Thin film coatings are layers of material applied to a substrate, with thicknesses ranging from fractions of a nanometer (monolayer) to several micrometers. These coatings are used in a wide variety of applications, including decorative finishes, electrical coatings, and functional coatings, due to their properties such as transparency, durability, and conductivity. The specific thickness of a thin film coating depends on its intended application and the method of deposition used. Understanding the range of thicknesses and the factors influencing them is crucial for selecting the appropriate coating for a given purpose.
Key Points Explained:
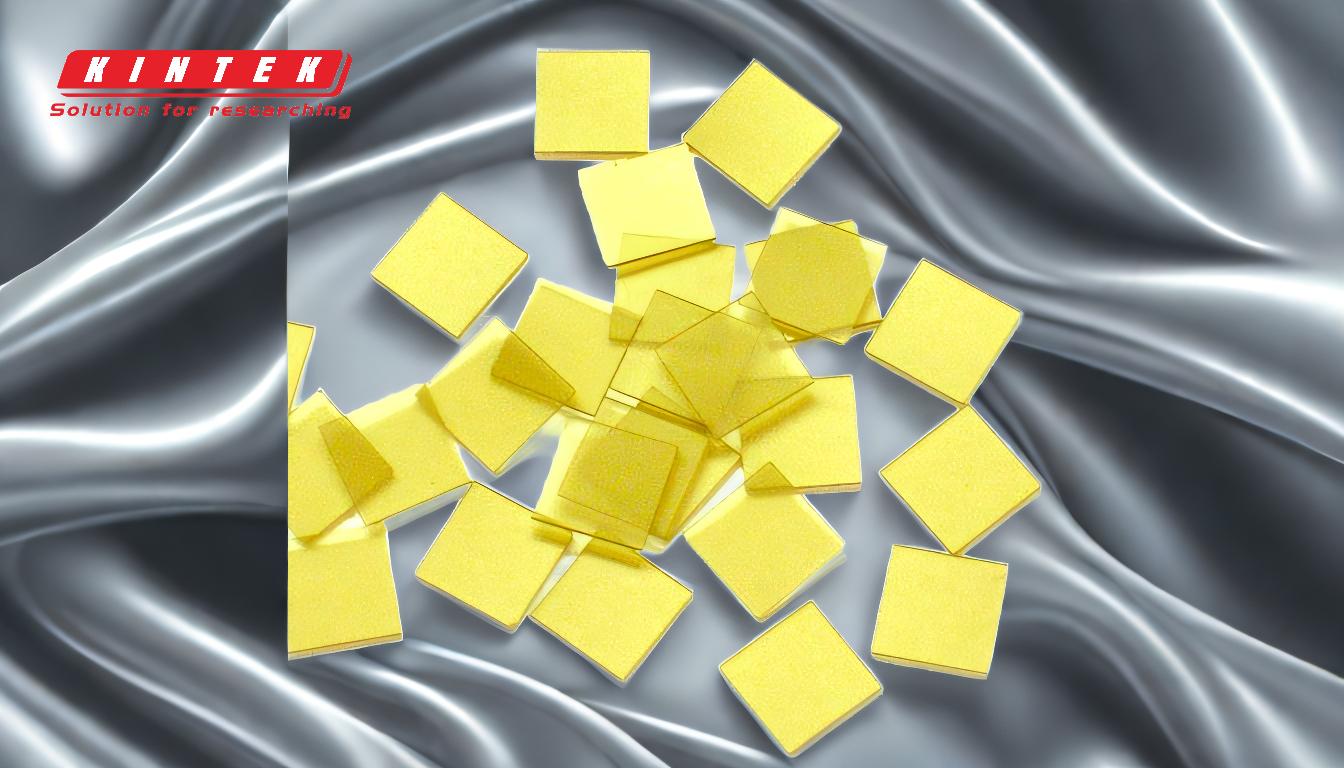
-
Definition and Range of Thin Film Thickness:
- Thin films are defined as layers of material with thicknesses ranging from fractions of a nanometer (monolayer) to several micrometers.
- The thickness can be as thin as just a few atoms, making them extremely thin compared to bulk materials.
- The range of thicknesses allows for a wide variety of applications, from nanotechnology to larger-scale industrial uses.
-
Applications and Characteristics:
- Thin film coatings are used in numerous applications, including decorative finishes, electrical coatings, and functional coatings.
- The characteristics of thin films, such as transparency, durability, and conductivity, make them suitable for specific uses.
- For example, some coatings are designed to be transparent for optical applications, while others may be used to enhance electrical conductivity or signal transmission.
-
Deposition Methods and Thickness Control:
- The thickness of thin film coatings is influenced by the deposition method used, such as physical vapor deposition (PVD) or chemical vapor deposition (CVD).
- These methods allow for precise control over the thickness, ranging from several angstroms to many microns.
- The choice of deposition method and parameters can be tailored to achieve the desired thickness and properties for a specific application.
-
Factors Influencing Thin Film Thickness:
- The intended application is a primary factor in determining the appropriate thickness of a thin film coating.
- The properties of the substrate material and the desired performance characteristics also play a significant role.
- For instance, a coating designed for scratch resistance may require a different thickness than one intended for electrical conductivity.
-
Measurement and Verification:
- Accurate measurement of thin film thickness is essential for ensuring the coating meets the required specifications.
- Techniques such as ellipsometry, profilometry, and X-ray reflectometry are commonly used to measure thin film thickness.
- Verification of thickness ensures the coating performs as expected in its intended application.
In summary, the thickness of a thin film coating can vary significantly, from fractions of a nanometer to several micrometers, depending on the application and deposition method. Understanding the range of thicknesses and the factors influencing them is crucial for selecting the appropriate coating for a given purpose. The ability to control and measure thin film thickness accurately is essential for ensuring the coating performs as expected in its intended application.
Summary Table:
Aspect | Details |
---|---|
Thickness Range | Fractions of a nanometer (monolayer) to several micrometers |
Applications | Decorative finishes, electrical coatings, functional coatings |
Key Characteristics | Transparency, durability, conductivity |
Deposition Methods | Physical Vapor Deposition (PVD), Chemical Vapor Deposition (CVD) |
Measurement Techniques | Ellipsometry, profilometry, X-ray reflectometry |
Need help selecting the right thin film coating for your application? Contact our experts today!