods | Chemical Vapor Deposition (CVD), Physical Vapor Deposition (PVD) |
CVD Process | Uses hydrogen and methane gases, high temperatures (750°C+), tungsten wires |
PVD Process | Evaporates source material in a vacuum, forms DLC coatings (0.5-2.5 microns) |
Applications | Coating carbide tools for durability, wear resistance, and low friction |
Key Considerations | Method selection, tool compatibility, temperature tolerance, cost analysis |
Ready to enhance your tools with diamond coatings? Contact our experts today for tailored solutions!