Rotary furnaces, also known as rotating furnaces, are widely used in various industrial applications due to their unique design and operational advantages. They offer benefits such as high energy efficiency, precise temperature control, and continuous production capabilities, making them suitable for processes like material sintering, coating preparation, chemical reactions, and heat treatment. However, they also have certain limitations, such as potential challenges in material placement and accessibility. This analysis explores the advantages and disadvantages of rotary furnaces in detail, providing insights into their suitability for different industrial applications.
Key Points Explained:
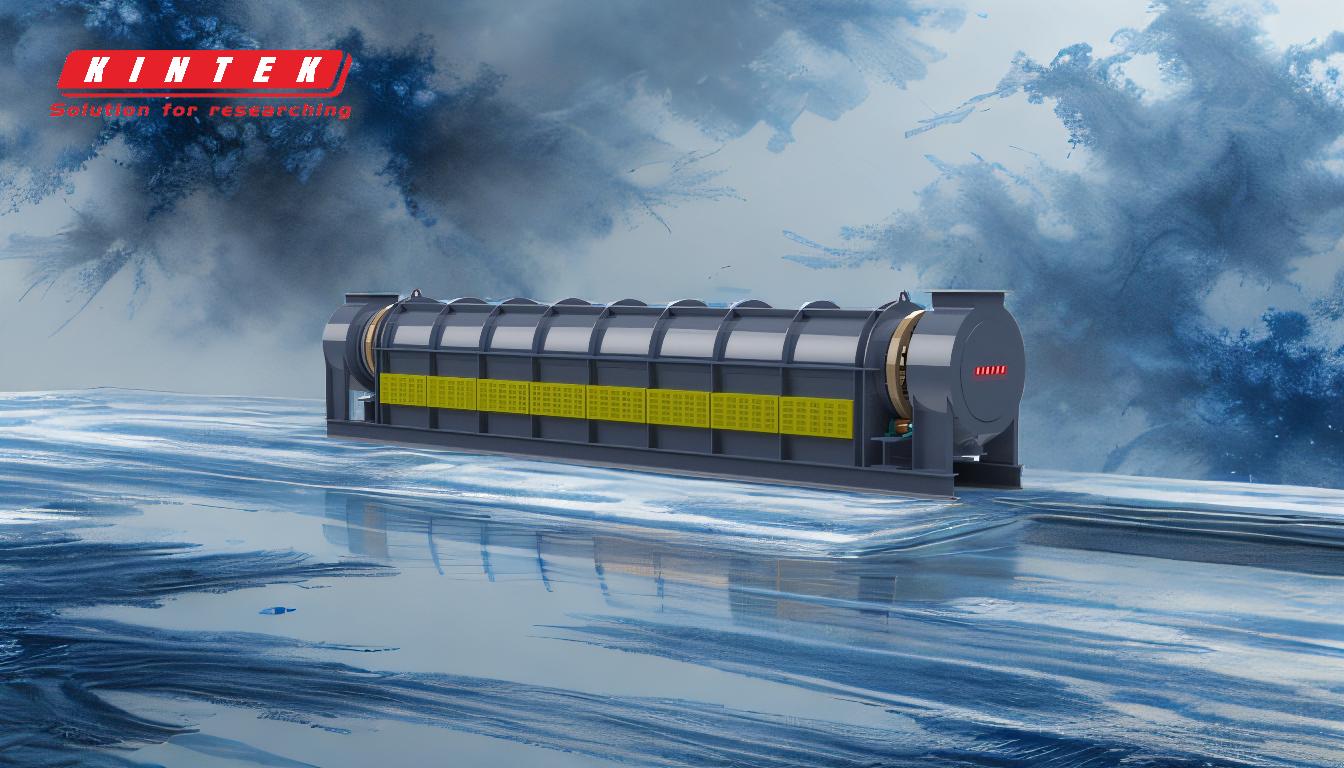
-
Advantages of Rotary Furnaces:
- High Energy Efficiency: Rotary furnaces are designed to maximize energy utilization compared to stationary furnaces. Their dynamic rotation method ensures uniform heat distribution, reducing energy consumption and improving overall efficiency.
- Continuous Production: These furnaces support continuous operation, which is ideal for large-scale industrial processes. This feature enhances productivity and reduces downtime.
- Precise Temperature Control: Rotary furnaces offer high-temperature control precision, ensuring consistent and uniform heating. This is critical for processes like sintering, annealing, and chemical reactions.
- Improved Gas Diffusion: The continuous movement of materials in a rotary furnace exposes the entire surface area to the atmosphere, enhancing gas diffusion and reducing gas consumption.
- Environmental Benefits: Rotary furnaces allow for centralized dust collection and low pollution emissions, contributing to energy conservation and environmental protection.
- Versatility: They are suitable for a wide range of applications, including material sintering, coating preparation, and catalyst production, due to their ability to address issues like heat accumulation and temperature differences.
-
Disadvantages of Rotary Furnaces:
- Material Placement Challenges: The design of rotary furnaces can make it harder to access the interior, requiring careful placement of materials during use. This can be a limitation for processes requiring frequent material adjustments.
- Initial Warm-Up Time: While rotary furnaces are efficient once operational, they may take longer to reach the desired temperature compared to some other heating methods, which could be a drawback for time-sensitive projects.
- Complexity in Maintenance: The rotating mechanism and high-temperature environment may require more frequent maintenance and specialized expertise to ensure optimal performance.
- Limited Refining Capacity: Similar to induction furnaces, rotary furnaces may have limitations in refining capacity, requiring pre-processed charge materials free of oxides and of known composition.
-
Comparison with Other Furnace Types:
- Muffle Furnaces: Rotary furnaces offer better energy efficiency and continuous production capabilities compared to muffle furnaces, which are slower to heat up and have limited accessibility.
- Induction Furnaces: Unlike induction furnaces, rotary furnaces do not require a heating device for slag treatment and operate with lower energy consumption. However, both furnace types share limitations in refining capacity.
- Traditional Equipment: Rotary furnaces are gradually replacing traditional equipment like mesh belt furnaces and push plate kilns due to their ability to address issues like air leakage, heat accumulation, and temperature differences, ensuring uniformity in material properties.
-
Applications of Rotary Furnaces:
- Material Sintering: Rotary furnaces are ideal for sintering ceramics and metal powders, improving density, strength, and corrosion resistance.
- Coating Preparation: They are used to create ceramic or metal coatings on substrates, enhancing wear resistance, corrosion resistance, and aesthetics.
- Chemical Reactions: Rotary furnaces facilitate the synthesis of new materials and the preparation of catalysts.
- Heat Treatment and Annealing: They improve the structure and performance of metal materials through precise heat treatment processes.
In summary, rotary furnaces offer significant advantages in terms of energy efficiency, continuous production, and precise temperature control, making them suitable for a wide range of industrial applications. However, challenges related to material placement, initial warm-up time, and maintenance complexity should be considered when evaluating their suitability for specific processes.
Summary Table:
Aspect | Advantages | Disadvantages |
---|---|---|
Energy Efficiency | High energy utilization, uniform heat distribution, reduced energy consumption | Initial warm-up time may be longer |
Production | Continuous operation, enhanced productivity, reduced downtime | Material placement challenges, limited accessibility |
Temperature Control | Precise and consistent heating, ideal for sintering and chemical reactions | Maintenance complexity due to rotating mechanism and high-temperature environment |
Environmental Impact | Low pollution emissions, centralized dust collection | Limited refining capacity, requires pre-processed materials |
Versatility | Suitable for sintering, coating, catalysts, and heat treatment |
Discover how rotary furnaces can optimize your industrial processes—contact our experts today!