Silicon Carbide (SiC) components are advanced materials made from silicon carbide, a compound semiconductor composed of silicon and carbon. These components are highly valued for their exceptional mechanical, thermal, chemical, and physical properties, making them suitable for a wide range of applications in both traditional industries and high-tech fields. SiC components are known for their low density, high strength, excellent thermal conductivity, high hardness, and superior chemical inertness. They are used in demanding environments such as semiconductors, nuclear energy, national defense, and space technology, as well as in industrial applications like resistance heating elements, thermistors, varistors, and abrasive products. Their ability to maintain high mechanical strength at extreme temperatures and resist chemical corrosion makes them indispensable in modern engineering and technology.
Key Points Explained:
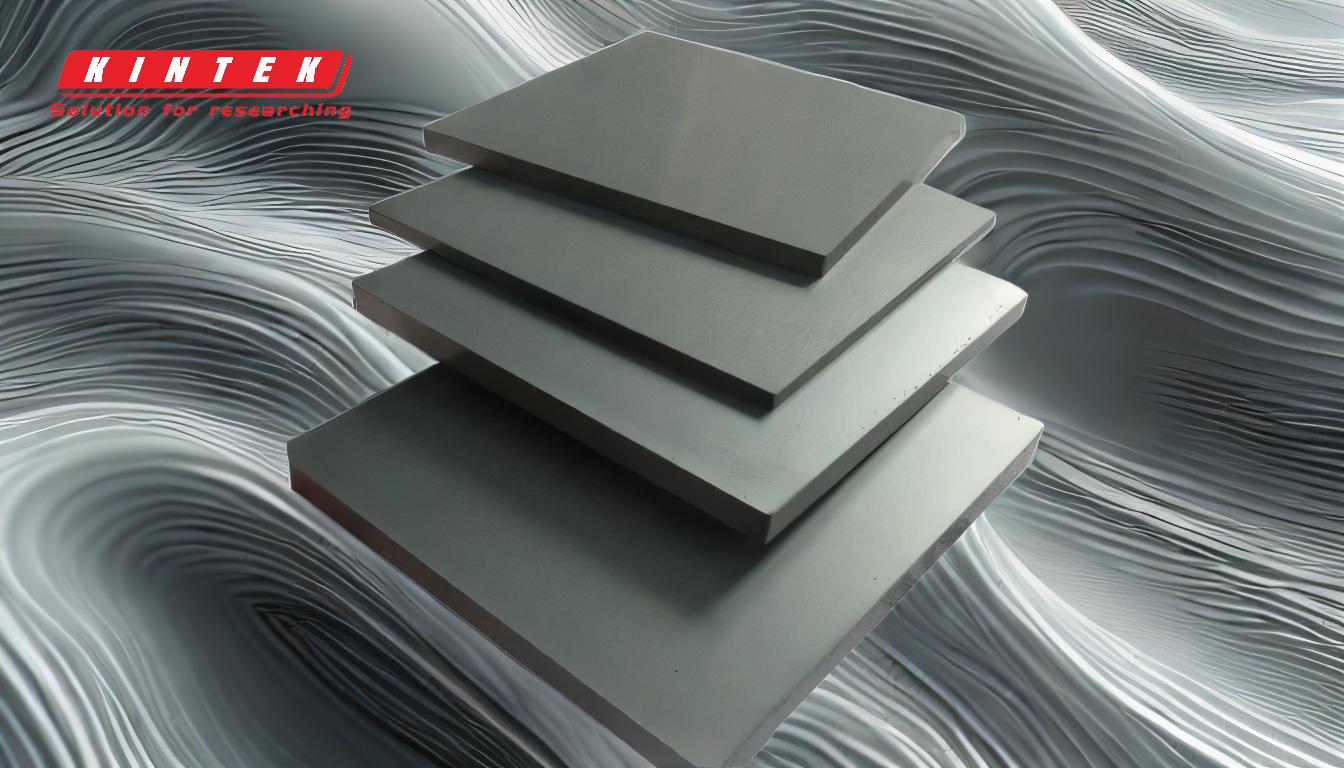
-
Composition and Properties of SiC:
- Composition: Silicon Carbide (SiC) is a compound made from silicon and carbon, forming a ceramic material with semiconductor properties.
-
Key Properties:
- Mechanical: High strength, high hardness, and high elastic modulus.
- Thermal: Low thermal expansion, high thermal conductivity, and excellent thermal shock resistance.
- Chemical: Superior chemical inertness and resistance to corrosion.
- Physical: Low density and high melting point.
-
Manufacturing Process:
- SiC components are typically produced by pressing or extruding silicon carbide powder and then sintering it at high temperatures. This process results in a dense, durable material with high electrical conductivity compared to other ceramics.
-
Applications of SiC Components:
-
Industrial Applications:
- Abrasives: SiC has been used for over a century in abrasive products like grinding wheels due to its high hardness and wear resistance.
- Heating Elements: SiC is used in resistance heating elements for electric furnaces, as well as in thermistors and varistors.
-
High-Tech Applications:
- Semiconductors: SiC is increasingly used in semiconductor process equipment due to its excellent thermal and electrical properties.
- Energy and Defense: SiC components are used in nuclear energy, national defense, and space technology for their ability to withstand extreme conditions.
- Mechanical Components: SiC is used in fixed and moving turbine components, seals, bearings, ball valve parts, hot gas flow liners, and heat exchangers.
-
Industrial Applications:
-
Advantages of SiC Components:
- High-Temperature Performance: SiC maintains high mechanical strength at temperatures up to 1,400°C, making it ideal for high-temperature applications.
- Chemical Resistance: SiC has higher chemical corrosion resistance than other ceramics, making it suitable for harsh chemical environments.
- Thermal Shock Resistance: SiC's ability to withstand rapid temperature changes without cracking or degrading is crucial in applications like heat exchangers and turbine components.
- Wear Resistance: The high hardness and wear resistance of SiC make it ideal for abrasive and mechanical applications.
-
Future Prospects:
- The versatility and superior performance characteristics of SiC components are driving their increasing adoption in various high-tech fields. As technology advances, the demand for SiC components is expected to grow, particularly in applications requiring high performance under extreme conditions.
In summary, SiC components are critical materials in modern engineering and technology, offering a unique combination of mechanical, thermal, and chemical properties that make them suitable for a wide range of demanding applications. Their ability to perform under extreme conditions and resist wear and corrosion ensures their continued importance in both traditional industries and emerging high-tech fields.
Summary Table:
Key Aspect | Details |
---|---|
Composition | Silicon and carbon compound, forming a ceramic semiconductor material. |
Key Properties | High strength, thermal conductivity, chemical inertness, and wear resistance. |
Manufacturing Process | Pressing or extruding SiC powder, followed by high-temperature sintering. |
Applications | Semiconductors, nuclear energy, defense, space tech, heating elements, abrasives. |
Advantages | High-temperature performance, chemical resistance, thermal shock resistance, wear resistance. |
Future Prospects | Increasing adoption in high-tech fields due to superior performance under extreme conditions. |
Learn how Silicon Carbide (SiC) components can enhance your applications—contact us today!