Electric arc furnaces (EAFs) are widely used in the steelmaking industry due to their efficiency and cost-effectiveness, especially for small-scale operations. These furnaces rely on electricity to generate the heat required to melt scrap metal, which acts as the anode in the process. The amount of electricity consumed by an arc furnace depends on several factors, including the type of furnace, the size of the operation, and the specific materials being processed. Below, we break down the key aspects of electricity consumption in arc furnaces.
Key Points Explained:
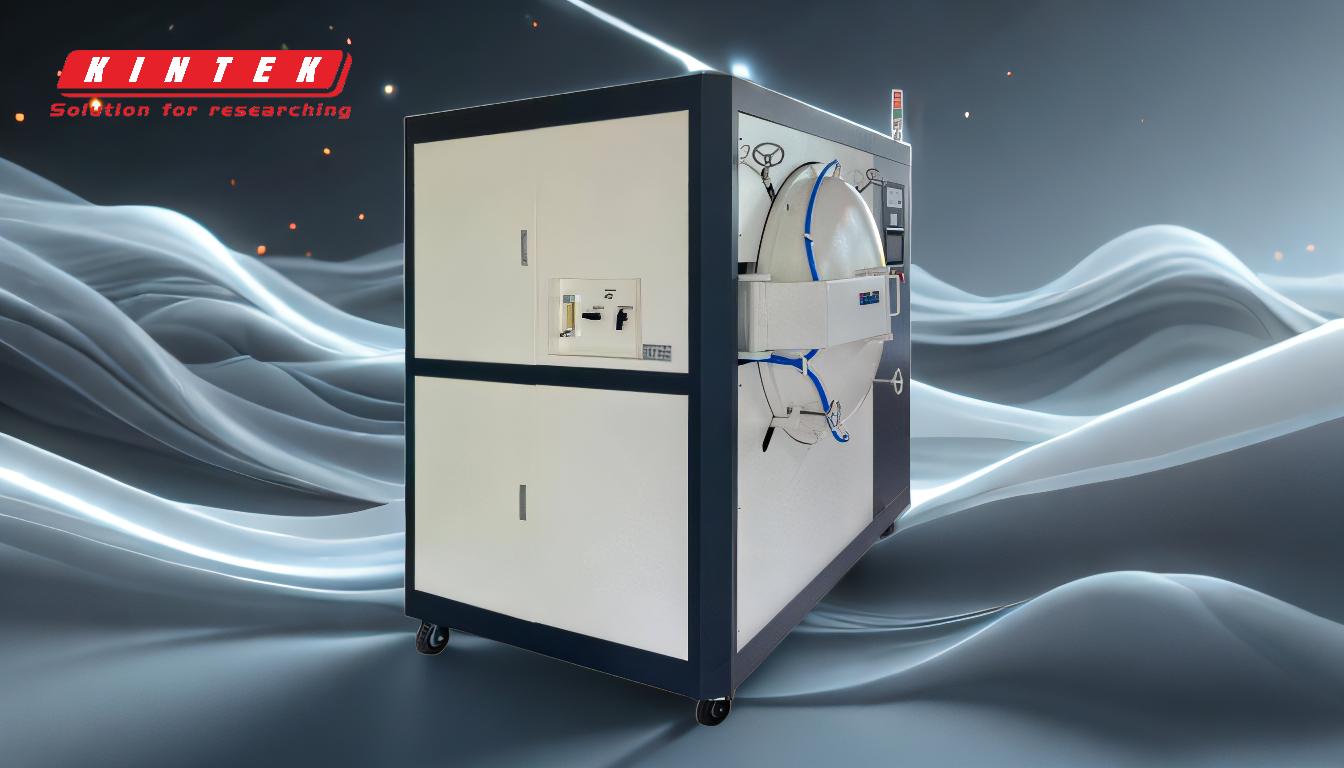
-
Electric Arc Furnace Operation and Electricity Consumption
- Electric arc furnaces use electricity to create an arc between graphite electrodes and the metal charge, generating intense heat to melt the scrap metal.
- The electricity consumption of an arc furnace is substantial, as it requires a significant amount of energy to heat the metal to its melting point.
- On average, an electric arc furnace consumes between 350 to 500 kWh (kilowatt-hours) of electricity per ton of steel produced. This range can vary depending on the efficiency of the furnace and the type of scrap metal being processed.
-
Factors Affecting Electricity Usage
- Furnace Size and Design: Larger furnaces or those with advanced designs may have better energy efficiency, reducing overall electricity consumption.
- Scrap Metal Quality: The type and quality of scrap metal used can influence energy requirements. Cleaner, higher-quality scrap typically requires less energy to melt compared to contaminated or lower-grade materials.
- Operational Practices: Efficient operational practices, such as preheating scrap metal or optimizing electrode positioning, can reduce electricity consumption.
- Power Supply and Voltage: The voltage and power supply configuration of the furnace also play a role in determining energy usage.
-
Cost-Effectiveness of Electric Arc Furnaces
- Despite their high electricity consumption, electric arc furnaces are considered cost-effective for small-scale operations because they can be quickly started and stopped, allowing for flexible production schedules.
- They are particularly advantageous for recycling scrap metal, as they eliminate the need for raw materials like iron ore and coke, which are required in traditional blast furnaces.
-
Environmental Impact and Energy Efficiency
- Electric arc furnaces are generally more environmentally friendly than blast furnaces because they produce fewer greenhouse gas emissions.
- Advances in technology, such as the use of renewable energy sources or energy recovery systems, are further improving the energy efficiency of these furnaces.
-
Comparison with Other Furnace Types
- Compared to blast furnaces, electric arc furnaces consume less energy overall, as they do not require the combustion of fossil fuels.
- However, they rely heavily on electricity, which can be a significant cost factor depending on local energy prices.
In summary, electric arc furnaces are a vital tool in modern steelmaking, offering flexibility and environmental benefits. While they consume a significant amount of electricity, their efficiency and cost-effectiveness make them a preferred choice for many operations. By optimizing furnace design, operational practices, and energy sources, the electricity consumption of arc furnaces can be further reduced, enhancing their sustainability and economic viability.
Summary Table:
Aspect | Details |
---|---|
Average Consumption | 350–500 kWh per ton of steel produced |
Factors Affecting Usage | Furnace size, scrap metal quality, operational practices, power supply |
Cost-Effectiveness | Flexible production, recyclability, reduced raw material dependency |
Environmental Impact | Lower greenhouse gas emissions compared to blast furnaces |
Energy Efficiency | Improved by renewable energy, energy recovery systems, and advanced design |
Discover how to optimize your arc furnace's energy efficiency—contact our experts today!