Methane pyrolysis is a process that decomposes methane (CH₄) into hydrogen (H₂) and solid carbon, typically requiring significant energy input. The energy requirement depends on factors such as the temperature, pressure, reaction kinetics, and the type of equipment used, such as a pyrolysis reactor. Generally, the process operates at high temperatures (around 750–1500°C) and may require energy inputs ranging from 40 to 100 kJ/mol of methane, depending on the efficiency of the system and the reaction conditions. The energy can be supplied through direct heating, plasma, or catalytic methods. The process is gaining attention as a cleaner alternative to steam methane reforming for hydrogen production, as it avoids CO₂ emissions.
Key Points Explained:
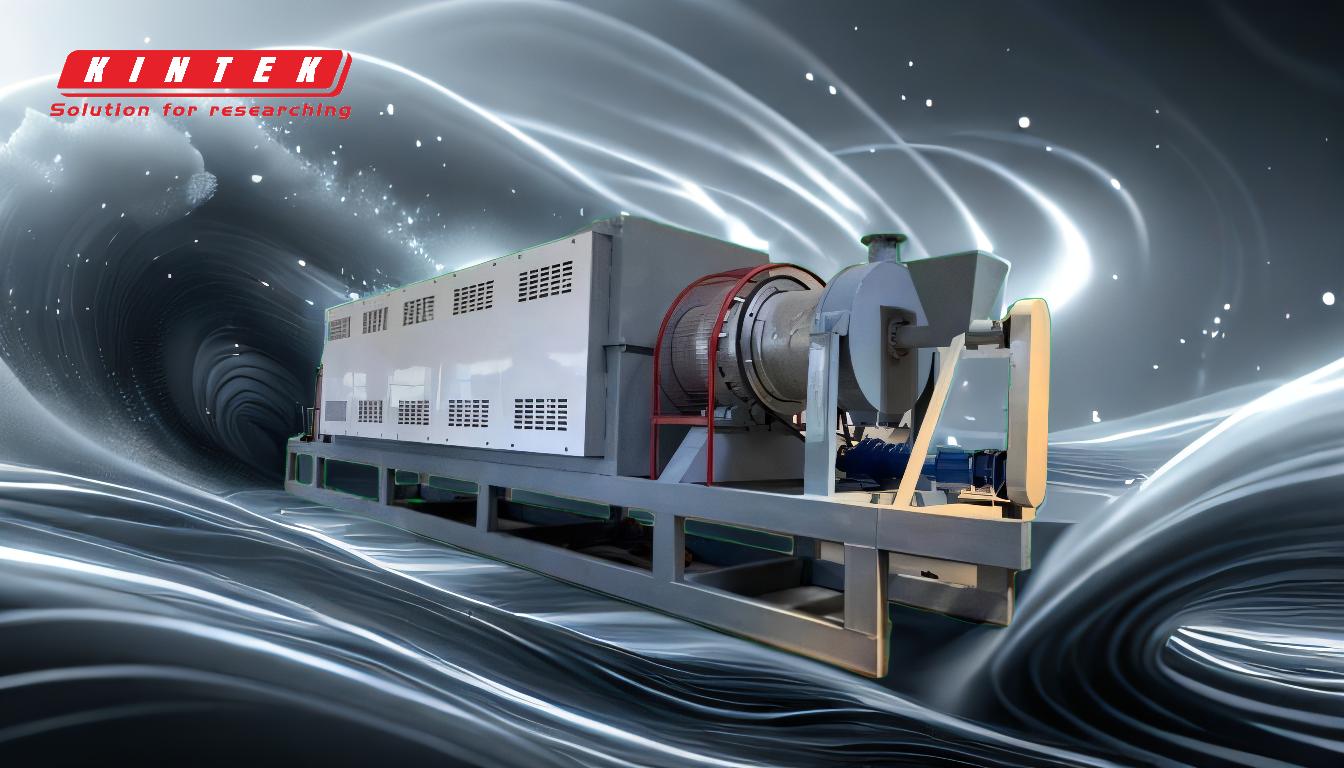
-
Energy Requirements for Methane Pyrolysis:
- Methane pyrolysis typically requires an energy input of 40–100 kJ/mol of methane, depending on the reaction conditions and the efficiency of the system.
- The energy is primarily used to break the C-H bonds in methane, which requires a temperature range of 750–1500°C.
- The energy can be supplied through various methods, including:
- Direct heating: Using external heat sources like electric furnaces or burners.
- Plasma-assisted pyrolysis: Utilizing plasma to provide high-energy conditions.
- Catalytic pyrolysis: Employing catalysts to lower the activation energy and reduce the overall energy requirement.
-
Factors Influencing Energy Consumption:
- Temperature: Higher temperatures generally increase reaction rates but also raise energy consumption.
- Pressure: Operating at elevated pressures can influence the reaction kinetics and energy requirements.
- Reactor design: The type of reactor, such as a pyrolysis reactor, plays a critical role in determining energy efficiency. Advanced designs aim to minimize heat losses and optimize heat transfer.
- Catalysts: The use of catalysts can significantly reduce the energy needed by lowering the activation energy of the reaction.
-
Comparison with Other Hydrogen Production Methods:
- Steam Methane Reforming (SMR): SMR is the most common method for hydrogen production but emits CO₂. Methane pyrolysis, in contrast, produces hydrogen without CO₂ emissions, making it a more environmentally friendly option.
- Electrolysis: While electrolysis uses electricity to split water into hydrogen and oxygen, methane pyrolysis can be more energy-efficient in regions with abundant natural gas.
-
Energy Sources for Pyrolysis:
- The energy for methane pyrolysis can come from renewable sources, such as solar or wind power, to further reduce the carbon footprint of the process.
- Alternatively, waste heat from industrial processes can be utilized to improve overall energy efficiency.
-
Challenges and Opportunities:
-
Challenges:
- High energy requirements and costs associated with maintaining high temperatures.
- Managing the solid carbon byproduct, which requires efficient separation and utilization strategies.
-
Opportunities:
- Integration with renewable energy sources to make the process more sustainable.
- Development of advanced reactors and catalysts to improve energy efficiency and reduce costs.
-
Challenges:
-
Applications and Future Prospects:
- Methane pyrolysis is gaining traction as a method for producing turquoise hydrogen, which is hydrogen produced without CO₂ emissions.
- The solid carbon byproduct can be used in various industries, such as construction, electronics, and materials manufacturing, adding value to the process.
- Ongoing research focuses on scaling up the technology and improving its economic viability.
In summary, methane pyrolysis is an energy-intensive process that requires careful optimization of reaction conditions and reactor design to minimize energy consumption. While it offers a cleaner alternative to traditional hydrogen production methods, further advancements in technology and renewable energy integration are needed to enhance its feasibility and sustainability.
Summary Table:
Aspect | Details |
---|---|
Energy Range | 40–100 kJ/mol of methane |
Temperature Range | 750–1500°C |
Energy Sources | Direct heating, plasma-assisted, catalytic methods |
Key Factors | Temperature, pressure, reactor design, catalysts |
Comparison with SMR | No CO₂ emissions, cleaner hydrogen production |
Challenges | High energy costs, solid carbon byproduct management |
Opportunities | Renewable energy integration, advanced reactor and catalyst development |
Interested in learning more about methane pyrolysis? Contact us today to explore how this technology can benefit your operations!