PVD (Physical Vapor Deposition) coating is a highly advantageous surface treatment method, particularly in industries requiring precision, durability, and environmental sustainability. It offers superior hardness, wear resistance, and adhesion while operating at lower temperatures, reducing the risk of thermal damage to substrates. PVD coatings are thinner, preserving the sharpness of cutting tools and reducing cutting forces. They are environmentally friendly, safer than chemical-based methods, and versatile, suitable for both functional and decorative applications. Additionally, PVD coatings are ideal for heat-sensitive materials and can replicate the appearance of costly metals, making them a preferred choice in industries like manufacturing, jewelry, and tooling.
Key Points Explained:
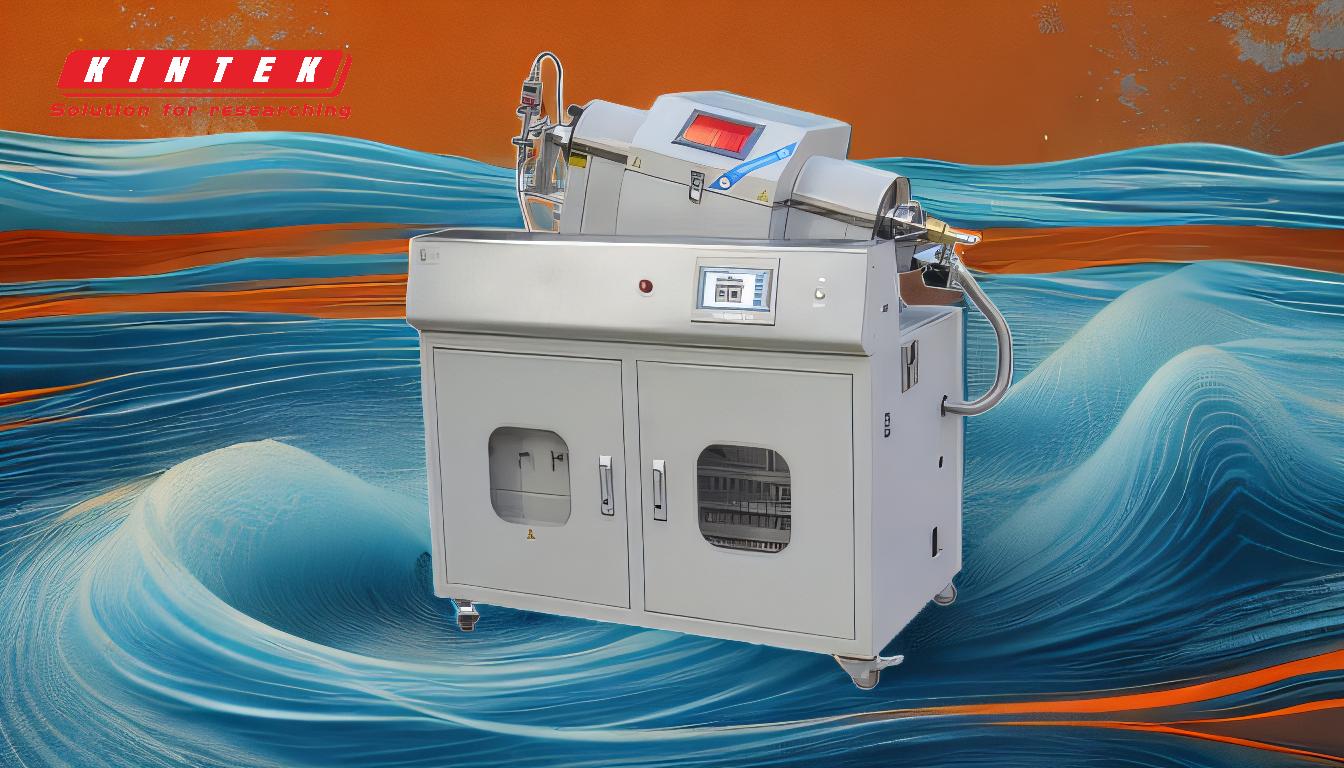
-
Enhanced Hardness and Wear Resistance
- PVD coatings significantly increase the hardness of the substrate material, making it more resistant to wear and abrasion. This is particularly beneficial for cutting tools, molds, and other components subjected to high stress.
- The thin coating (3~5μm) preserves the sharpness of blades and reduces cutting force and heat, enhancing tool life and performance.
-
Lower Process Temperatures
- PVD operates at temperatures around 500 °C, which minimizes the risk of thermal distortion or damage to the substrate. This makes it suitable for heat-sensitive materials and ensures dimensional stability in precision components.
-
Environmental and Safety Advantages
- Unlike chemical-based coating methods, PVD does not require extensive cleanups or the use of toxic substances. It is environmentally friendly and reduces the need for hazardous waste management.
- The process is safer for operators, as it avoids exposure to harmful chemicals and reduces workplace risks.
-
Versatility in Applications
- PVD coatings can be applied to almost any inorganic material, including metals, ceramics, and composites. This versatility makes it suitable for a wide range of industries, from manufacturing to jewelry.
- It can recreate the appearance of expensive metals like gold, brass, and bronze, offering decorative finishes without the high cost or maintenance requirements.
-
Improved Adhesion and Durability
- PVD coatings form a strong bond with the substrate, ensuring high adhesion and long-lasting performance. This is critical for applications requiring durability and reliability, such as cutting tools and molds.
- The compressive stress formed during cooling prevents crack formation and expansion, making PVD coatings ideal for interrupted cutting processes like milling.
-
Precision and Thin Film Deposition
- PVD allows for the accurate deposition of thin films with thicknesses ranging from 0.02 to 5 microns. This precision is essential for applications like optical coatings and fine blanking tools.
- The vacuum conditions of the process ensure thermal transport by radiation only, preventing conduction and convection, which enhances coating quality.
-
Cost and Production Efficiency
- PVD coating machines are computer-controlled, enabling operators to multitask and reduce production costs. They are suitable for both high-volume manufacturing and small batch production, offering flexibility and efficiency.
- The reduced need for post-processing and maintenance further lowers operational costs and turnaround time.
-
Decorative and Functional Finishes
- PVD coatings can provide both functional and decorative finishes. For example, they are used in jewelry for rose gold finishes and in watches for black or gunmetal colors.
- The original color of the coating can be maintained with simple cleaning, ensuring long-lasting aesthetic appeal.
In summary, PVD coating is a superior choice for many applications due to its combination of enhanced performance, environmental benefits, and versatility. Its ability to provide durable, precise, and aesthetically pleasing finishes makes it a preferred method across various industries.
Summary Table:
Advantages of PVD Coating | Key Benefits |
---|---|
Enhanced Hardness | Increases substrate hardness, ideal for cutting tools and high-stress components. |
Wear Resistance | Thin coatings (3~5μm) preserve sharpness, reduce cutting force, and enhance tool life. |
Lower Process Temperatures | Operates at ~500°C, minimizing thermal damage to heat-sensitive materials. |
Environmental Safety | No toxic substances, eco-friendly, and reduces workplace risks. |
Versatility | Suitable for metals, ceramics, and composites; decorative and functional uses. |
Improved Adhesion | Strong bond with substrates ensures durability and reliability. |
Precision Deposition | Thin films (0.02~5μm) for optical coatings and fine tools. |
Cost Efficiency | Computer-controlled machines reduce production costs and turnaround time. |
Ready to enhance your materials with PVD coatings? Contact us today to learn more!