Chemical Vapor Deposition (CVD) is a highly versatile and efficient method for thin film deposition, offering numerous advantages over other techniques. It is widely used in industries requiring high-performance coatings due to its ability to produce films with superior hardness, wear resistance, smoothness, and oxidation resistance. CVD can be applied to a wide range of materials, including ceramics, metals, and glass, and is capable of coating complex and precision surfaces. The process allows for optimization of gas compositions to achieve specific properties such as corrosion resistance, abrasion resistance, or high purity. Additionally, CVD films are durable and can withstand high-stress environments, extreme temperatures, and temperature variations. The method also provides excellent control over film thickness and uniformity, making it ideal for applications like electrical circuits and advanced materials.
Key Points Explained:
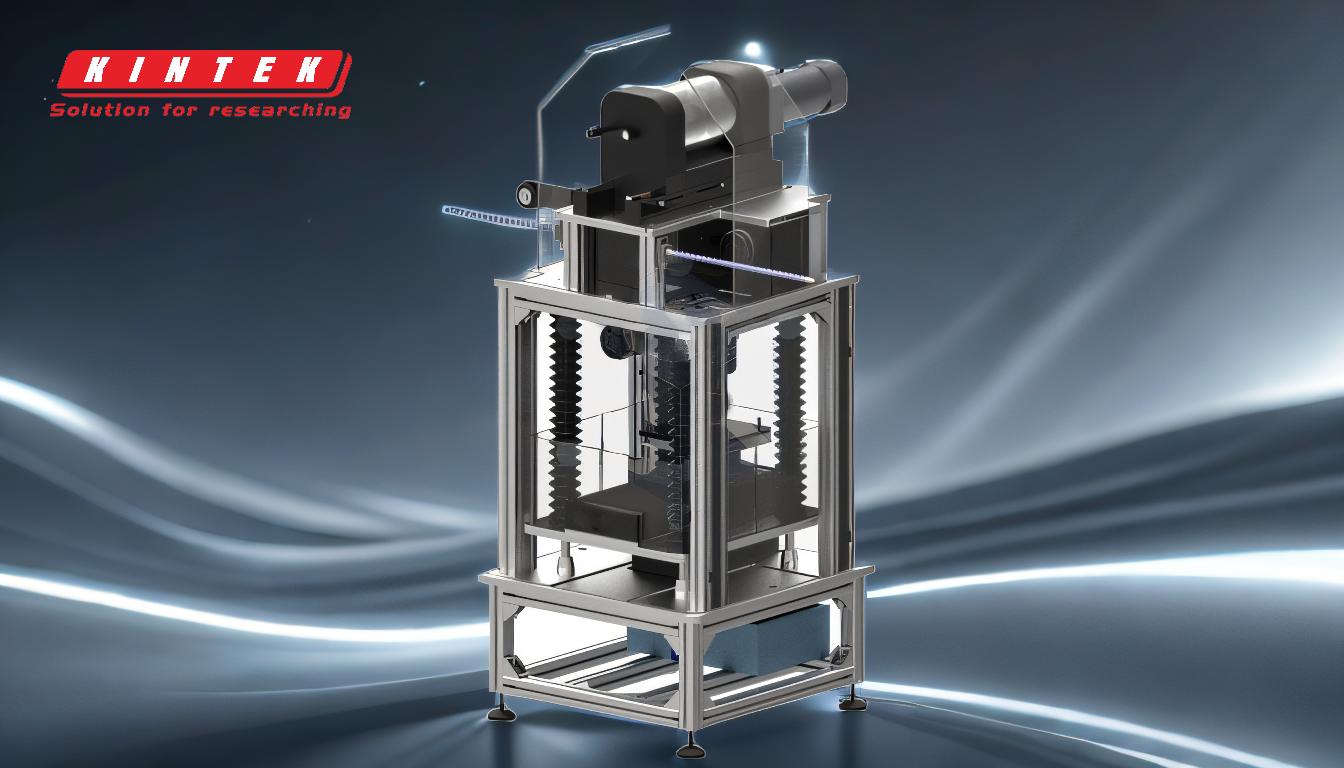
-
Versatility Across Materials
- CVD can be used on a diverse range of materials, including ceramics, metals, and glass. This versatility makes it suitable for a wide array of industrial applications, from electronics to aerospace.
- The ability to tailor gas compositions allows for the creation of coatings with specific properties, such as enhanced corrosion resistance, abrasion resistance, or high purity.
-
Durability in High-Stress Environments
- Thin films produced by CVD are known for their durability and ability to withstand high-stress environments. This makes them ideal for applications where mechanical wear, thermal stress, or chemical exposure are concerns.
- The coatings maintain their integrity even under extreme temperatures or rapid temperature variations, ensuring long-term performance.
-
Precision and Complex Surface Coating
- CVD excels at coating precision and complex surfaces, including intricate geometries and microstructures. This capability is crucial for industries like semiconductor manufacturing, where uniformity and precision are paramount.
- The process can achieve ultra-thin layers of material, which is essential for applications such as electrical circuits and nanotechnology.
-
High Purity and Uniformity
- CVD produces films with high purity and uniformity, which are critical for applications requiring consistent material properties. This is particularly important in the production of semiconductors and optical coatings.
- The method allows for the synthesis of both pure and complex materials at desired purity levels, ensuring high-quality results.
-
Control Over Film Properties
- CVD offers full control over the chemical and physical properties of the films by adjusting parameters such as temperature, pressure, gas flow rate, and gas concentration. This level of control enables the creation of tailored materials for specific applications.
- The ability to produce single- or polycrystalline thin films, as well as amorphous films, further enhances its versatility.
-
Scalability and Environmental Friendliness
- CVD is a scalable process, making it suitable for both small-scale research and large-scale industrial production. This scalability is a significant advantage over other deposition techniques.
- The process is considered environmentally friendly, as it often uses non-toxic precursors and generates minimal waste compared to other methods like Physical Vapor Deposition (PVD).
In summary, Chemical Vapor Deposition stands out as a superior method for thin film deposition due to its versatility, durability, precision, and control over film properties. Its ability to produce high-quality, uniform coatings on a wide range of materials makes it indispensable in modern manufacturing and advanced material synthesis.
Summary Table:
Advantage | Description |
---|---|
Versatility Across Materials | Works on ceramics, metals, glass; tailored gas compositions for specific needs. |
Durability | Withstands high stress, extreme temperatures, and rapid temperature changes. |
Precision Coating | Coats complex and precision surfaces, ideal for semiconductors and nanotech. |
High Purity & Uniformity | Produces consistent, high-quality films for critical applications. |
Control Over Film Properties | Adjustable parameters for tailored material properties. |
Scalability & Eco-Friendliness | Suitable for small- and large-scale production; minimal waste generation. |
Unlock the potential of Chemical Vapor Deposition for your applications—contact our experts today!