Thin film thickness during evaporation is measured using a variety of techniques, each with its own advantages and limitations. Real-time monitoring methods like quartz crystal microbalance (QCM) and optical interference are commonly used to track film growth during deposition. Post-deposition, techniques such as ellipsometry, profilometry, interferometry, X-ray reflectivity (XRR), and cross-sectional electron microscopy (SEM/TEM) are employed for precise measurements. These methods rely on principles like interference, refractive index analysis, and mechanical profiling to determine thickness. The choice of technique depends on factors like material properties, required accuracy, and whether the measurement is in situ or post-deposition.
Key Points Explained:
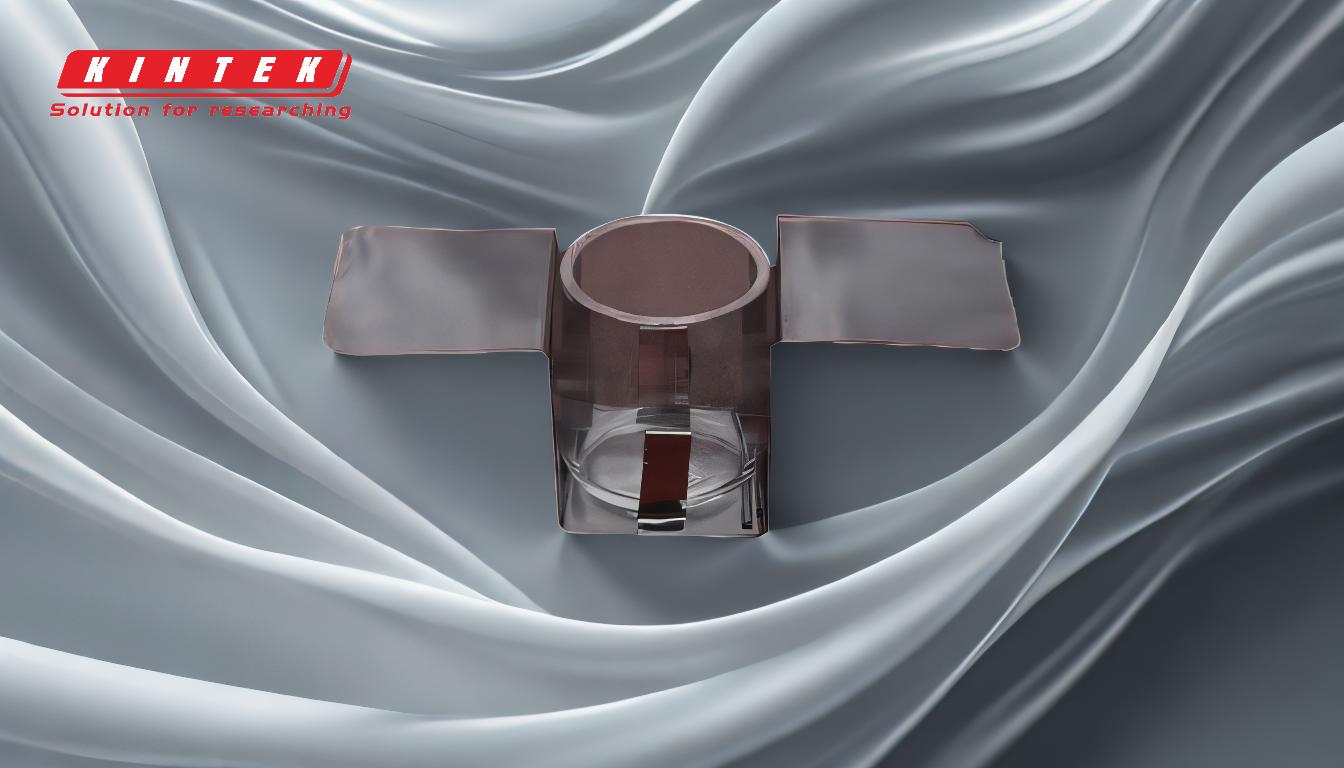
-
Quartz Crystal Microbalance (QCM)
- Principle: QCM sensors measure mass changes on a quartz crystal resonator during deposition. As the film grows, the mass increases, causing a shift in the crystal's resonant frequency.
- Advantages: Real-time monitoring, high sensitivity, and suitability for in situ measurements.
- Limitations: Requires calibration and is sensitive to environmental factors like temperature and pressure.
-
Optical Interference
- Principle: This method analyzes the interference pattern created by light reflecting off the top and bottom interfaces of the film. The number of interference peaks and valleys is used to calculate thickness.
- Advantages: Non-contact, real-time monitoring, and high accuracy for transparent or semi-transparent films.
- Limitations: Requires knowledge of the material's refractive index and may not work well for very thin or highly absorbing films.
-
Ellipsometry
- Principle: Measures changes in the polarization state of light reflected from the film surface. The thickness is derived from the phase shift and amplitude change of the reflected light.
- Advantages: High precision, non-destructive, and suitable for very thin films (nanometer range).
- Limitations: Requires a model for data interpretation and is sensitive to surface roughness.
-
Profilometry
- Principle: A mechanical stylus or optical probe scans the film surface to measure height differences between the film and substrate.
- Advantages: Direct measurement, suitable for a wide range of thicknesses (0.3 to 60 µm).
- Limitations: Requires a step or groove between the film and substrate, and may damage delicate films.
-
Interferometry
- Principle: Uses interference fringes created by a highly reflective surface to measure thickness. The spacing of the fringes corresponds to the film thickness.
- Advantages: High resolution and non-contact measurement.
- Limitations: Requires a reflective surface and may be affected by film uniformity.
-
X-ray Reflectivity (XRR)
- Principle: Measures the intensity of X-rays reflected from the film at various angles. The thickness is determined from the interference pattern in the reflected X-rays.
- Advantages: High accuracy for ultra-thin films (nanometer range) and multi-layer structures.
- Limitations: Requires specialized equipment and is sensitive to surface roughness and density variations.
-
Cross-sectional SEM/TEM
- Principle: Uses electron microscopy to image a cross-section of the film. The thickness is measured directly from the image.
- Advantages: Provides detailed structural information and high resolution.
- Limitations: Destructive, requires sample preparation, and is time-consuming.
-
Spectrophotometry
- Principle: Measures the intensity of light transmitted through or reflected from the film. The thickness is calculated based on the interference pattern and material properties.
- Advantages: Non-contact, suitable for microscopic sampling areas, and works for a wide range of thicknesses.
- Limitations: Requires knowledge of the material's optical properties and may not work well for very thin or highly absorbing films.
-
Stylus Profilometry
- Principle: A mechanical stylus moves across the film surface to measure the height difference between the film and substrate.
- Advantages: Simple and direct measurement.
- Limitations: Requires a step or groove and may damage the film.
-
Non-contact Optical Techniques
- Principle: Uses optical methods like interferometry or spectrophotometry to measure thickness without physical contact.
- Advantages: Non-destructive, high accuracy, and suitable for delicate films.
- Limitations: Requires a reflective or transparent surface and may be affected by film uniformity.
In summary, the choice of technique depends on the specific requirements of the deposition process, such as the need for real-time monitoring, the material properties of the film, and the desired accuracy. Combining multiple methods can provide a more comprehensive understanding of film thickness and uniformity.
Summary Table:
Technique | Principle | Advantages | Limitations |
---|---|---|---|
Quartz Crystal Microbalance | Measures mass changes on a quartz crystal resonator | Real-time monitoring, high sensitivity | Requires calibration, sensitive to environmental factors |
Optical Interference | Analyzes interference patterns from light reflections | Non-contact, real-time monitoring, high accuracy | Requires refractive index knowledge, less effective for thin/absorbing films |
Ellipsometry | Measures polarization changes in reflected light | High precision, non-destructive, suitable for nanometer-range films | Requires data interpretation model, sensitive to surface roughness |
Profilometry | Scans film surface with a mechanical stylus or optical probe | Direct measurement, suitable for 0.3 to 60 µm films | Requires a step or groove, may damage delicate films |
Interferometry | Uses interference fringes from a reflective surface | High resolution, non-contact | Requires reflective surface, affected by film uniformity |
X-ray Reflectivity (XRR) | Measures reflected X-ray intensity at various angles | High accuracy for ultra-thin films and multi-layer structures | Requires specialized equipment, sensitive to surface roughness and density |
Cross-sectional SEM/TEM | Images film cross-section using electron microscopy | Detailed structural information, high resolution | Destructive, requires sample preparation, time-consuming |
Spectrophotometry | Measures light intensity transmitted or reflected through the film | Non-contact, suitable for microscopic areas, wide thickness range | Requires optical properties knowledge, less effective for thin/absorbing films |
Stylus Profilometry | Measures height differences with a mechanical stylus | Simple and direct measurement | Requires a step or groove, may damage the film |
Non-contact Optical | Uses optical methods like interferometry or spectrophotometry | Non-destructive, high accuracy, suitable for delicate films | Requires reflective/transparent surface, affected by film uniformity |
Need help selecting the right thin film thickness measurement technique? Contact our experts today for tailored advice!