PVD (Physical Vapor Deposition) coatings are highly regarded for their corrosion resistance, among other properties. These coatings are thin, typically ranging from 0.5 to 5 microns, and are known for their high hardness, wear resistance, and low friction. They are chemically inert compared to their pure metallic forms, making them resistant to environmental conditions like corrosion and oxidation. This resistance extends the lifespan of products and tools, making PVD coatings suitable for industries such as automotive, aerospace, and medical. The coatings also offer high purity, uniformity, and excellent adhesion to substrates, often outperforming traditional electroplating in terms of hardness and corrosion resistance.
Key Points Explained:
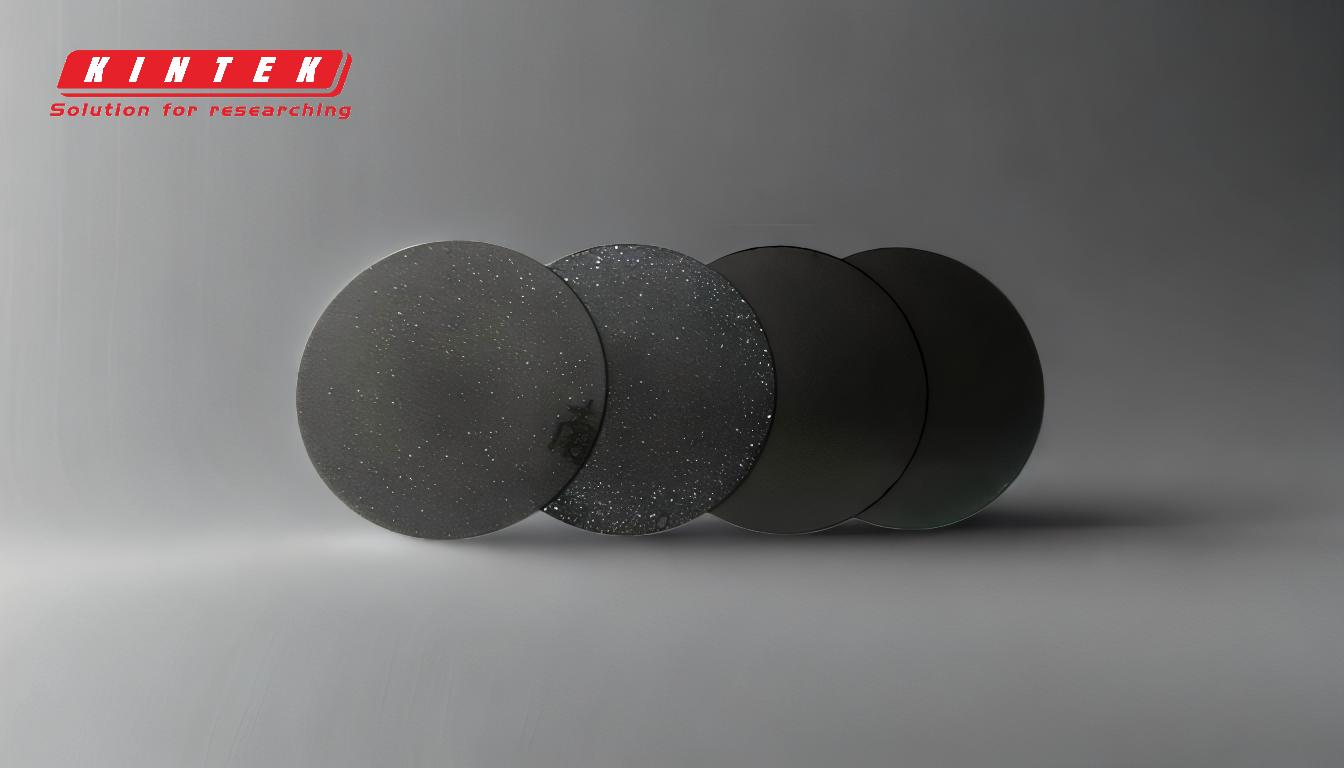
-
Corrosion Resistance of PVD Coatings:
- PVD coatings are highly resistant to corrosion and oxidation. This is due to their chemical inertness, which makes them less reactive to environmental factors that typically cause corrosion.
- The thin nature of these coatings, ranging from 0.5 to 5 microns, contributes to their durability and resistance to wear and tear, further enhancing their corrosion resistance.
-
Chemical Inertness:
- PVD coatings are more chemically inert than their pure metallic forms. This means they do not easily react with substances that typically cause corrosion, such as oxygen and moisture.
- This property ensures that PVD-coated products maintain a tarnish-free appearance and enhanced durability over time.
-
Applications in Various Industries:
- The corrosion resistance of PVD coatings makes them ideal for use in industries where exposure to harsh environments is common. For example, in the automotive and aerospace industries, components are often exposed to extreme conditions that can lead to corrosion.
- In the medical industry, PVD coatings are used on surgical instruments and implants, where corrosion resistance is crucial for maintaining hygiene and functionality.
-
Comparison with Electroplating:
- PVD coatings are often harder and more corrosion-resistant than coatings applied by electroplating. This is due to the high purity and uniformity of PVD coatings, which provide better adhesion to the substrate and superior protection against corrosion.
- The durability of PVD coatings often eliminates the need for additional protective topcoats, making them a cost-effective solution in the long run.
-
Enhanced Aesthetic and Functional Properties:
- Besides corrosion resistance, PVD coatings offer improved wear resistance, reduced friction, and increased hardness. These properties make them valuable in applications where both aesthetic appearance and functional performance are important.
- The coatings can replicate the original finish of materials with minimal effort, providing a high-quality metallic luster without the need for polishing.
-
Limitations and Considerations:
- While PVD coatings are highly effective, they do have some limitations. For instance, they may have poor coating performance on the back and sides of tools due to low air pressure during the coating process.
- The properties of PVD coatings are also influenced by the underlying substrate material. For example, a TiN coating on Ti-6Al-4V alloy can significantly increase the fatigue limit and endurance of the material.
In summary, PVD coatings are highly corrosion-resistant due to their chemical inertness, thinness, and high purity. These properties make them suitable for a wide range of applications across various industries, offering both functional and aesthetic benefits. While there are some limitations, the overall advantages of PVD coatings make them a preferred choice for enhancing the durability and performance of products and tools.
Summary Table:
Property | Description |
---|---|
Corrosion Resistance | Highly resistant to corrosion and oxidation due to chemical inertness. |
Thickness | Thin coatings (0.5–5 microns) enhance durability and wear resistance. |
Chemical Inertness | Less reactive to environmental factors like oxygen and moisture. |
Applications | Ideal for automotive, aerospace, and medical industries. |
Comparison to Electroplating | Harder and more corrosion-resistant than electroplating. |
Limitations | Poor coating performance on tool backs/sides; substrate material influences results. |
Learn how PVD coatings can improve your product's durability—contact our experts today!