Brazing and welding are both essential joining techniques in manufacturing and repair, but they differ significantly in terms of cost, application, and performance. Whether brazing is cheaper than welding depends on factors such as material compatibility, joint design, production volume, and the specific requirements of the application. Brazing is generally more cost-effective for certain scenarios, particularly when joining dissimilar metals or when heat distortion must be minimized. However, welding may be more economical for high-strength applications or large-scale production. Below, we explore the key factors that influence the cost comparison between brazing and welding.
Key Points Explained:
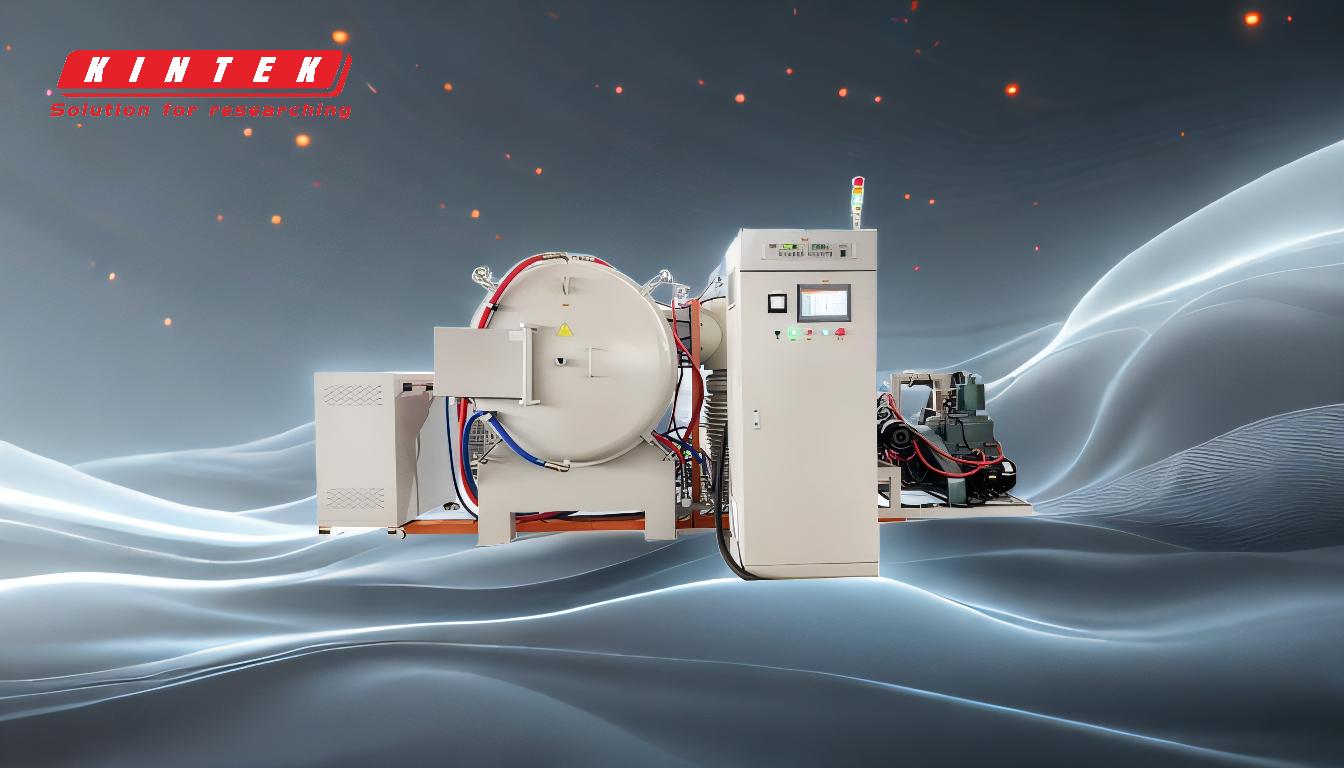
-
Material Costs:
- Brazing typically uses filler metals like silver, copper, or aluminum alloys, which can be expensive but are used in smaller quantities compared to welding consumables.
- Welding requires filler rods, wires, or electrodes, which may be cheaper per unit but are often used in larger volumes. The cost of shielding gases or fluxes in welding can also add to the expense.
-
Equipment Costs:
- Brazing equipment, such as torches or furnaces, is generally less expensive than welding equipment like arc welders or TIG/MIG machines.
- Welding setups often require more sophisticated machinery, including power supplies, cooling systems, and safety gear, which can significantly increase upfront costs.
-
Labor and Skill Requirements:
- Brazing is relatively easier to learn and perform, requiring less specialized training compared to welding. This reduces labor costs and training expenses.
- Welding demands higher skill levels and certifications, which can increase labor costs and the time required for training and execution.
-
Energy Consumption:
- Brazing operates at lower temperatures than welding, which reduces energy consumption and associated costs.
- Welding, especially processes like arc welding, consumes more energy due to higher heat requirements, leading to increased operational costs.
-
Joint Design and Application:
- Brazing is ideal for joining dissimilar metals or thin materials, where welding might cause distortion or require additional preparation. This makes brazing a cost-effective choice for specific applications.
- Welding is better suited for high-strength joints or heavy-duty applications, where the cost of welding may be justified by the performance requirements.
-
Production Volume and Speed:
- For high-volume production, welding can be more cost-effective due to faster cycle times and automation capabilities.
- Brazing is often slower and less suitable for mass production, making it more expensive in high-volume scenarios.
-
Post-Processing and Finishing:
- Brazed joints typically require minimal post-processing, reducing additional costs.
- Welded joints often need grinding, polishing, or heat treatment, which can increase overall expenses.
In conclusion, while brazing is generally cheaper in terms of equipment, labor, and energy costs, welding may be more economical for high-strength or high-volume applications. The choice between brazing and welding ultimately depends on the specific requirements of the project, including material compatibility, joint design, and production scale.
Summary Table:
Factor | Brazing | Welding |
---|---|---|
Material Costs | Uses expensive filler metals in smaller quantities. | Uses cheaper filler materials but in larger volumes. |
Equipment Costs | Less expensive equipment like torches or furnaces. | More expensive setups with arc welders, TIG/MIG machines, and safety gear. |
Labor Costs | Easier to learn, requiring less specialized training. | Demands higher skill levels and certifications, increasing labor costs. |
Energy Consumption | Operates at lower temperatures, reducing energy costs. | Higher heat requirements increase energy consumption. |
Joint Design | Ideal for dissimilar metals or thin materials, minimizing distortion. | Better for high-strength joints or heavy-duty applications. |
Production Volume | Slower and less suitable for mass production. | Faster cycle times and automation make it cost-effective for high volumes. |
Post-Processing | Minimal post-processing required. | Often requires grinding, polishing, or heat treatment. |
Still unsure which method is right for your project? Contact our experts today for personalized advice!