Low-Pressure Chemical Vapor Deposition (LPCVD) is a widely used technique in semiconductor manufacturing and thin-film deposition due to its ability to produce high-quality, uniform films with excellent conformal step coverage. LPCVD operates at reduced pressures, which enhances the mass transfer rate of gaseous reactants and by-products, leading to faster reaction rates and improved film properties. However, it also has some limitations, such as requiring higher temperatures, which can restrict the types of materials that can be processed. This method is highly versatile, cost-effective, and suitable for a variety of applications, including MEMS devices and semiconductor products.
Key Points Explained:
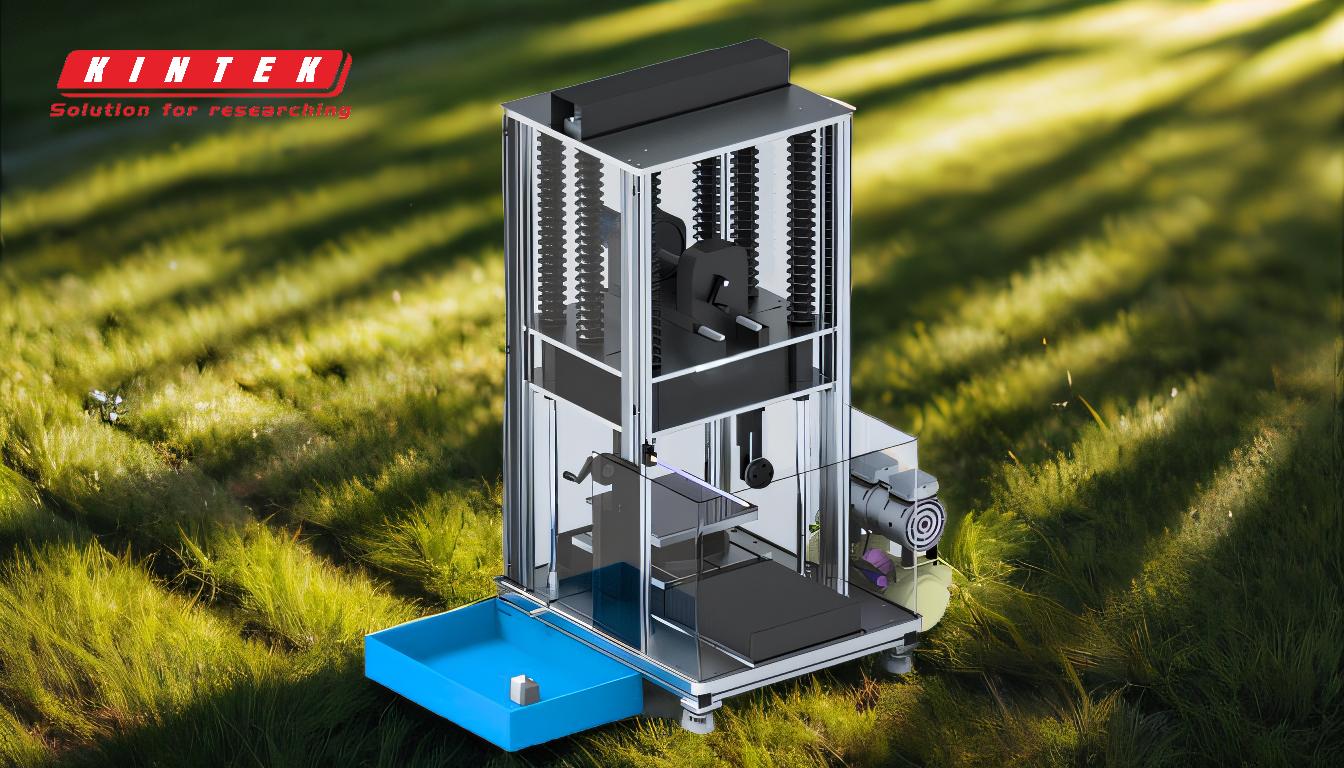
-
Advantages of LPCVD:
- Film Uniformity and Quality: LPCVD produces films with high uniformity, fewer defects, and excellent conformal step coverage. This makes it ideal for applications requiring precise thin-film deposition, such as in MEMS devices and semiconductor manufacturing.
- Versatility: LPCVD can be used to deposit a wide range of materials, including silicon dioxide, silicon nitride, polycrystalline silicon, and even advanced materials like graphene and carbon nanotubes.
- Cost-Effectiveness: The process is relatively cost-effective compared to other deposition methods, making it a popular choice in the industry.
- Low-Temperature Processing: While LPCVD generally requires higher temperatures than some other methods, it still offers low-temperature processing options, which can be beneficial for certain materials and applications.
- High Deposition Rates: The reduced operating pressure in LPCVD increases the free path of molecules and the gas diffusion coefficient, leading to faster reaction rates and higher deposition rates.
-
Disadvantages of LPCVD:
- High Temperature Requirements: LPCVD typically requires higher temperatures than other chemical vapor deposition methods, which can limit the types of materials that can be processed. This can be a drawback for temperature-sensitive materials.
- Complexity and Skill Requirements: The process can be complex and may require skilled operators, especially when dealing with high vacuums and temperatures. This can increase the overall cost and complexity of the process.
- Material Limitations: The high temperatures required for LPCVD can restrict the types of materials that can be used, potentially limiting its applicability in certain scenarios.
-
Comparison with Other Deposition Methods:
- PVD vs. LPCVD: Physical Vapor Deposition (PVD) is a line-of-sight technique, making it difficult to coat undercuts and similar surface features. In contrast, LPCVD offers better conformal coverage and is more versatile in terms of the materials it can deposit. However, PVD may be preferred in applications where high vacuum and temperature conditions are not a concern.
- Hybrid PVD Techniques: Hybrid PVD techniques, which combine elements of cathodic arc evaporation and magnetron sputtering, offer potential advantages in terms of deposition rate and degree of ionization. However, these techniques are less commonly used due to limited research and may not yet offer the same level of versatility and cost-effectiveness as LPCVD.
-
Applications of LPCVD:
- Semiconductor Manufacturing: LPCVD is widely used in the production of semiconductor devices, where it is valued for its ability to produce high-quality, uniform films with specific properties.
- MEMS Devices: The precise thin-film deposition capabilities of LPCVD make it particularly useful in the fabrication of MEMS devices, where uniformity and conformal coverage are critical.
- Advanced Materials: LPCVD is also used in the preparation of advanced materials such as graphene and carbon nanotubes, which require precise control over film properties and deposition conditions.
In summary, LPCVD offers numerous advantages, including high-quality film deposition, versatility, and cost-effectiveness, making it a preferred method for many industrial applications. However, its high temperature requirements and complexity can be limiting factors, particularly for temperature-sensitive materials and processes. Understanding these advantages and disadvantages is crucial for selecting the appropriate deposition method for specific applications.
Summary Table:
Aspect | Advantages | Disadvantages |
---|---|---|
Film Quality | High uniformity, fewer defects, excellent conformal step coverage | High temperature requirements may limit material options |
Versatility | Deposits a wide range of materials (e.g., SiO₂, Si₃N₄, graphene, nanotubes) | Complex process requiring skilled operators |
Cost-Effectiveness | Relatively cost-effective compared to other deposition methods | Increased complexity can raise operational costs |
Deposition Rate | Faster reaction rates due to reduced pressure | Material limitations for temperature-sensitive applications |
Applications | Ideal for semiconductor manufacturing, MEMS devices, and advanced materials | High vacuum and temperature conditions may not suit all processes |
Discover how LPCVD can optimize your thin-film deposition process—contact our experts today!