Gold coating is often necessary for SEM (Scanning Electron Microscopy) when analyzing non-conductive or poorly conductive samples. This is because the electron beam in SEM can cause charging effects on such samples, leading to image distortion and artifacts. Gold coating provides a conductive layer that helps dissipate the charge, improving image quality and resolution. While gold is a common choice due to its high conductivity and fine grain size, platinum is sometimes preferred for ultrahigh-resolution applications. The decision to use gold coating depends on the sample's conductivity, the SEM mode, and the desired resolution.
Key Points Explained:
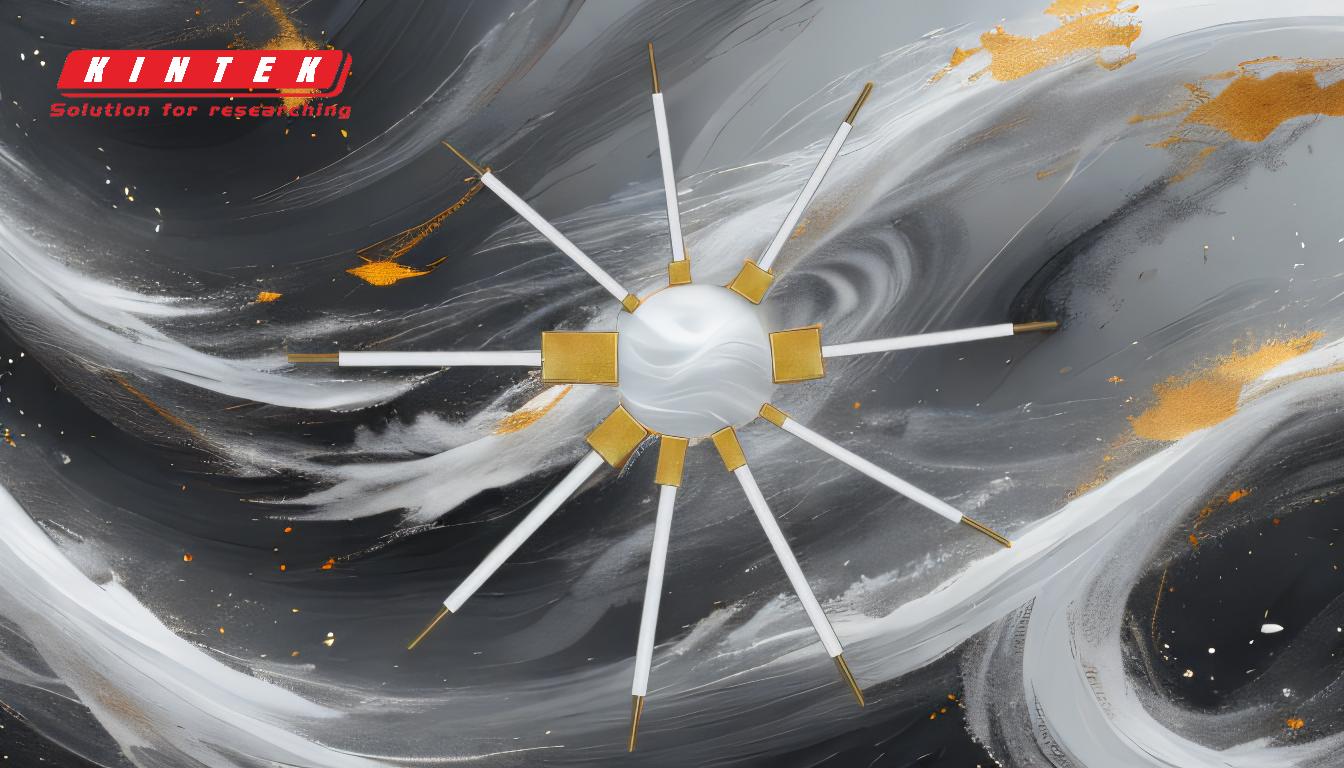
-
Why Conductive Coating is Necessary in SEM:
- In conventional SEM mode, which operates under high vacuum and high voltage, non-conductive or poorly conductive samples can accumulate charge when exposed to the electron beam. This charging effect can distort the image and create artifacts, making it difficult to obtain clear and accurate results.
- A conductive coating, such as gold, helps to dissipate this charge, ensuring that the electron beam interacts uniformly with the sample surface. This improves the quality of the secondary electron emission, which is crucial for high-resolution imaging.
-
Advantages of Gold Coating:
- High Conductivity: Gold is an excellent conductor of electricity, making it ideal for preventing charging effects in SEM.
- Small Grain Size: The fine grain size of gold ensures that the coating does not obscure the fine details of the sample, which is essential for high-resolution imaging.
- Reliability and Uniformity: Gold coating has been used for a long time in SEM applications, and its reliability is well-established. It provides uniform coverage, even in recessed areas of the sample, ensuring consistent conductivity across the surface.
- Flexibility: Gold coating can be applied in varying thicknesses, allowing for customization based on the specific requirements of the sample and the SEM analysis.
- Lower Energy Consumption: Compared to other coating methods like PVD (Physical Vapor Deposition), gold coating requires less energy, making it a more cost-effective option.
-
When Platinum Coating is Preferred:
- While gold is commonly used, platinum coating is sometimes preferred, especially in ultrahigh-resolution applications involving Field Emission Gun SEM (FEG-SEM). Platinum has an even smaller grain size than gold, which can enhance edge resolution and provide better image quality in high-magnification imaging.
- Platinum is also more resistant to oxidation and contamination, making it suitable for long-duration imaging sessions or when working with samples that may be exposed to harsh environments.
-
Considerations for Choosing Between Gold and Platinum:
- Sample Conductivity: If the sample is highly conductive, a coating may not be necessary. However, for non-conductive or poorly conductive samples, a coating is essential.
- Resolution Requirements: For standard SEM applications, gold coating is usually sufficient. However, for ultrahigh-resolution imaging, platinum may be the better choice due to its finer grain size.
- Cost and Availability: Gold is generally more cost-effective and widely available compared to platinum. However, if the application demands the highest possible resolution, the additional cost of platinum may be justified.
-
Alternative Coating Methods:
- While sputter coating with gold or platinum is the most common method, other techniques like PVD can also be used. However, PVD typically requires higher temperatures and energy consumption, making it less efficient for some applications.
- The choice of coating method should consider the specific requirements of the sample, the SEM mode, and the desired outcome in terms of image quality and resolution.
In summary, gold coating is often necessary for SEM to prevent charging effects and improve image quality, especially for non-conductive samples. While gold is the most commonly used material due to its conductivity and fine grain size, platinum may be preferred for ultrahigh-resolution applications. The choice between gold and platinum depends on the sample's properties, the SEM mode, and the resolution requirements.
Summary Table:
Key Considerations | Details |
---|---|
Why Conductive Coating is Needed | Prevents charging effects, reduces image distortion, and improves resolution. |
Advantages of Gold Coating | High conductivity, small grain size, uniform coverage, and cost-effectiveness. |
When Platinum is Preferred | Ultrahigh-resolution applications, finer grain size, and resistance to oxidation. |
Factors to Consider | Sample conductivity, resolution needs, and cost vs. performance trade-offs. |
Need help choosing the right coating for your SEM analysis? Contact our experts today for personalized advice!