Pyrolysis can be a good investment depending on the specific goals, operational needs, and budget of the project. The choice of pyrolysis reactor plays a critical role in determining the efficiency, cost-effectiveness, and suitability of the process. Different types of reactors, such as circulating, continuous, intermittent, and auger pyrolysis reactors, offer unique advantages and limitations. For instance, circulating reactors eliminate the need for catalysts and inert atmospheres, while continuous reactors prioritize efficiency and automation. On the other hand, intermittent reactors are more cost-effective, and auger reactors are ideal for processing heterogeneous materials but are less suitable for producing bio-oils. Understanding the specific requirements of the plant, the size of the reactor, and the type of material to be processed is essential for making an informed decision.
Key Points Explained:
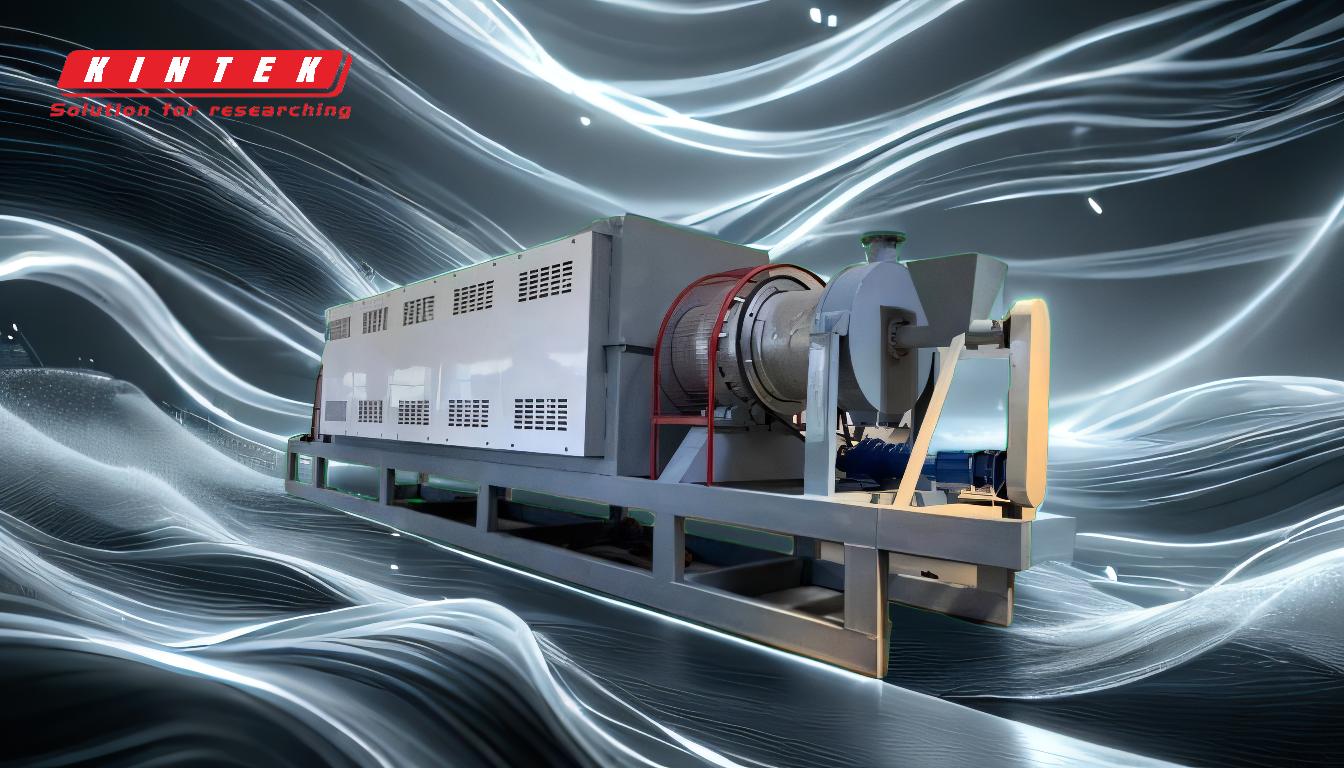
-
Types of Pyrolysis Reactors and Their Suitability
- Circulating Pyrolysis Reactor: This type of reactor is highly efficient as it relies solely on external heat supply, eliminating the need for catalysts, inert atmospheres, and additional requirements. This makes it a simpler and potentially more cost-effective option for certain applications.
- Continuous Pyrolysis Reactor: Ideal for projects prioritizing high efficiency and automation. These reactors are suitable for large-scale operations but may involve higher initial investment costs.
- Intermittent Pyrolysis Reactor: A more budget-friendly option, suitable for smaller-scale operations or projects with limited capital. However, they may not offer the same level of efficiency as continuous reactors.
- Auger Pyrolysis Reactor: Best suited for processing heterogeneous or difficult materials, such as agricultural waste. While it excels in producing biochar, it is less effective for generating bio-oils and volatiles.
-
Factors Influencing the Investment Decision
- Operational Needs: The choice of reactor should align with the specific goals of the project. For example, if the primary objective is to produce bio-oils, a circulating or continuous reactor may be more suitable than an auger reactor.
- Budget Considerations: The initial investment and operational costs vary significantly between reactor types. Intermittent reactors are more affordable, while continuous reactors may require a larger upfront investment but offer long-term efficiency benefits.
- Material Type: The nature of the feedstock is a critical factor. For instance, an auger reactor is ideal for heterogeneous materials, while a circulating reactor may be better suited for more uniform feedstocks.
-
Benefits of Pyrolysis as an Investment
- Waste Management: Pyrolysis is an effective method for converting waste materials, such as plastics, biomass, and tires, into valuable products like biochar, bio-oil, and syngas. This can help reduce waste disposal costs and generate additional revenue streams.
- Sustainability: Pyrolysis contributes to a circular economy by recycling waste materials and reducing reliance on fossil fuels.
- Scalability: Depending on the reactor type, pyrolysis can be scaled to meet the needs of small, medium, or large operations.
-
Challenges and Considerations
- Initial Investment: High-efficiency reactors, such as continuous systems, may require significant upfront capital.
- Operational Complexity: Some reactors, like continuous systems, may require more sophisticated infrastructure and skilled personnel.
- Feedstock Availability: The success of a pyrolysis project depends on a consistent supply of suitable feedstock.
-
Key Considerations When Purchasing a Pyrolysis Reactor
- Plant Requirements: Assess the specific needs of the plant, including space, energy supply, and operational capabilities.
- Reactor Size: Choose a reactor size that matches the scale of the operation and the volume of feedstock to be processed.
- Material Compatibility: Ensure the reactor is compatible with the type of material it will process, whether it’s biomass, plastics, or other waste materials.
In conclusion, pyrolysis can be a profitable and sustainable investment if the right reactor is selected based on the project's specific needs, budget, and operational goals. For more detailed information on selecting the appropriate reactor, refer to the pyrolysis reactor guide.
Summary Table:
Reactor Type | Advantages | Limitations |
---|---|---|
Circulating | No catalysts or inert atmospheres needed; cost-effective for certain uses. | May require higher initial investment. |
Continuous | High efficiency and automation; ideal for large-scale operations. | Higher upfront costs and operational complexity. |
Intermittent | Budget-friendly; suitable for small-scale projects. | Lower efficiency compared to continuous reactors. |
Auger | Ideal for heterogeneous materials like agricultural waste; great for biochar. | Less effective for producing bio-oils and volatiles. |
Ready to explore pyrolysis for your project? Contact our experts today to find the perfect solution!