Physical Vapor Deposition (PVD) coatings are a versatile and advanced technology used across numerous industries to enhance the performance, durability, and functionality of materials. These coatings are applied through processes like sputtering and thermal methods, which include vacuum evaporation, pulsed laser deposition, and ion plating. PVD coatings are known for their ability to improve electrical conductivity, optical performance, and oxidation resistance. They are widely used in industries such as aerospace, automotive, medical, and electronics, where they provide benefits like high hardness, corrosion resistance, and the ability to deposit both organic and inorganic materials.
Key Points Explained:
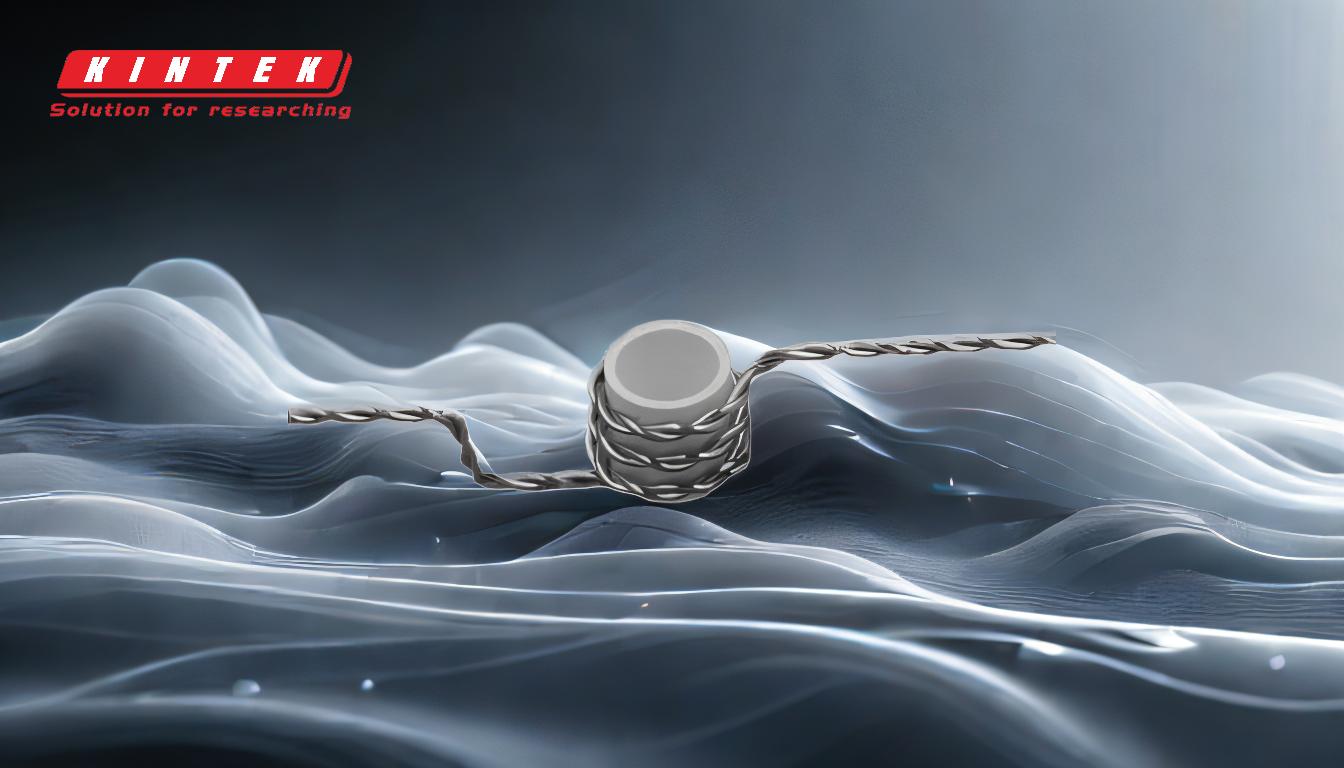
-
Types of PVD Coatings
- Titanium Coatings: Commonly used in the medical field for surgical tools and implants due to their biocompatibility and corrosion resistance.
- Gold Thin Films: Replacing traditional plating methods in electronics to enhance conductivity and reduce oxidation.
- Ceramic Coatings: Applied to industrial tools to increase hardness and wear resistance, making them ideal for high-stress environments.
- Non-Metal Oxides: Used in semiconductor manufacturing for their chemical resistance and ability to withstand harsh processing conditions.
-
Industries and Applications
- Aerospace: PVD coatings are used on composites and components to improve oxidation resistance and durability in extreme conditions.
- Automotive: Applied to engine parts and other components to enhance wear resistance and reduce friction.
- Medical: Used on surgical instruments and implants to ensure biocompatibility and prevent corrosion.
- Electronics: Gold thin films and other conductive coatings are used in circuits and connectors to improve performance.
- Optics: PVD coatings are applied to mirrors and lenses to enhance reflectivity and optical clarity.
-
Benefits of PVD Coatings
- High Hardness: Provides excellent wear resistance, making them suitable for industrial tools and machinery.
- Corrosion Resistance: Protects materials from environmental degradation, extending their lifespan.
- Flexibility: Can be applied to a wide range of materials, including metals, ceramics, and polymers.
- Enhanced Performance: Improves electrical conductivity, optical properties, and thermal stability.
-
PVD Processes
- Sputtering: A method where atoms are ejected from a solid target material due to bombardment by energetic ions, forming a thin film on the substrate.
- Thermal Processes: Include vacuum evaporation, pulsed laser deposition, and ion plating, each offering unique advantages for specific applications.
-
Future Trends
- The demand for PVD coatings is expected to grow in industries like renewable energy, where they can be used to improve the efficiency of solar panels and wind turbines.
- Advances in nanotechnology are likely to lead to the development of even thinner and more efficient coatings.
PVD coatings are a critical technology in modern manufacturing, offering solutions to some of the most challenging material performance issues across a wide range of industries. Their versatility, durability, and ability to enhance material properties make them indispensable in high-tech applications.
Summary Table:
Coating Type | Applications | Key Benefits |
---|---|---|
Titanium Coatings | Medical tools, implants | Biocompatibility, corrosion resistance |
Gold Thin Films | Electronics (circuits, connectors) | Enhanced conductivity, reduced oxidation |
Ceramic Coatings | Industrial tools, high-stress environments | High hardness, wear resistance |
Non-Metal Oxides | Semiconductor manufacturing | Chemical resistance, durability in harsh conditions |
Learn how PVD coatings can transform your materials—contact our experts today for tailored solutions!