Physical vapor deposition (PVD) is generally considered a safe process, especially when compared to chemical vapor deposition (CVD), which involves the use of potentially hazardous chemicals. PVD does not typically involve toxic chemicals, making it safer for operators and the environment. However, safety risks still exist, primarily related to the handling of high-energy processes, vacuum systems, and potential gas hazards. Proper ventilation, equipment maintenance, and adherence to safety protocols are essential to mitigate these risks. Below, we explore the safety aspects of PVD in detail.
Key Points Explained:
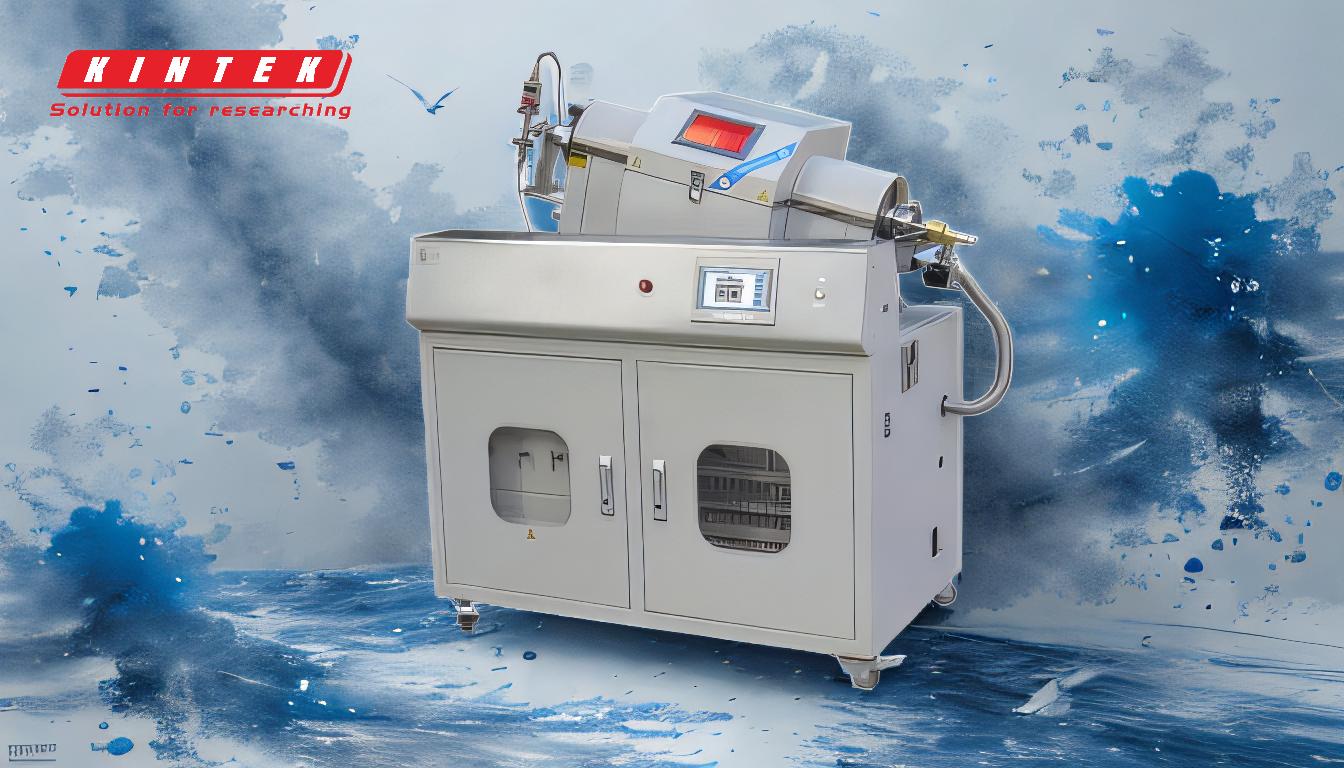
-
Absence of Toxic Chemicals in PVD
- Unlike CVD, which uses corrosive, flammable, and toxic gases, PVD operates in a vacuum environment and does not rely on chemical reactions. This eliminates the risks associated with handling and disposing of hazardous chemicals.
- The primary materials used in PVD, such as metals and ceramics, are generally inert and pose minimal health risks when handled correctly.
-
Risk of Explosion and Gas Hazards
- While PVD does not involve toxic chemicals, certain gases (e.g., argon or nitrogen) used in the process can pose explosion risks if not properly managed. Adequate ventilation and gas monitoring systems are critical to prevent the buildup of hazardous gas concentrations.
- The vacuum chamber must be maintained and inspected regularly to ensure there are no leaks or malfunctions that could lead to unsafe conditions.
-
High-Energy Processes and Equipment Safety
- PVD involves high-energy processes, such as sputtering or evaporation, which generate heat and require significant electrical power. Operators must be trained to handle high-voltage equipment and follow safety protocols to avoid electrical hazards.
- Proper grounding and shielding of equipment are necessary to prevent accidental exposure to high-energy particles or radiation.
-
Plasma-Assisted PVD (PAPVD) and Advanced Technologies
- Modern PVD techniques, such as plasma-assisted PVD (PAPVD), use advanced power sources like direct current (DC), radio-frequency (RF), or pulsed plasma. These technologies require specialized knowledge and safety measures to operate safely.
- Operators must be trained to handle the specific risks associated with these technologies, including plasma generation and ion beam-assisted coatings.
-
Handling of Powdery and Crumbly Substances
- Although PVD does not typically produce powdery or crumbly substances, any byproducts or residues from the process should be handled with care. Proper cleaning and disposal procedures must be followed to prevent contamination or inhalation hazards.
-
Ventilation and Environmental Controls
- Adequate ventilation is essential to maintain a safe working environment during PVD. This includes ensuring that any gases or particles released during the process are effectively captured and filtered.
- Environmental controls, such as fume extraction systems and air quality monitoring, help minimize exposure to any potential hazards.
-
Training and Safety Protocols
- Comprehensive training for operators is crucial to ensure safe handling of PVD equipment and processes. This includes understanding the risks, emergency procedures, and proper use of personal protective equipment (PPE).
- Regular safety audits and equipment maintenance are necessary to identify and address potential risks before they become hazards.
In conclusion, while PVD is generally safer than CVD due to the absence of toxic chemicals, it is not without risks. Proper safety measures, including ventilation, equipment maintenance, and operator training, are essential to ensure a safe working environment. By adhering to these protocols, the risks associated with PVD can be effectively managed, making it a reliable and safe process for various industrial applications.
Summary Table:
Aspect | Key Information |
---|---|
Absence of Toxic Chemicals | No toxic chemicals used; safer than CVD. |
Gas Hazards | Argon, nitrogen gases require proper ventilation and monitoring. |
High-Energy Processes | Requires training for handling high-voltage equipment and radiation shielding. |
Advanced Technologies | Plasma-assisted PVD (PAPVD) needs specialized safety measures. |
Ventilation & Controls | Adequate ventilation and environmental controls are essential. |
Training & Protocols | Comprehensive training and regular safety audits are crucial. |
Ensure your PVD processes are safe and efficient—contact our experts today for guidance!