The lifespan of ceramic materials, particularly ceramic coatings, depends on the quality of the ceramic, the application environment, and maintenance practices. High-quality ceramic coatings can last between 2 to 5 years with proper care, and in some cases, up to 10 years or more. Ceramics are inherently durable due to their chemical composition and bonding, which provide high temperature resistance, corrosion resistance, abrasion resistance, and insulation properties. Advanced ceramics, with their ionic or covalent bonds, further enhance these properties, making them suitable for demanding applications. Understanding these factors helps in selecting the right ceramic material for specific needs.
Key Points Explained:
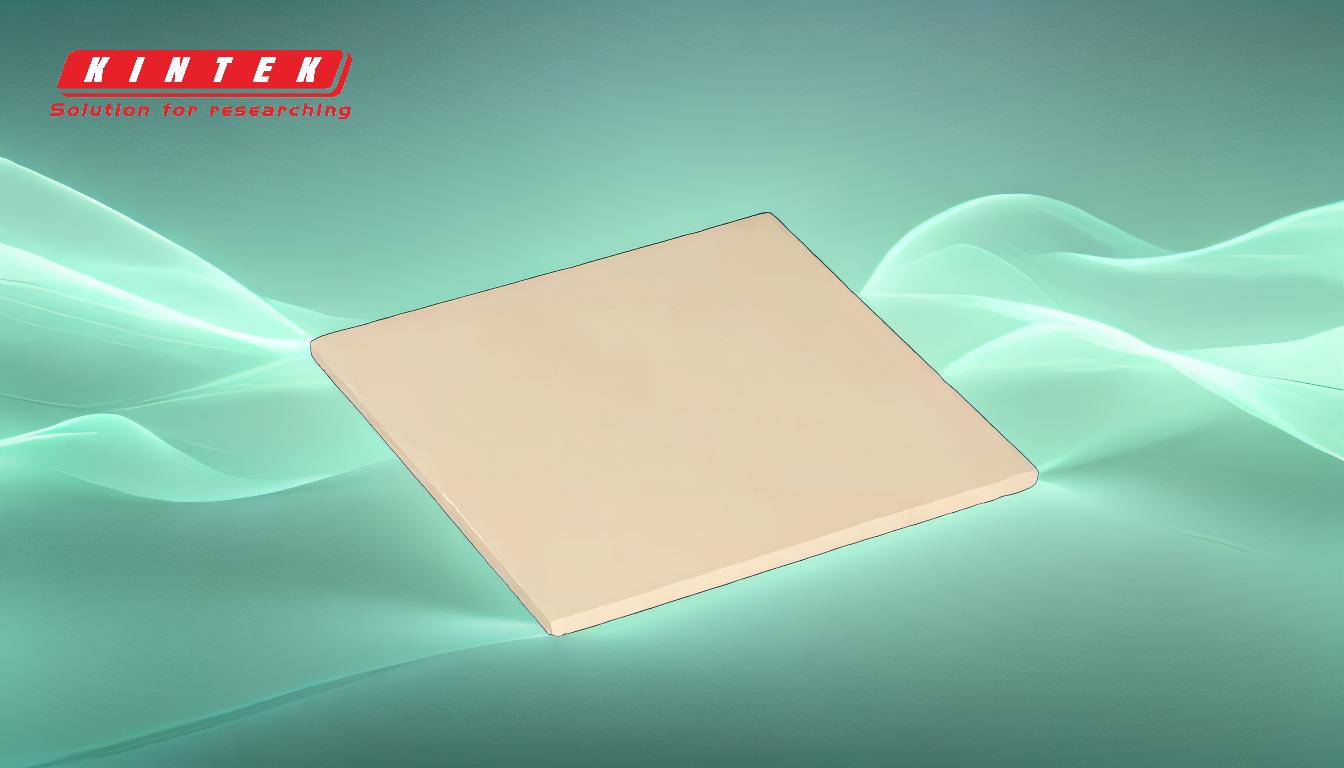
-
Lifespan of Ceramic Coatings:
- High-quality ceramic coatings typically last between 2 to 5 years with proper care.
- Some premium coatings can extend their lifespan to 10 years or more, depending on the quality and maintenance.
-
Factors Influencing Ceramic Longevity:
- Quality of the Ceramic: Higher-quality ceramics with advanced formulations tend to last longer.
- Application Environment: Exposure to harsh conditions (e.g., extreme temperatures, chemicals, or abrasion) can reduce lifespan.
- Maintenance Practices: Regular cleaning and proper care can significantly extend the life of ceramic coatings.
-
Inherent Properties of Ceramics:
- High Temperature Resistance: Ceramics can withstand extreme heat, making them ideal for high-temperature applications.
- Corrosion Resistance: They are resistant to chemical corrosion, which enhances their durability in corrosive environments.
- Abrasion Resistance: Ceramics are highly resistant to wear and tear, making them suitable for high-friction applications.
- Insulation Properties: Their excellent electrical insulation makes them valuable in electronic and electrical applications.
-
Advanced Ceramics:
- Advanced ceramics are composed of ionic or covalent bonds, which provide superior strength, hardness, and durability.
- These materials are used in demanding applications such as aerospace, medical implants, and industrial machinery due to their high strength, wear resistance, and biocompatibility.
-
Applications and Durability:
- Automotive: Ceramic coatings are used for car paint protection, offering long-lasting shine and protection against environmental damage.
- Industrial: Ceramics are used in machinery components, cutting tools, and wear-resistant parts due to their durability.
- Medical: Advanced ceramics are used in implants and prosthetics because of their biocompatibility and resistance to bodily fluids.
-
Maintenance Tips for Extending Ceramic Lifespan:
- Regular Cleaning: Use gentle, non-abrasive cleaners to avoid damaging the ceramic surface.
- Avoid Harsh Chemicals: Strong acids or alkalis can degrade the ceramic coating over time.
- Inspect for Damage: Regularly check for chips or cracks and address them promptly to prevent further deterioration.
By understanding these key points, purchasers and users can make informed decisions about selecting and maintaining ceramic materials to maximize their lifespan and performance.
Summary Table:
Aspect | Details |
---|---|
Lifespan | 2-5 years (up to 10+ years with premium coatings and proper care). |
Key Influencing Factors | Quality, application environment, and maintenance practices. |
Inherent Properties | High temperature, corrosion, abrasion resistance, and insulation. |
Advanced Ceramics | Ionic/covalent bonds for superior strength, hardness, and biocompatibility. |
Applications | Automotive, industrial machinery, medical implants, and more. |
Maintenance Tips | Regular cleaning, avoiding harsh chemicals, and inspecting for damage. |
Want to learn more about maximizing the lifespan of ceramic coatings? Contact our experts today for tailored advice!