The temperature during thin film deposition has generally been decreasing.
This trend is particularly evident with the shift from high-temperature furnace processes to plasma-enhanced chemical vapor deposition (PECVD) processes.
PECVD processes operate at lower temperatures, typically between 250 to 350°C.
This reduction in temperature is driven by the need to reduce the thermal budget while maintaining the performance of the films.
5 Key Insights
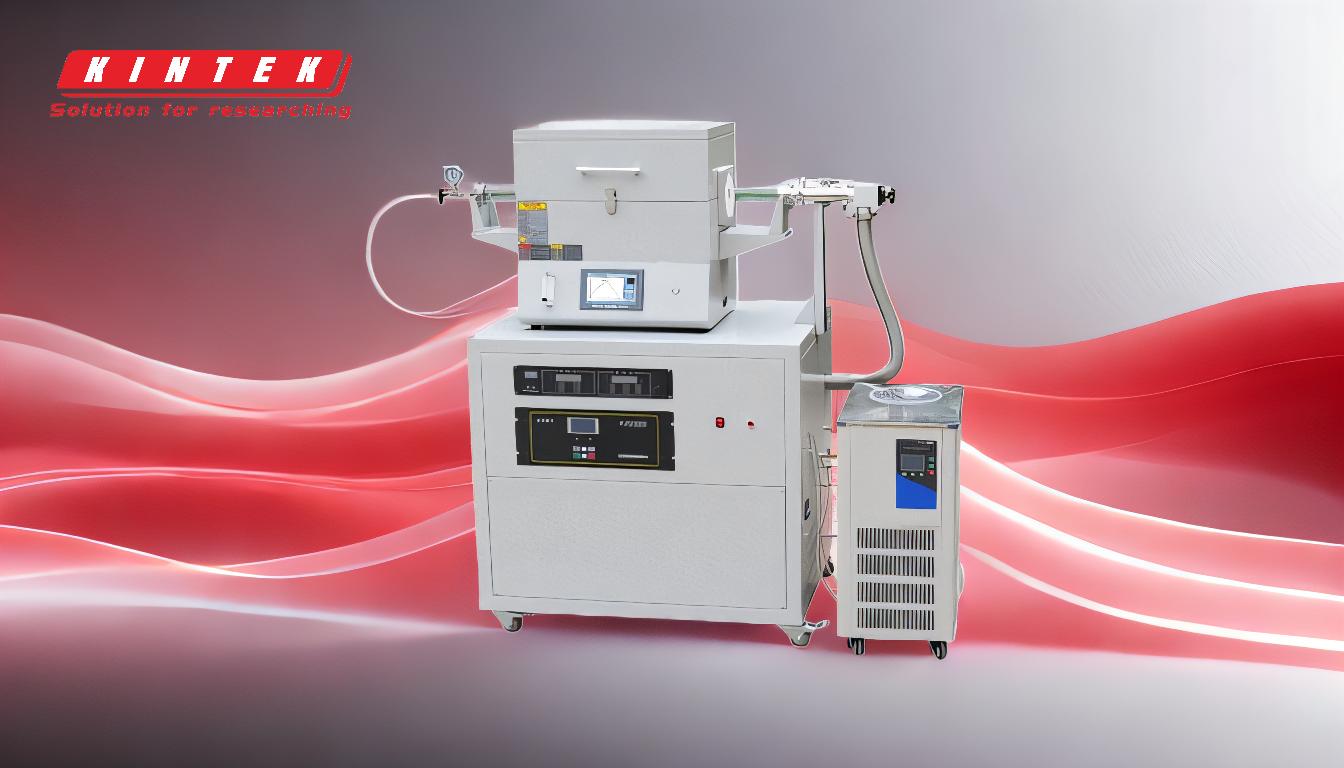
1. Lowering of Deposition Temperatures
Historically, thin film deposition was conducted at very high temperatures, often exceeding 1000°C, using furnaces.
However, advancements in technology and materials have led to the development of PECVD.
PECVD operates at significantly lower temperatures, which is crucial for the integration of new materials that may not withstand the high temperatures of traditional deposition methods.
The lower temperatures in PECVD processes are achieved through the use of plasma, which can activate chemical reactions at lower temperatures than thermal methods.
2. Impact of Substrate Temperature
The temperature of the substrate during deposition plays a critical role in the quality and properties of the thin film.
Lower substrate temperatures can lead to slower film growth and increased surface roughness.
Conversely, higher substrate temperatures can enhance the growth rate and reduce surface roughness.
However, the optimal substrate temperature depends on the specific materials and the desired film properties.
In some cases, additional cooling steps may be necessary to carefully control the heat on the substrate, especially for sensitive materials or specific product requirements.
3. Control of Deposition Rate and Process Temperature
The deposition rate and process temperature are closely linked and must be carefully controlled to ensure the desired film characteristics.
The deposition rate affects the uniformity and thickness consistency of the film.
Process temperature significantly impacts film characteristics and is often dictated by the application’s requirements.
For instance, certain applications may require lower temperatures to prevent damage to the underlying material or to achieve specific film properties.
4. Potential for Damage at Lower Temperatures
While lower temperatures reduce the thermal stress on the materials, they can introduce other forms of damage.
These include issues like pollution, UV radiation, and ion bombardment, which can be more pronounced in smaller features.
Understanding and mitigating these risks is crucial for maintaining the integrity and performance of the deposited films.
5. Summary of Temperature Trends in Deposition
The trend in thin film deposition is towards lower temperatures, primarily to reduce thermal stress on materials and substrates.
This trend also aims to accommodate a wider range of materials and applications.
However, achieving the right balance between temperature, deposition rate, and other process parameters is essential for producing high-quality thin films.
Continue exploring, consult our experts
Discover the cutting-edge advancements in thin film deposition technology with KINTEK SOLUTION.
Our innovative plasma-enhanced chemical vapor deposition (PECVD) systems operate at lower temperatures, ensuring material integrity and film performance without compromising on quality.
Embrace the future of high-quality thin films with temperature-controlled precision.
Elevate your deposition processes today—explore our solutions and redefine your thin film technology with KINTEK SOLUTION.