Tyre pyrolysis oil and plastic pyrolysis oil are not the same, although they are both derived from pyrolysis processes. While they share some similarities, such as being products of thermal decomposition in the absence of oxygen, their chemical compositions, properties, and potential applications differ significantly due to the distinct raw materials used. Tyre pyrolysis oil is derived from scrap tyres, which contain rubber, carbon black, and other additives, while plastic pyrolysis oil comes from various types of plastic waste, such as polyethylene, polypropylene, and polystyrene. These differences result in variations in their physical and chemical properties, such as heating value, viscosity, and composition, which ultimately influence their suitability for specific applications.
Key Points Explained:
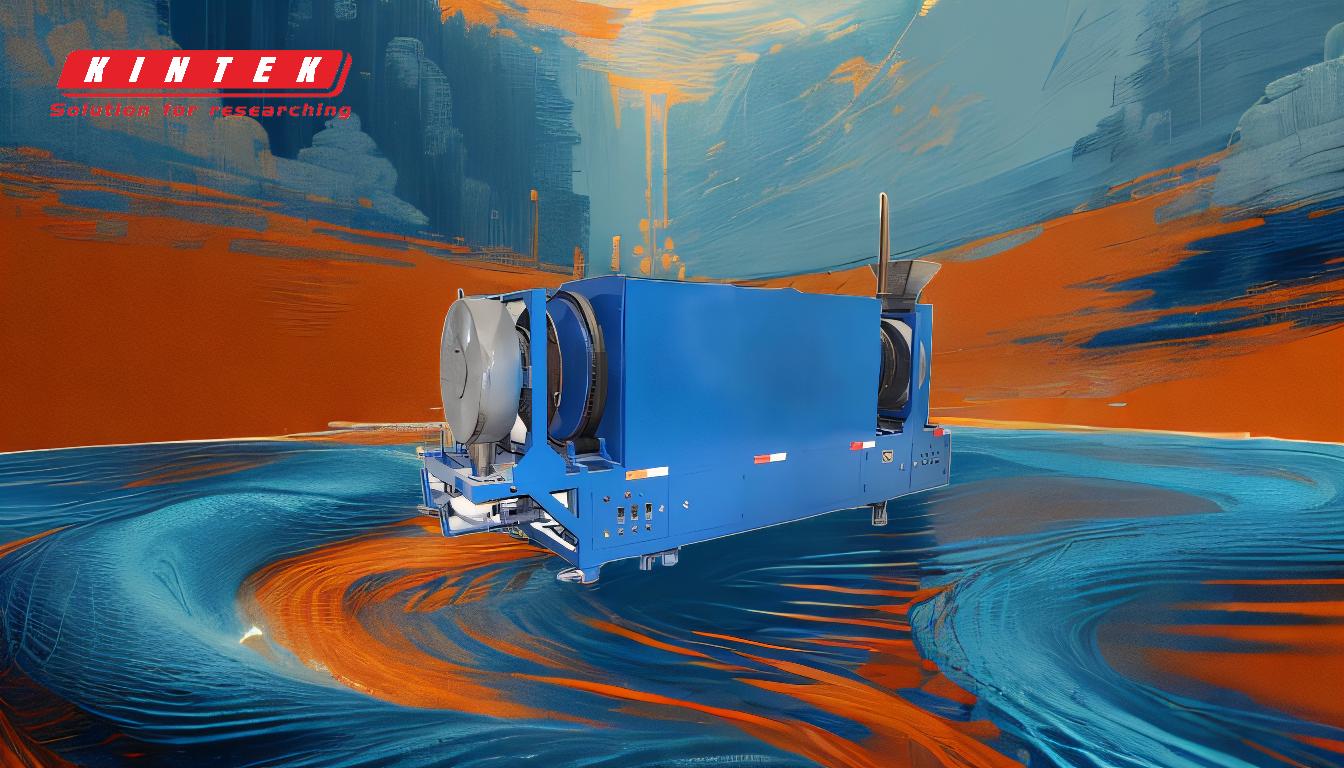
-
Raw Materials and Composition:
- Tyre Pyrolysis Oil: Derived from scrap tyres, which are composed of natural and synthetic rubber, carbon black, steel, and other additives. The pyrolysis process breaks down these materials into oil, gas, and char. The oil contains hydrocarbons, aromatic compounds, and other organic substances.
- Plastic Pyrolysis Oil: Derived from plastic waste, which consists of polymers like polyethylene (PE), polypropylene (PP), and polystyrene (PS). The pyrolysis process decomposes these polymers into smaller hydrocarbon chains, resulting in oil with a different chemical profile compared to tyre pyrolysis oil.
-
Chemical Properties:
- Tyre Pyrolysis Oil: Typically contains a higher concentration of aromatic hydrocarbons and sulfur compounds due to the presence of rubber and additives in tyres. This makes it more acidic and less stable compared to plastic pyrolysis oil.
- Plastic Pyrolysis Oil: Generally contains a higher proportion of aliphatic hydrocarbons, which are more stable and less acidic. The absence of sulfur compounds in most plastics results in a cleaner oil with fewer impurities.
-
Physical Properties:
- Tyre Pyrolysis Oil: Has a higher density and viscosity compared to plastic pyrolysis oil. It may also contain more solid residues, such as carbon char, due to the incomplete breakdown of tyre components.
- Plastic Pyrolysis Oil: Typically has lower density and viscosity, making it easier to handle and process. It is also less likely to contain solid residues, as plastics tend to decompose more completely during pyrolysis.
-
Heating Value:
- Tyre Pyrolysis Oil: Generally has a lower heating value compared to plastic pyrolysis oil due to its higher water content and the presence of impurities. This makes it less efficient as a fuel.
- Plastic Pyrolysis Oil: Has a higher heating value, making it more suitable for use as a fuel or for further refining into higher-value products.
-
Applications:
- Tyre Pyrolysis Oil: Often used as a fuel in industrial burners or as a feedstock for further refining. However, its high sulfur content and instability limit its applications in more sensitive processes.
- Plastic Pyrolysis Oil: Can be used as a fuel or refined into diesel, gasoline, or other petrochemical products. Its cleaner composition makes it more versatile and suitable for a wider range of applications.
-
Environmental Impact:
- Tyre Pyrolysis Oil: The presence of sulfur and other impurities can lead to higher emissions of pollutants when burned, making it less environmentally friendly.
- Plastic Pyrolysis Oil: Generally has a lower environmental impact due to its cleaner composition, although it still requires proper handling to minimize emissions and ensure safe disposal of by-products.
In summary, while both tyre pyrolysis oil and plastic pyrolysis oil are products of pyrolysis, they differ significantly in terms of their raw materials, chemical and physical properties, heating values, applications, and environmental impacts. These differences make them distinct products with unique challenges and opportunities in the market.
Summary Table:
Aspect | Tyre Pyrolysis Oil | Plastic Pyrolysis Oil |
---|---|---|
Raw Materials | Scrap tyres (rubber, carbon black, additives) | Plastic waste (polyethylene, polypropylene, polystyrene) |
Chemical Properties | High aromatic hydrocarbons, sulfur compounds, acidic, less stable | High aliphatic hydrocarbons, fewer impurities, more stable |
Physical Properties | Higher density, viscosity, and solid residues | Lower density, viscosity, and fewer residues |
Heating Value | Lower heating value due to impurities and water content | Higher heating value, suitable for fuel and refining |
Applications | Industrial burners, feedstock for refining (limited by sulfur content) | Fuel, refined into diesel, gasoline, and petrochemical products |
Environmental Impact | Higher emissions due to sulfur and impurities | Cleaner composition, lower emissions, but requires proper handling |
Want to learn more about pyrolysis oils and their applications? Contact our experts today for tailored advice!