The thickness of a plasma nitriding layer typically ranges from a few hundred nanometers to several microns, depending on the specific application and process parameters. Plasma nitriding is a surface hardening technique that enhances the wear resistance, fatigue strength, and corrosion resistance of metal components. The thickness of the nitrided layer is influenced by factors such as material composition, process temperature, duration, and the type of plasma used. For most industrial applications, the nitriding layer thickness is carefully controlled to ensure optimal performance without compromising the base material's integrity.
Key Points Explained:
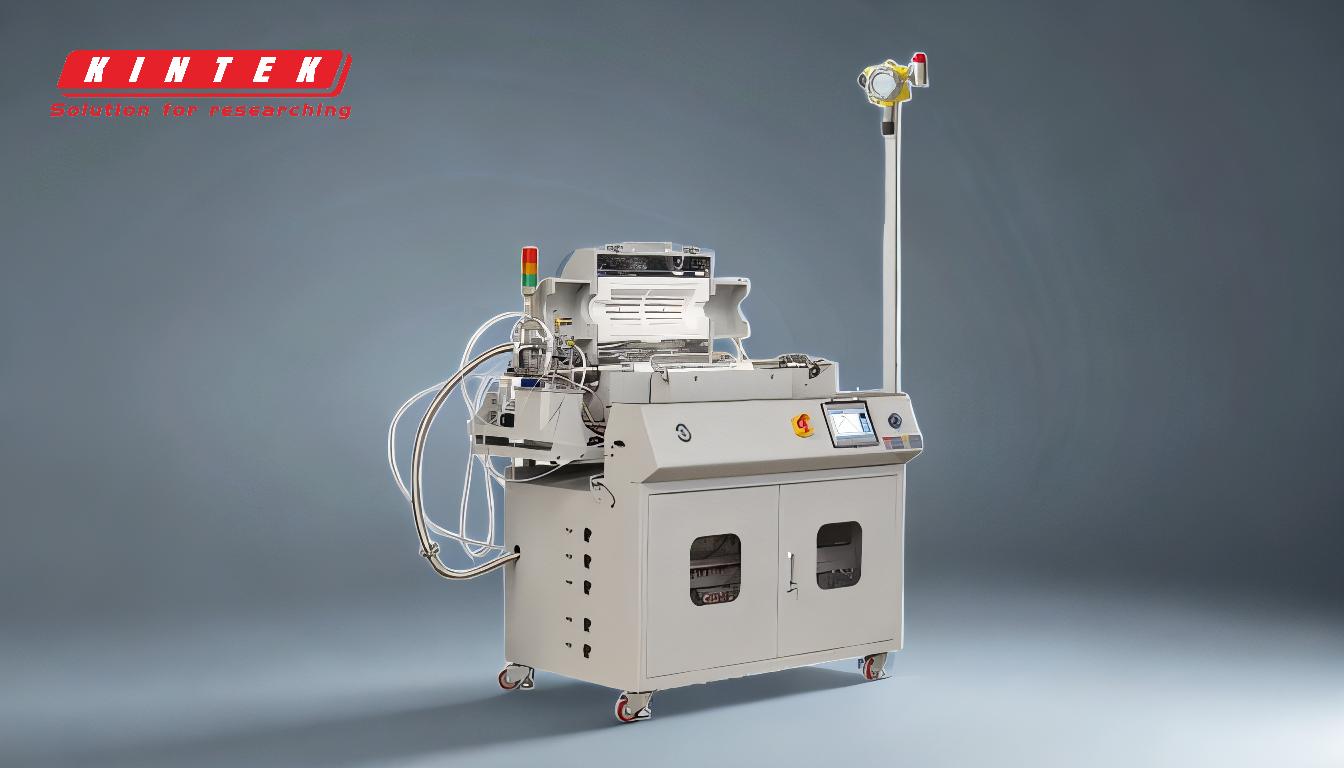
-
Typical Thickness Range:
- The plasma nitriding layer thickness generally ranges from 0.25 microns to 5 microns. This range is suitable for most industrial applications, providing a balance between surface hardness and component durability.
- In some cases, particularly for specialized applications, the thickness can extend up to 10 microns or more, depending on the material and process conditions.
-
Factors Influencing Thickness:
- Material Composition: The type of material being treated significantly affects the nitriding layer thickness. For example, steels with higher alloying elements tend to form thicker layers due to enhanced nitrogen diffusion.
- Process Temperature: Higher temperatures generally increase the diffusion rate of nitrogen, leading to thicker nitrided layers. However, excessively high temperatures can degrade the base material.
- Process Duration: Longer nitriding times allow for greater nitrogen diffusion, resulting in thicker layers. The relationship between time and thickness is often linear within a certain range.
- Plasma Parameters: The power, pressure, and composition of the plasma gas (e.g., nitrogen, hydrogen, or argon mixtures) influence the nitriding kinetics and, consequently, the layer thickness.
-
Measurement and Control:
- The thickness of the nitrided layer is typically measured using techniques such as microhardness testing, optical microscopy, or scanning electron microscopy (SEM). These methods provide accurate and reliable data for quality control.
- Precise control of the nitriding process is essential to achieve the desired layer thickness and uniformity. Advanced plasma nitriding systems often include real-time monitoring and feedback mechanisms to ensure consistent results.
-
Applications and Considerations:
- Wear Resistance: Thicker nitrided layers are often used in applications requiring high wear resistance, such as gears, bearings, and cutting tools.
- Fatigue Strength: For components subjected to cyclic loading, a carefully controlled nitriding layer can significantly enhance fatigue life.
- Corrosion Resistance: While plasma nitriding primarily improves wear resistance, it also provides some degree of corrosion resistance, particularly in combination with post-treatment processes like oxidation.
-
Comparison with Other Surface Treatments:
- Compared to other surface hardening techniques, such as carburizing or physical vapor deposition (PVD), plasma nitriding offers a unique combination of hardness, adhesion, and uniformity. The thickness of the nitrided layer is often more consistent and easier to control than in other methods.
By understanding these key points, equipment and consumable purchasers can make informed decisions about the plasma nitriding process, ensuring that the chosen parameters and equipment meet the specific requirements of their applications.
Summary Table:
Aspect | Details |
---|---|
Typical Thickness Range | 0.25 microns to 5 microns (up to 10 microns for specialized applications) |
Factors Influencing Thickness | Material composition, process temperature, duration, and plasma parameters |
Measurement Techniques | Microhardness testing, optical microscopy, SEM |
Key Applications | Wear resistance, fatigue strength, corrosion resistance |
Comparison with Other Methods | More consistent and easier to control than carburizing or PVD |
Need help optimizing your plasma nitriding process? Contact our experts today for tailored solutions!