Calcination is a thermal treatment process used to decompose materials, typically at high temperatures, to drive off volatile components or induce chemical changes. While it is essential in industries like cement production, metal refining, and chemical manufacturing, its environmental impact is significant. The process releases greenhouse gases, particularly carbon dioxide (CO₂), and other pollutants, contributing to climate change and air quality degradation. Additionally, calcination consumes substantial energy, often derived from fossil fuels, further exacerbating its environmental footprint. Mitigation strategies, such as using alternative fuels, improving energy efficiency, and implementing carbon capture technologies, are being explored to reduce its negative effects.
Key Points Explained:
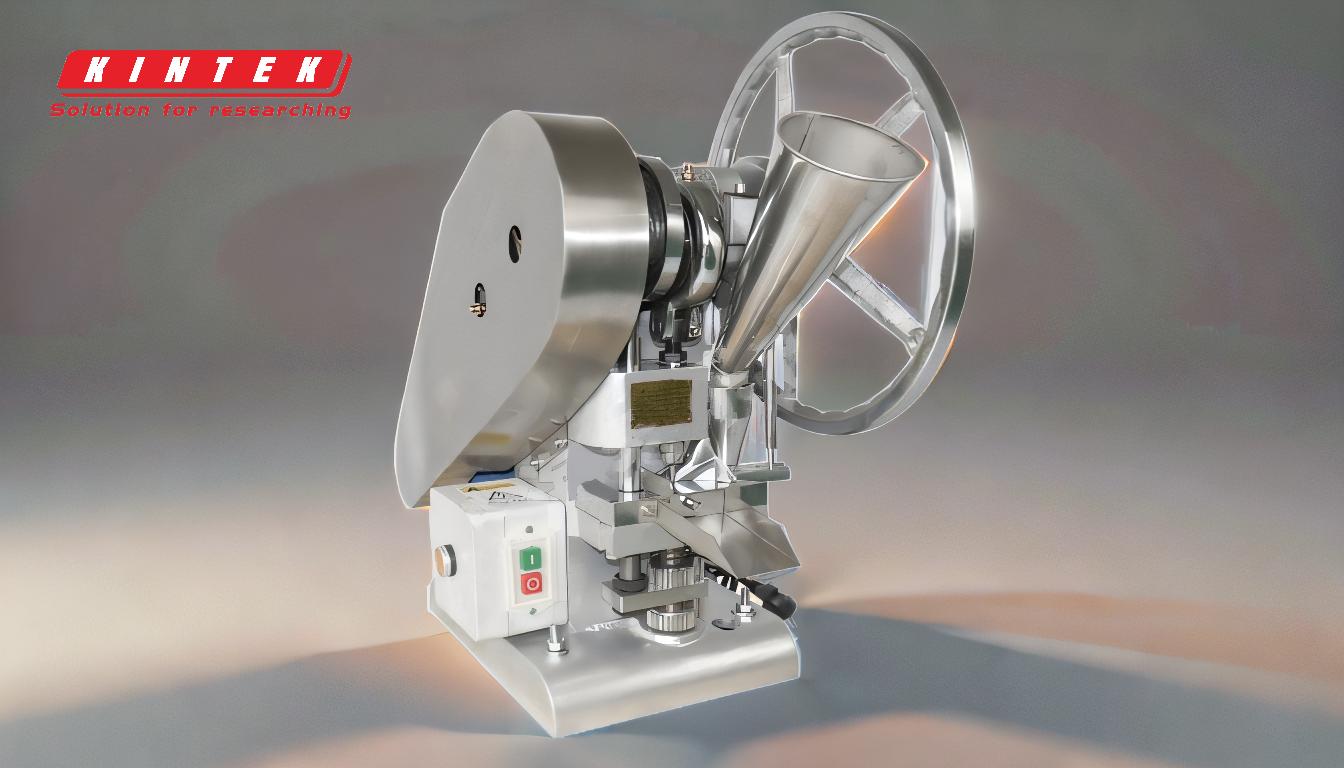
-
Definition and Purpose of Calcination:
- Calcination involves heating materials to high temperatures (typically 500–1200°C) in the absence or limited supply of air to induce thermal decomposition, remove volatile substances, or cause chemical transformations.
- It is widely used in industries such as cement production (to produce clinker), metal refining (to extract metals from ores), and chemical manufacturing (to produce lime or alumina).
-
Environmental Impact of Calcination:
-
Greenhouse Gas Emissions:
- Calcination releases significant amounts of CO₂, a major greenhouse gas. For example, in cement production, the chemical decomposition of limestone (CaCO₃ → CaO + CO₂) accounts for about 60% of the CO₂ emissions.
- These emissions contribute to global warming and climate change.
-
Air Pollution:
- The process can release other pollutants, such as sulfur oxides (SOₓ), nitrogen oxides (NOₓ), and particulate matter, which degrade air quality and harm human health.
-
Energy Consumption:
- Calcination requires high temperatures, often achieved by burning fossil fuels like coal or natural gas, leading to additional CO₂ emissions and resource depletion.
-
Greenhouse Gas Emissions:
-
Industry-Specific Environmental Concerns:
-
Cement Industry:
- Cement production is one of the largest sources of industrial CO₂ emissions, with calcination being a major contributor.
-
Metal Refining:
- Calcination of metal ores can release toxic byproducts, such as arsenic or mercury, depending on the ore composition.
-
Chemical Manufacturing:
- The production of lime (CaO) and alumina (Al₂O₃) through calcination also generates significant CO₂ emissions.
-
Cement Industry:
-
Mitigation Strategies:
-
Alternative Fuels:
- Using renewable energy sources or waste-derived fuels can reduce the carbon footprint of calcination.
-
Energy Efficiency:
- Improving the design of kilns and furnaces to reduce energy consumption can lower emissions.
-
Carbon Capture and Storage (CCS):
- Capturing CO₂ emissions from calcination processes and storing them underground can mitigate climate impact.
-
Material Substitution:
- Developing alternative materials or processes that require less calcination can reduce environmental harm.
-
Alternative Fuels:
-
Broader Implications:
- The environmental impact of calcination is a critical concern for industries striving to meet sustainability goals and regulatory requirements.
- Addressing these impacts requires a combination of technological innovation, policy support, and industry collaboration.
In summary, while calcination is an essential industrial process, its environmental consequences, particularly CO₂ emissions and energy consumption, are significant. However, advancements in technology and sustainable practices offer pathways to mitigate these impacts and align industrial activities with environmental goals.
Summary Table:
Aspect | Details |
---|---|
Definition | Heating materials at high temperatures (500–1200°C) to induce decomposition. |
Key Industries | Cement production, metal refining, chemical manufacturing. |
Environmental Impact | - Releases CO₂ and pollutants like SOₓ, NOₓ, and particulate matter. |
- High energy consumption, often from fossil fuels. | |
Mitigation Strategies | - Alternative fuels, energy efficiency, carbon capture, material substitution. |
Broader Implications | Critical for sustainability goals and regulatory compliance. |
Learn how to reduce the environmental impact of calcination—contact our experts today for sustainable solutions!