PVD (Physical Vapor Deposition) coating and powder coating are two distinct surface treatment technologies, each with its own advantages and limitations. PVD coating is a high-tech process that applies extremely thin, durable, and environmentally friendly coatings in a vacuum chamber. It offers superior hardness, wear resistance, corrosion resistance, and thermal stability, making it ideal for high-performance applications. Powder coating, on the other hand, is a more cost-effective method that provides a wide range of colors and finishes but lacks the durability and precision of PVD coatings. While PVD is better suited for demanding industrial applications, powder coating is more commonly used for aesthetic and less demanding purposes.
Key Points Explained:
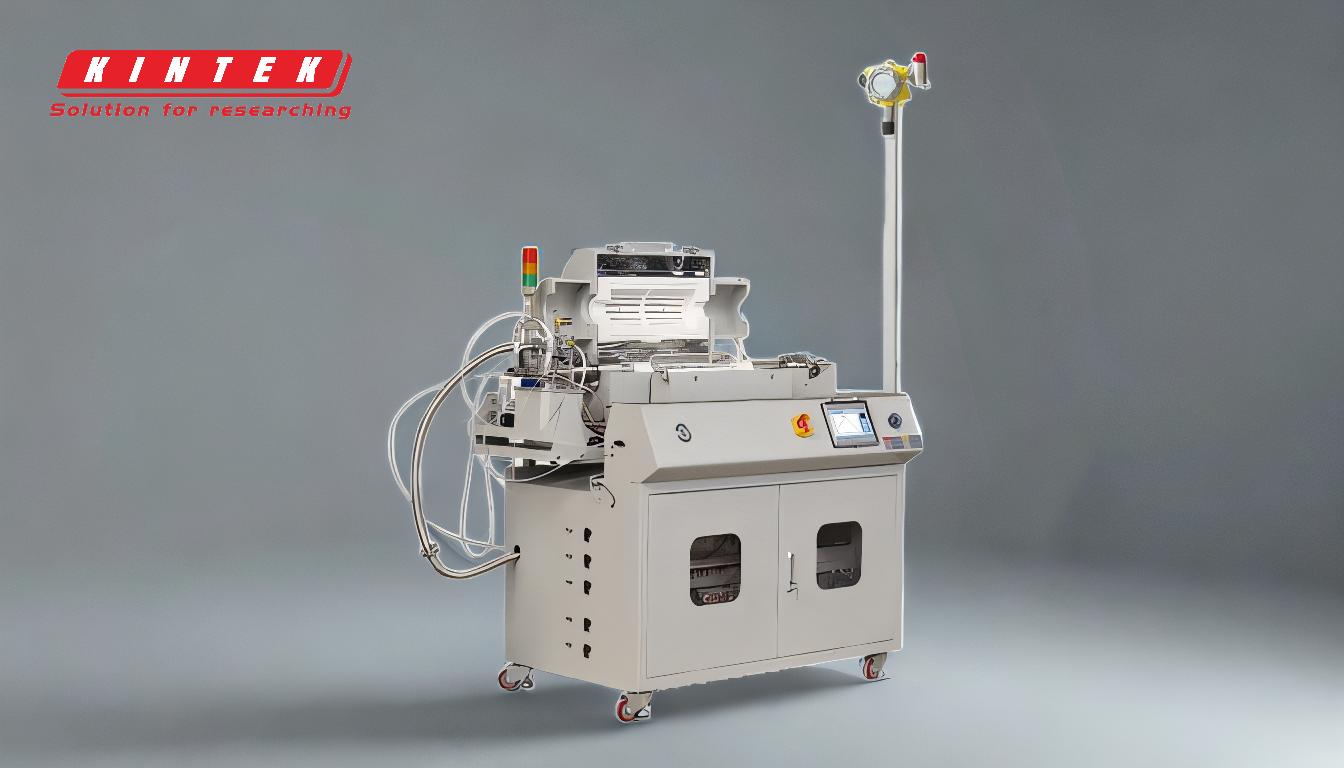
-
Coating Thickness and Durability:
- PVD coatings are extremely thin, ranging from 0.5 to 5 microns, but they are denser and more durable than powder coatings. This thin yet robust layer provides high hardness, wear resistance, and corrosion resistance, making PVD ideal for applications requiring long-lasting performance.
- Powder coatings are thicker and less dense, making them more suitable for decorative purposes or applications where extreme durability is not a priority.
-
Environmental Impact:
- PVD coating is more environmentally friendly as it produces no waste or harmful gases. The process occurs in a vacuum chamber, eliminating the need for toxic chemicals and reducing environmental contamination.
- Powder coating, while generally eco-friendly compared to liquid paints, still involves the use of polymers and may require more chemical management and disposal.
-
Application Process:
- PVD coating requires specialized equipment and a vacuum chamber. The process involves high temperatures (around 500 °C) and physical vapor deposition, which ensures a precise and uniform coating.
- Powder coating uses an electrostatic charge to apply organic polymers at lower temperatures. It is less complex and more cost-effective but lacks the precision and durability of PVD.
-
Material Compatibility:
- PVD can deposit a wide range of materials, including metals, alloys, and ceramics, making it versatile for various industrial applications.
- Powder coating is limited to organic polymers, restricting its use to less demanding applications.
-
Performance in High-Stress Environments:
- PVD coatings excel in high-stress environments due to their high hardness, wear resistance, and ability to withstand high temperatures. They also form compressive stress during cooling, preventing crack formation and expansion.
- Powder coatings are less suitable for high-stress applications, as they lack the mechanical strength and thermal stability of PVD coatings.
-
Aesthetic and Functional Flexibility:
- Powder coating offers a wider range of colors and finishes, making it ideal for decorative purposes.
- PVD coatings provide a superior finish at the molecular level and can enhance the appearance of products by changing their color or finish, though the options are more limited compared to powder coating.
-
Cost and Accessibility:
- Powder coating is generally more affordable and accessible, making it a popular choice for large-scale or less demanding projects.
- PVD coating is more expensive due to the specialized equipment and processes involved, but it offers long-term value for high-performance applications.
In summary, PVD coating is better than powder coating for applications requiring high durability, precision, and environmental sustainability. However, powder coating remains a cost-effective and versatile option for less demanding or decorative purposes. The choice between the two depends on the specific requirements of the application.
Summary Table:
Feature | PVD Coating | Powder Coating |
---|---|---|
Coating Thickness | 0.5 to 5 microns (thin and dense) | Thicker and less dense |
Durability | High hardness, wear, and corrosion resistance | Less durable, suitable for decorative purposes |
Environmental Impact | Eco-friendly, no waste or harmful gases | Generally eco-friendly but involves polymers |
Application Process | Requires vacuum chamber and high temperatures (500 °C) | Uses electrostatic charge at lower temperatures |
Material Compatibility | Metals, alloys, ceramics | Limited to organic polymers |
High-Stress Performance | Excellent due to hardness and thermal stability | Less suitable for high-stress environments |
Aesthetic Flexibility | Limited color options, superior molecular finish | Wide range of colors and finishes |
Cost | Expensive but offers long-term value | Affordable and accessible |
Need help choosing the right coating for your project? Contact our experts today for personalized advice!