Chemical vapor deposition (CVD) is a widely used technique for synthesizing nanomaterials, offering high-quality, pure, and durable coatings. The process involves the transportation of gaseous reactants to a substrate, where they undergo adsorption, surface reactions, and nucleation to form a solid film. The by-products are then desorbed and removed from the system. CVD is versatile, capable of depositing materials like graphene, ceramics, and metals, and is valued for its ability to produce coatings with excellent mechanical and thermal properties. The process is divided into several steps, including reactant transport, adsorption, surface reactions, and by-product removal, ensuring precise control over film growth and composition.
Key Points Explained:
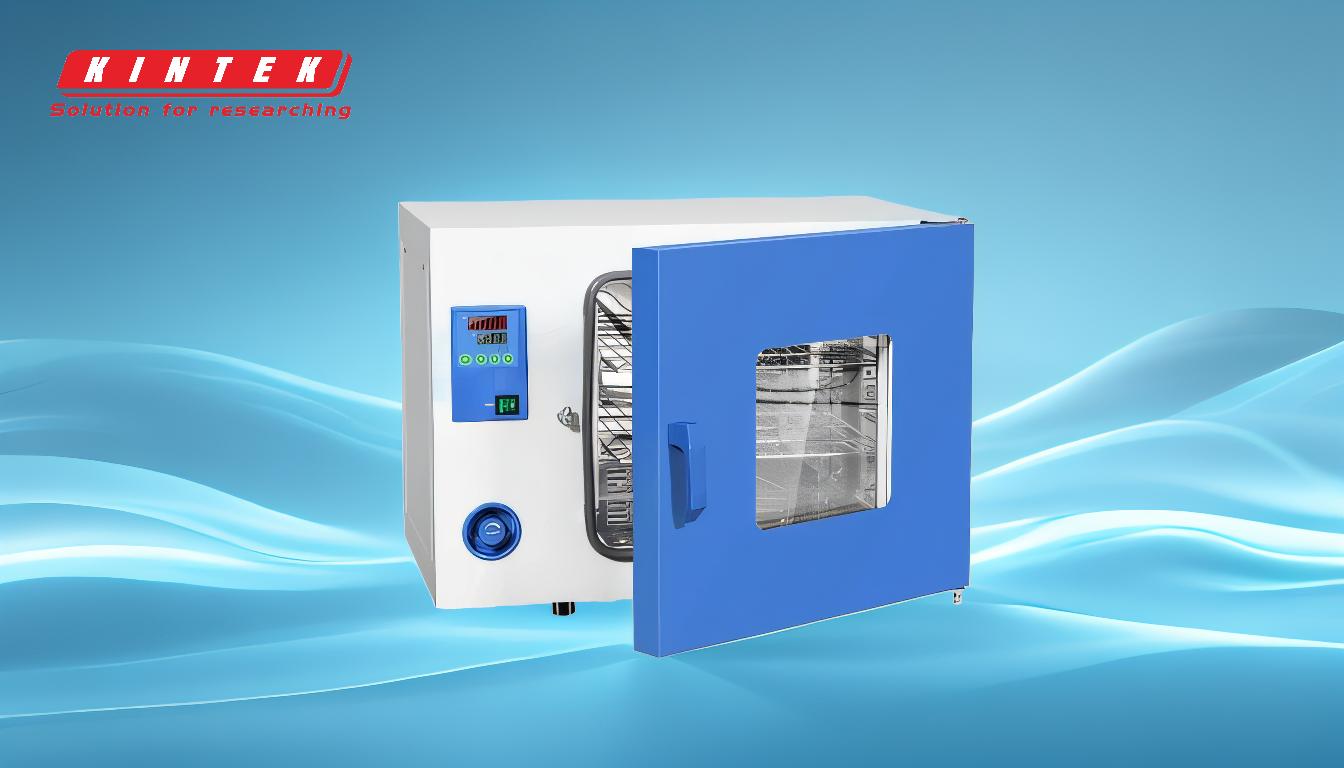
-
Transport of Reactants:
- The first step in CVD involves the transportation of gaseous reactants to the substrate surface. This can occur through convection or diffusion within the reaction chamber. The reactants are typically volatile compounds that can easily vaporize and move toward the substrate.
-
Adsorption on the Surface:
- Once the gaseous reactants reach the substrate, they adsorb onto its surface. This adsorption can be physical or chemical, depending on the nature of the reactants and the substrate. Adsorption is crucial as it prepares the reactants for subsequent surface reactions.
-
Surface Reactions:
- The adsorbed reactants undergo heterogeneous surface-catalyzed reactions. These reactions can involve decomposition, oxidation, reduction, or other chemical transformations, leading to the formation of solid film precursors. The reactions are often thermally driven, requiring precise temperature control.
-
Surface Diffusion and Nucleation:
- After the surface reactions, the resulting species diffuse across the substrate to find growth sites. Nucleation occurs at these sites, forming small clusters that grow into a continuous film. This step determines the microstructure and quality of the deposited material.
-
Film Growth:
- The nucleation sites grow into a thin film through the continuous addition of material. The growth rate and film properties depend on factors like temperature, pressure, and reactant concentration. CVD allows for the deposition of uniform and high-purity films.
-
Desorption of By-products:
- Volatile by-products generated during the surface reactions desorb from the substrate and are transported away from the reaction zone. This step ensures that the film remains free of contaminants and maintains its desired properties.
-
Removal of By-products:
- The gaseous by-products are removed from the reactor through convection and diffusion processes. Efficient removal is essential to maintain the purity of the deposited film and prevent unwanted reactions.
-
Advantages of CVD:
- CVD is valued for its ability to produce high-quality, durable coatings with excellent mechanical and thermal properties. It is versatile, capable of depositing a wide range of materials, including graphene, ceramics, and metals. The process can be tailored to achieve specific properties like corrosion resistance, abrasion resistance, or high purity.
-
Applications of CVD:
- CVD is used in various industries, including electronics, optics, and aerospace, for applications such as semiconductor fabrication, protective coatings, and thin-film deposition. Its ability to coat complex and precision surfaces makes it indispensable in advanced manufacturing.
By understanding these key steps and advantages, one can appreciate the precision and versatility of chemical vapor deposition in synthesizing nanomaterials. The process's ability to produce high-quality, durable, and tailored coatings makes it a cornerstone of modern material science and engineering.
Summary Table:
Step | Description |
---|---|
1. Transport of Reactants | Gaseous reactants are transported to the substrate via convection or diffusion. |
2. Adsorption | Reactants adsorb onto the substrate surface, preparing for surface reactions. |
3. Surface Reactions | Adsorbed reactants undergo decomposition, oxidation, or reduction reactions. |
4. Surface Diffusion | Resulting species diffuse to nucleation sites for film growth. |
5. Film Growth | Nucleation sites grow into a continuous, high-purity film. |
6. Desorption | Volatile by-products desorb from the substrate. |
7. Removal of By-products | By-products are removed from the reactor to maintain film purity. |
8. Advantages | High-quality, durable coatings with excellent mechanical and thermal properties. |
9. Applications | Used in electronics, optics, and aerospace for precision coatings. |
Unlock the potential of CVD for your projects—contact our experts today to learn more!