The length of a cement rotary kiln can vary significantly depending on its design, application, and production capacity. Cement rotary kilns are typically long, horizontal steel cylinders lined with refractory materials, and they are designed to facilitate the chemical reactions required for cement production. The length of these kilns can range from around 50 meters to as much as 230 meters, with the upper limit being constrained by structural considerations such as the shell's ability to withstand deformation under its own weight. The length-to-diameter (L/D) ratio is a critical design parameter, influencing the kiln's efficiency, heat distribution, and residence time of materials. Larger kilns are often used in high-capacity cement plants, while smaller kilns may be employed in specialized applications or smaller-scale operations.
Key Points Explained:
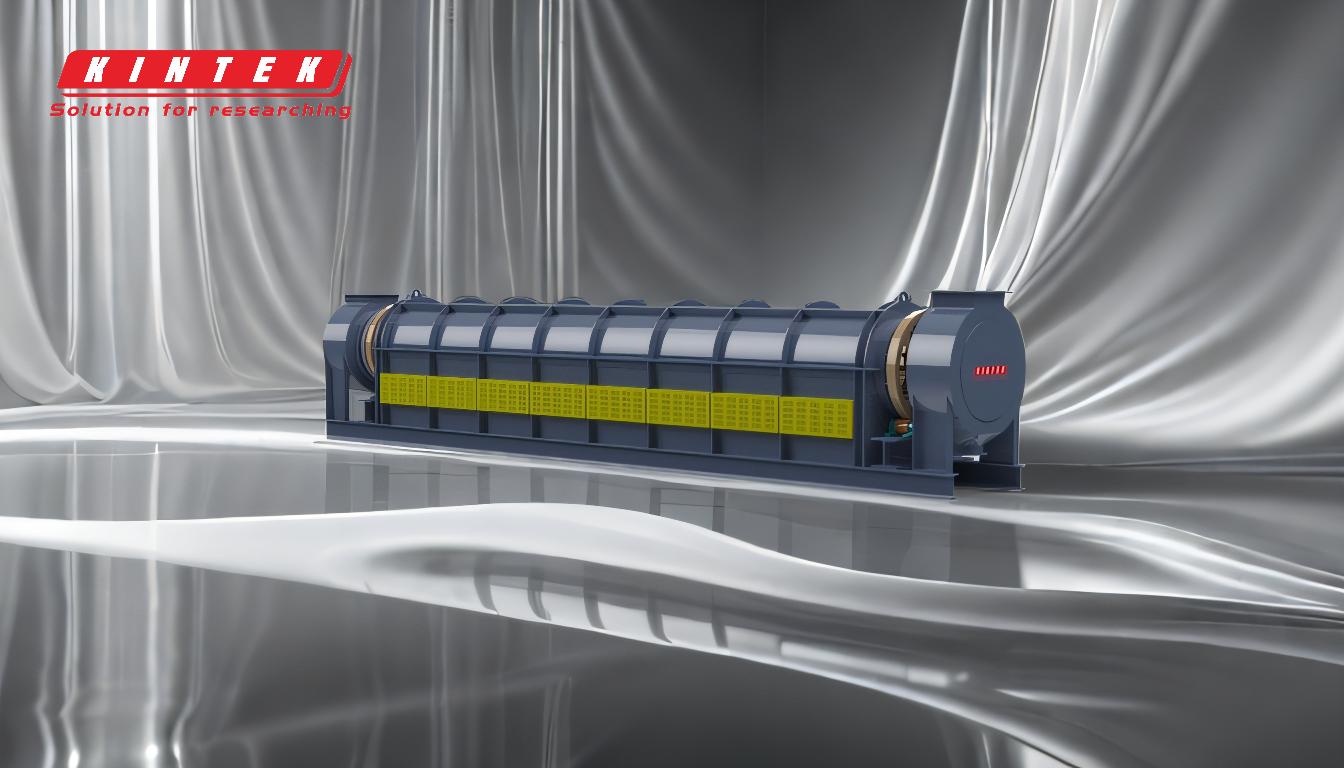
-
Typical Length Range of Cement Rotary Kilns:
- Cement rotary kilns are generally long structures, with lengths ranging from 50 meters to 230 meters.
- The length is determined by the production capacity, the type of cement being produced, and the specific chemical reactions required.
- Larger kilns are used in high-capacity cement plants, while smaller kilns are suitable for specialized or low-volume applications.
-
Structural Constraints on Kiln Length:
- The kiln shell is typically made from rolled mild steel plates, with thicknesses ranging from 15 to 30 mm.
- The upper limit on length (around 230 meters) is set by the structural integrity of the shell, as longer kilns are more prone to deformation under their own weight.
- The diameter of the kiln also plays a role in determining the maximum feasible length, with larger diameters requiring shorter lengths to maintain stability.
-
Length-to-Diameter (L/D) Ratio:
- The L/D ratio is a critical design parameter for rotary kilns, influencing heat distribution, material residence time, and overall efficiency.
- A higher L/D ratio generally allows for better heat transfer and more controlled chemical reactions, but it also increases the complexity and cost of the kiln.
- Typical L/D ratios for cement rotary kilns range from 15:1 to 40:1, depending on the specific application and design goals.
-
Impact of Kiln Length on Performance:
- Longer kilns provide greater residence time for materials, which is essential for completing the chemical reactions required in cement production.
- However, longer kilns also require more energy to operate and are more challenging to maintain and manage.
- The choice of kiln length is a balance between production capacity, energy efficiency, and operational feasibility.
-
Comparison with Other Types of Rotary Kilns:
- While cement rotary kilns are among the longest, other types of rotary kilns (e.g., those used for pyrolysis or biomass processing) may have shorter lengths.
- For example, pyrolysis rotary kilns are often designed for slow pyrolysis operations and may have lengths optimized for specific feedstocks and heat distribution requirements.
-
Design Considerations for Cement Rotary Kilns:
- The inclination angle and rotation speed of the kiln are adjusted to optimize material flow and heat distribution.
- Internal fixtures such as constriction dams and lifters are used to control the residence time and mixing of materials.
- The free board (open space above the material bed) and the shape of the free surface are influenced by operational requirements such as feed rate and material properties.
By understanding these key points, equipment purchasers can make informed decisions about the appropriate kiln length and design for their specific cement production needs. The choice of kiln length should align with production goals, energy efficiency targets, and operational constraints.
Summary Table:
Key Aspect | Details |
---|---|
Typical Length Range | 50 to 230 meters |
Structural Constraints | Shell thickness: 15-30mm; max length limited by structural integrity |
L/D Ratio | 15:1 to 40:1, influencing heat distribution and efficiency |
Impact on Performance | Longer kilns = greater residence time, higher energy use, and maintenance |
Design Considerations | Inclination angle, rotation speed, internal fixtures, and free board |
Need help selecting the right cement rotary kiln for your production needs? Contact our experts today!