Diamond coatings, particularly diamond-like carbon (DLC) coatings, are highly regarded for their exceptional properties, such as high hardness, durability, low friction, and chemical inertness. These coatings are widely used in industries where wear resistance, thermal conductivity, and surface performance are critical. However, determining whether diamond coatings are "worth it" depends on the specific application, budget, and performance requirements. While they offer significant advantages in terms of longevity and performance, their higher cost and specialized application processes may not justify their use in all scenarios. Below, we explore the key factors to consider when evaluating the value of diamond coatings.
Key Points Explained:
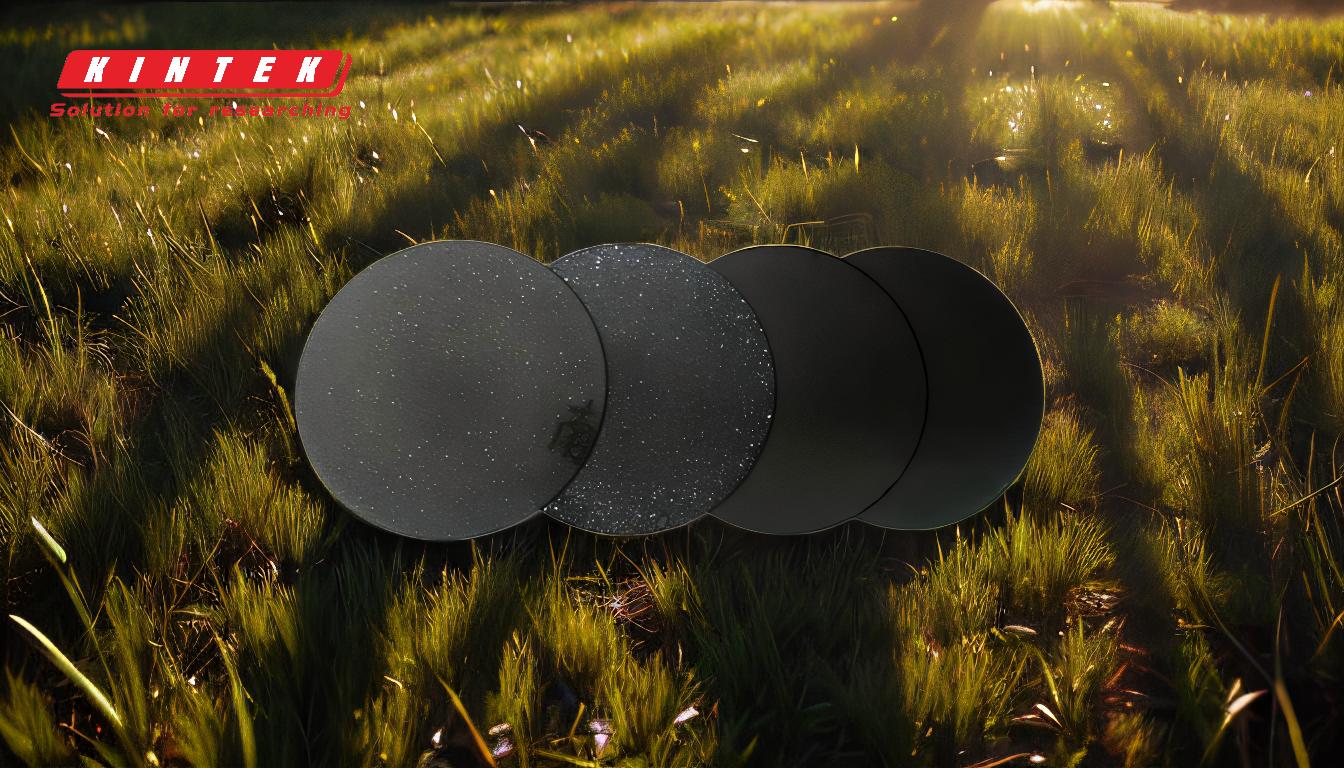
-
Exceptional Durability and Wear Resistance
- Diamond coatings are known for their extreme hardness, which makes them highly resistant to wear and abrasion. This is particularly beneficial in applications involving high friction or mechanical stress, such as cutting tools, bearings, and industrial machinery.
- The durability of diamond coatings can significantly extend the lifespan of components, reducing the need for frequent replacements and maintenance.
- Example: In cutting tools, diamond coatings can improve tool life by up to 10 times compared to uncoated tools, making them cost-effective in the long run for high-volume or precision machining operations.
-
Low Friction and Improved Performance
- Diamond-like carbon (DLC) coatings are specifically engineered to reduce friction, which enhances the efficiency and performance of moving parts.
- Low friction properties are particularly valuable in automotive and aerospace applications, where reducing energy loss and improving fuel efficiency are critical.
- Example: DLC-coated engine components, such as piston rings and camshafts, can reduce friction and improve overall engine performance, leading to better fuel economy and lower emissions.
-
Thermal Conductivity and Heat Management
- Diamond coatings have excellent thermal conductivity, which helps dissipate heat efficiently. This property is advantageous in high-temperature applications, such as electronics, where heat management is crucial for performance and reliability.
- By preventing overheating, diamond coatings can enhance the performance and lifespan of heat-sensitive components.
- Example: In electronic devices, diamond-coated heat sinks can improve thermal management, ensuring stable operation under demanding conditions.
-
Chemical Inertness and Corrosion Resistance
- Diamond coatings are chemically inert, meaning they resist reactions with most chemicals, acids, and bases. This makes them ideal for use in corrosive environments, such as chemical processing or marine applications.
- Their resistance to corrosion ensures that coated components maintain their integrity and performance over time, even in harsh conditions.
- Example: Diamond-coated valves and pumps used in chemical processing plants can withstand exposure to aggressive chemicals, reducing downtime and maintenance costs.
-
Tailorable Properties for Specific Applications
- The quality and characteristics of diamond coatings, such as grain size, surface roughness, and crystallinity, can be customized by adjusting deposition parameters and gas phase composition during the coating process.
- This flexibility allows manufacturers to optimize coatings for specific applications, ensuring the best possible performance.
- Example: For medical devices, diamond coatings can be tailored to provide both biocompatibility and wear resistance, making them suitable for implants and surgical instruments.
-
Cost Considerations
- While diamond coatings offer numerous benefits, they are generally more expensive than traditional coatings due to the specialized equipment and processes required for deposition.
- The higher upfront cost may not be justified for applications where lower-cost alternatives, such as titanium nitride (TiN) or chromium nitride (CrN) coatings, can provide adequate performance.
- Example: For low-volume or less demanding applications, the cost of diamond coatings may outweigh their benefits, making them less economically viable.
-
Application-Specific Value
- The value of diamond coatings depends heavily on the specific application and performance requirements. In high-performance or high-stress environments, the long-term benefits of reduced wear, improved efficiency, and extended component life often justify the initial investment.
- However, for applications with lower performance demands or budget constraints, alternative coatings may be more cost-effective.
- Example: In consumer products, such as kitchen knives or watch components, diamond coatings can enhance durability and aesthetics, but the added cost may not always align with consumer expectations or price points.
In conclusion, diamond coatings are worth considering for applications where their unique properties—such as exceptional durability, low friction, thermal conductivity, and chemical resistance—can provide significant advantages. However, their higher cost and specialized application requirements mean they are not universally suitable. Careful evaluation of the specific needs, performance goals, and budget constraints is essential to determine whether diamond coatings are the right choice for a given application.
Summary Table:
Key Property | Benefits | Applications |
---|---|---|
Durability & Wear Resistance | Extreme hardness, reduces wear, extends component lifespan | Cutting tools, bearings, industrial machinery |
Low Friction | Enhances efficiency, improves performance of moving parts | Automotive (piston rings, camshafts), aerospace |
Thermal Conductivity | Efficient heat dissipation, prevents overheating | Electronics (heat sinks), high-temperature environments |
Chemical Inertness | Resists corrosion, maintains performance in harsh conditions | Chemical processing, marine applications |
Tailorable Properties | Customizable grain size, surface roughness, and crystallinity | Medical devices (implants, surgical instruments) |
Cost Considerations | Higher upfront cost, but cost-effective for high-performance applications | High-volume machining, precision tools |
Interested in diamond coatings for your application? Contact us today to discuss your needs and explore the best solutions!