Tungsten heating elements are specialized components used in high-temperature applications due to tungsten's exceptional thermal and mechanical properties. These elements are capable of operating at extremely high temperatures, with a maximum temperature of 2400°C and long-term use at 2300°C. However, they are susceptible to embrittlement, mechanical and thermal shock, and oxidation when exposed to air above 500°C. To mitigate these risks, a ramping temperature control system is essential during cold start-up. Tungsten's high melting point, density, and thermal stability make it ideal for applications requiring precise temperature control and durability in harsh environments.
Key Points Explained:
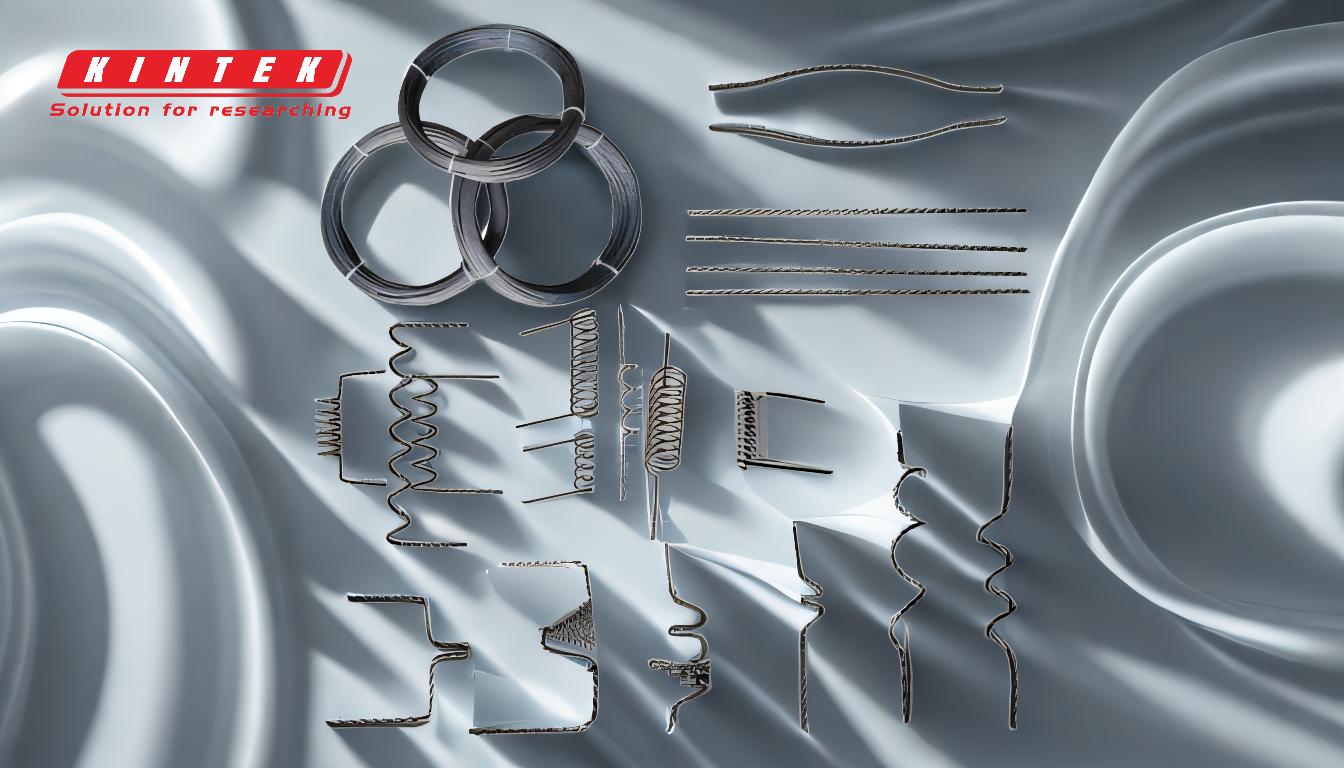
-
High-Temperature Capabilities:
- Tungsten heating elements can withstand extremely high temperatures, with a maximum operational temperature of 2400°C and a long-term use temperature of 2300°C. This makes them suitable for applications in industries such as semiconductor manufacturing, aerospace, and high-temperature furnaces.
- The heating process involves the transfer of kinetic energy from electrons to tungsten atoms, generating heat that warms the surrounding chamber. This mechanism allows for fast heating and precise temperature control.
-
Material Properties:
- Tungsten has a melting point of 3420°C and a boiling point of 5660°C, making it one of the most heat-resistant metals available.
- It has a density of 19.3 g/cm³, an atomic radius of 139 pm, and an electronegativity of 1.7. These properties contribute to its high-temperature strength and thermal stability.
- Tungsten is a silvery-white, shiny metal that is insoluble in water and exhibits excellent corrosion resistance to molten alkali metals and steam.
-
Challenges and Precautions:
- Tungsten heating elements are prone to embrittlement, mechanical and thermal shock, and oxidation when exposed to air at temperatures above 500°C (932°F).
- To prevent embrittlement during cold start-up, a ramping temperature control system is necessary. This system gradually increases the temperature, reducing the risk of thermal shock and extending the service life of the heating element.
-
Applications and Benefits:
- Tungsten heating elements are used in environments that require precise temperature control and durability, such as vacuum furnaces, high-temperature sintering, and crystal growth processes.
- The long service life and fast heating capabilities of tungsten mesh heating elements make them cost-effective solutions for high-temperature applications.
By understanding these key points, purchasers of equipment and consumables can make informed decisions about the suitability of tungsten heating elements for their specific needs, ensuring optimal performance and longevity in demanding environments.
Summary Table:
Key Aspect | Details |
---|---|
Max Temperature | 2400°C (operational), 2300°C (long-term use) |
Material Properties | Melting point: 3420°C, Density: 19.3 g/cm³, Corrosion-resistant |
Challenges | Embrittlement, oxidation above 500°C, thermal shock |
Precautions | Ramping temperature control system for cold start-up |
Applications | Vacuum furnaces, high-temperature sintering, crystal growth |
Benefits | Precise temperature control, durability, fast heating, cost-effective |
Ready to enhance your high-temperature processes? Contact us today to learn more about tungsten heating elements!