Diamond coating and ceramic coating are not the same, although they share some similarities in properties like hardness and durability. Diamond coatings are made of carbon atoms arranged in a diamond crystal structure, providing exceptional hardness, thermal conductivity, and chemical resistance. Ceramic coatings, on the other hand, are typically made of metal oxides, carbides, or nitrides, offering high hardness and wear resistance but differing in composition and specific properties. While both are used for protective and functional purposes, their material composition, deposition methods, and performance characteristics make them distinct.
Key Points Explained:
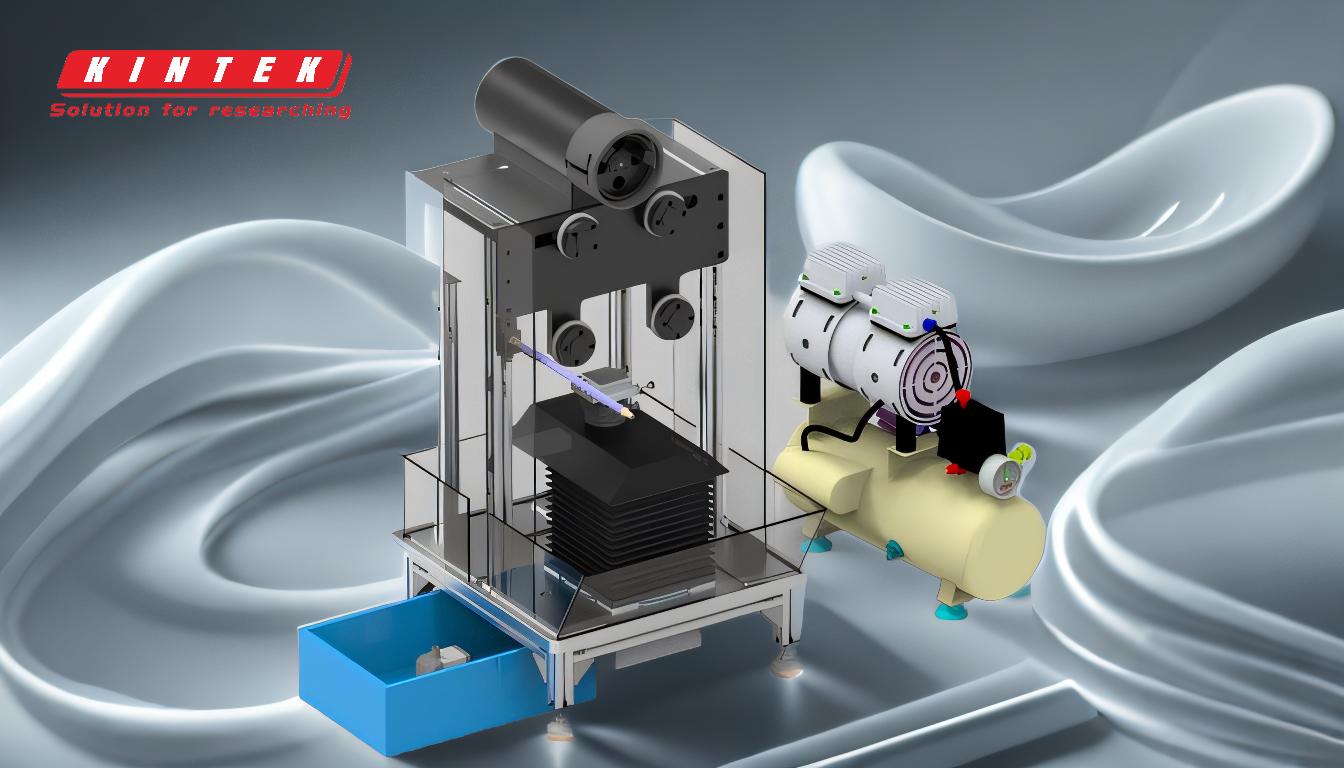
-
Material Composition:
- Diamond Coating: Composed of carbon atoms arranged in a diamond crystal lattice, giving it unparalleled hardness and thermal conductivity. It is chemically inert and resistant to wear.
- Ceramic Coating: Made from metal oxides, carbides, or nitrides (e.g., aluminum oxide, silicon carbide, or titanium nitride). These materials are hard and durable but differ significantly in structure and properties from diamond.
-
Properties:
-
Diamond Coating:
- Extremely high hardness (close to natural diamond).
- Excellent thermal conductivity, making it suitable for heat dissipation applications.
- Chemically inert, resistant to corrosion and wear.
-
Ceramic Coating:
- High hardness and wear resistance, though generally less than diamond.
- Good thermal and electrical insulation properties.
- Resistant to oxidation and corrosion, but not as chemically inert as diamond.
-
Diamond Coating:
-
Deposition Methods:
- Diamond Coating: Typically applied using chemical vapor deposition (CVD) or physical vapor deposition (PVD) techniques. The process involves precise control of gas phase composition and deposition parameters to tailor properties like grain size and surface roughness.
- Ceramic Coating: Applied using methods such as thermal spraying, plasma spraying, or PVD/CVD. The process varies depending on the specific ceramic material and application requirements.
-
Applications:
- Diamond Coating: Used in high-performance applications such as cutting tools, wear-resistant surfaces, and heat sinks. Its exceptional properties make it ideal for extreme conditions.
- Ceramic Coating: Commonly used in industries like aerospace, automotive, and manufacturing for wear protection, thermal barrier coatings, and electrical insulation.
-
Cost and Accessibility:
- Diamond Coating: Generally more expensive due to the complexity of the deposition process and the high cost of raw materials. It is used in specialized applications where its unique properties are essential.
- Ceramic Coating: More cost-effective and widely available, making it suitable for a broader range of industrial applications.
In summary, while both diamond and ceramic coatings offer high hardness and durability, they differ in material composition, properties, deposition methods, and applications. Diamond coatings are superior in terms of hardness and thermal conductivity but are more expensive and specialized. Ceramic coatings, on the other hand, are more versatile and cost-effective, making them suitable for a wider range of uses.
Summary Table:
Aspect | Diamond Coating | Ceramic Coating |
---|---|---|
Material Composition | Carbon atoms in a diamond crystal lattice | Metal oxides, carbides, or nitrides (e.g., aluminum oxide, silicon carbide) |
Properties | - Extremely high hardness - Excellent thermal conductivity - Chemically inert |
- High hardness - Good thermal/electrical insulation - Resistant to oxidation |
Deposition Methods | CVD or PVD | Thermal spraying, plasma spraying, or PVD/CVD |
Applications | Cutting tools, wear-resistant surfaces, heat sinks | Aerospace, automotive, manufacturing (wear protection, thermal barriers) |
Cost | Expensive and specialized | Cost-effective and widely available |
Need help choosing the right coating for your application? Contact our experts today!