PVD (Physical Vapor Deposition) coatings are known for their thinness, typically ranging between 0.25 microns and 5 microns. This thin layer is sufficient to enhance material properties such as hardness, smoothness, and corrosion resistance without significantly altering the dimensions or appearance of the substrate. The precise thickness can vary depending on the application, with jewelry coatings often being on the lower end of the range (0.25-5 microns) and industrial applications sometimes requiring thicker coatings (up to 5 microns). PVD coatings are highly valued for their uniformity, adhesion, and environmental friendliness compared to traditional coating methods like electroplating.
Key Points Explained:
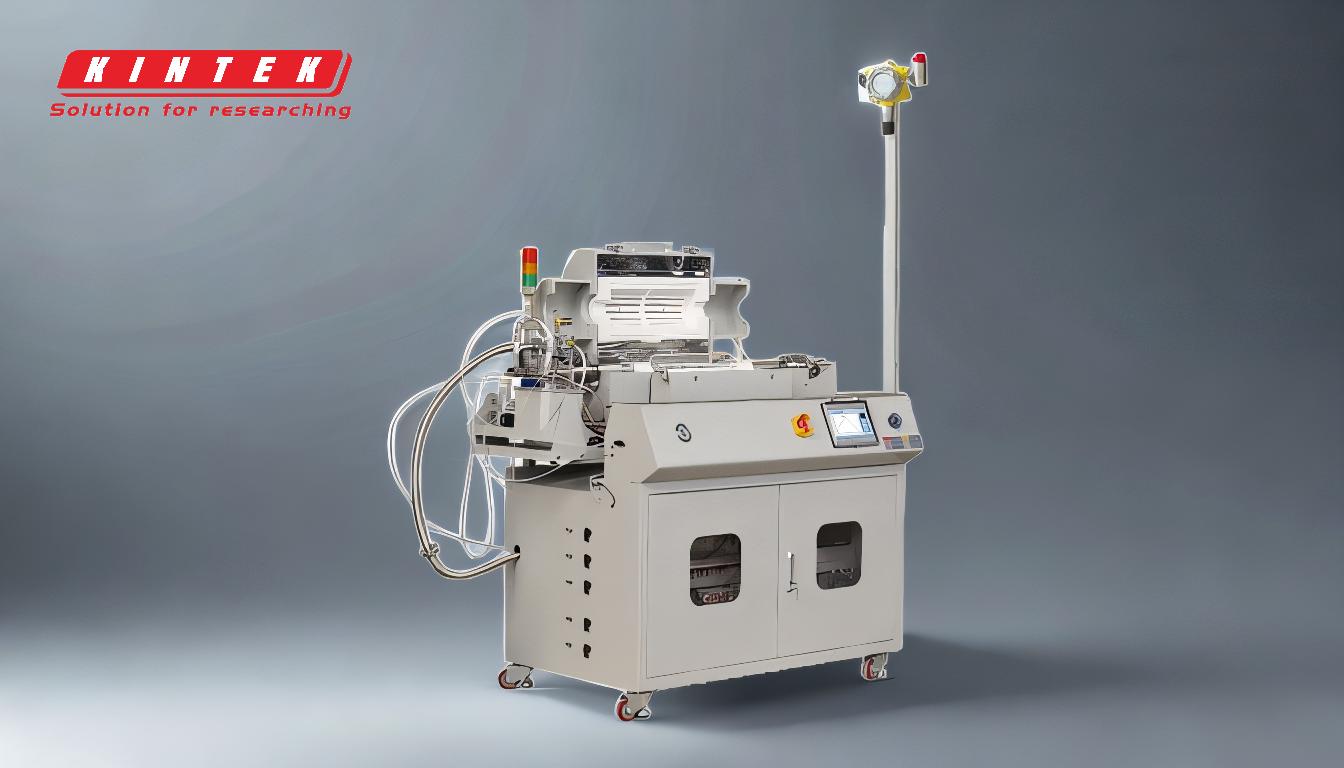
-
Typical Thickness Range:
- PVD coatings generally range from 0.25 microns to 5 microns in thickness. This range is consistent across various applications, including industrial components and jewelry.
- For example, jewelry coatings often fall within 0.25 to 5 microns, which is significantly thinner than the diameter of a human hair (about 70 microns).
-
Impact on Substrate Properties:
- The thinness of PVD coatings ensures that they do not alter the specifications or dimensions of engineered parts. This is crucial for precision components where even minor changes in size could affect performance.
- Despite their thinness, PVD coatings significantly enhance material properties such as:
- Hardness: PVD coatings are often harder than coatings applied by electroplating.
- Corrosion Resistance: They provide excellent protection against environmental degradation.
- Smoothness: The coatings improve surface finish without affecting the appearance.
-
Application-Specific Thickness:
- The required thickness of PVD coatings can vary depending on the application:
- For jewelry, coatings are typically on the thinner side (0.25-5 microns) to maintain aesthetic appeal and lightweight properties.
- For industrial applications, coatings may be closer to the upper end of the range (2-5 microns) to ensure durability and performance under harsh conditions.
- The required thickness of PVD coatings can vary depending on the application:
-
Comparison with Other Coating Methods:
- PVD coatings are thinner than those applied by CVD (Chemical Vapor Deposition), which typically range from 5-10 microns.
- PVD coatings are also more environmentally friendly compared to traditional electrochemical processes like electroplating, making them a preferred choice in many industries.
-
Uniformity and Adhesion:
- PVD coatings are characterized by their high purity and uniformity, ensuring consistent performance across the coated surface.
- They exhibit excellent adhesion to the substrate, which is critical for long-term durability and effectiveness.
-
Environmental Benefits:
- PVD coatings are considered environmentally friendly because they do not involve harmful chemicals or produce hazardous waste, unlike traditional coating methods.
In summary, the thickness of PVD coatings is a critical factor that balances performance enhancement with minimal impact on the substrate. Their thinness, combined with superior material properties and environmental benefits, makes PVD coatings a versatile and sustainable choice for a wide range of applications.
Summary Table:
Aspect | Details |
---|---|
Typical Thickness | 0.25 to 5 microns |
Applications | Jewelry (0.25-5 microns), Industrial (2-5 microns) |
Key Benefits | Hardness, corrosion resistance, smoothness, environmental friendliness |
Comparison to CVD | Thinner (CVD: 5-10 microns) |
Adhesion & Uniformity | High purity, excellent adhesion, uniform coating |
Interested in PVD coatings for your project? Contact us today to learn more!