Chemical Vapor Deposition (CVD) and Physical Vapor Deposition (PVD) are both widely used techniques for depositing thin films, but CVD offers distinct advantages over PVD in certain applications. CVD excels in its ability to coat complex geometries uniformly, including deep holes and shaded areas, due to its non-line-of-sight deposition process. It also allows the use of volatile chemical compounds, enabling the deposition of materials that are difficult to evaporate in PVD. Additionally, CVD can operate at atmospheric pressure, simplifying the process setup compared to PVD, which typically requires a vacuum environment. These advantages make CVD particularly suitable for applications in microelectronics, where conformality, selectivity, and process flexibility are critical.
Key Points Explained:
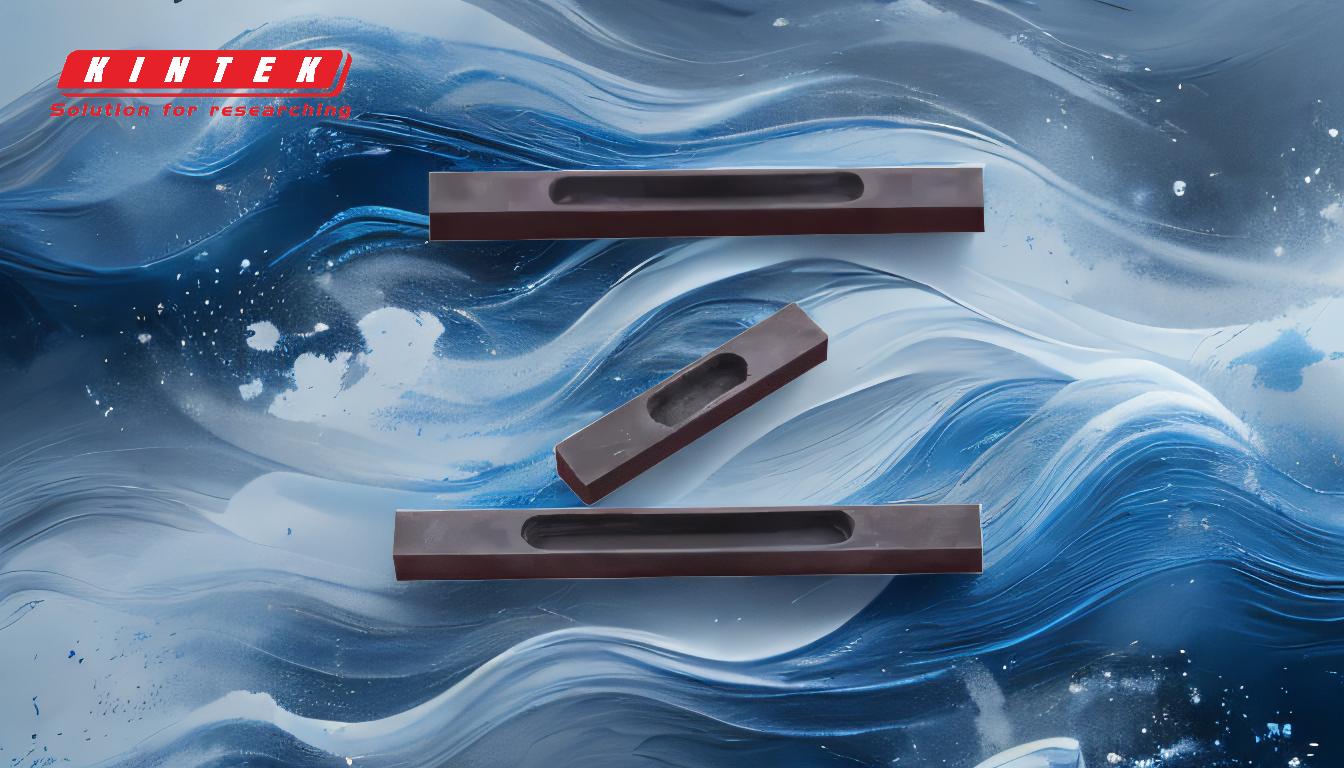
-
Non-Line-of-Sight Deposition:
- Unlike PVD, which requires a direct line of sight between the source and the substrate, CVD can deposit coatings uniformly on complex geometries, including deep holes, trenches, and shaded areas. This is particularly advantageous in industries like microelectronics, where intricate designs demand precise and consistent coating.
-
Use of Volatile Chemical Compounds:
- CVD can utilize volatile chemical precursors, enabling the deposition of materials that are challenging to evaporate in PVD. This expands the range of materials that can be deposited, including high-melting-point metals and ceramics, which are often required in advanced manufacturing processes.
-
Atmospheric Pressure Operation:
- CVD can be performed at atmospheric pressure, reducing the complexity and cost associated with maintaining a vacuum environment, as required in PVD. This makes CVD more accessible and cost-effective for certain industrial applications.
-
Conformality and Uniformity:
- CVD provides superior conformality, meaning it can produce uniform coatings even on highly irregular surfaces. This is critical for applications in semiconductor manufacturing, where even thickness and coverage are essential for device performance.
-
Process Flexibility:
- CVD offers greater flexibility in terms of precursor gases, deposition temperatures, and reaction conditions. This adaptability allows for the customization of film properties, such as composition, thickness, and microstructure, to meet specific application requirements.
-
Material Efficiency:
- CVD minimizes material waste by selectively coating only the heated areas of the substrate. This efficiency is further enhanced with advanced techniques like computer-controlled lasers, which can precisely target specific regions for deposition.
-
Microelectronics Applications:
- In microelectronics, CVD is often preferred over PVD due to its ability to produce high-quality, defect-free films with excellent selectivity and conformality. These properties are crucial for the fabrication of advanced semiconductor devices.
-
Economic Benefits:
- While both CVD and PVD can reduce manufacturing costs by extending tool life and improving performance, CVD's ability to deposit high-performance coatings on complex geometries often leads to greater cost savings in high-precision industries.
In summary, CVD's advantages over PVD lie in its ability to deposit uniform coatings on complex geometries, utilize a broader range of materials, operate at atmospheric pressure, and provide superior conformality and process flexibility. These benefits make CVD the preferred choice for many advanced manufacturing applications, particularly in microelectronics.
Summary Table:
Advantage | CVD | PVD |
---|---|---|
Deposition Method | Non-line-of-sight, uniform coating on complex geometries | Line-of-sight, limited to exposed surfaces |
Material Versatility | Can deposit high-melting-point metals and ceramics | Limited to materials that can be evaporated |
Operating Pressure | Can operate at atmospheric pressure | Requires a vacuum environment |
Conformality & Uniformity | Superior conformality on irregular surfaces | Less effective on complex geometries |
Process Flexibility | Highly adaptable to various precursor gases and conditions | Less flexible in customization |
Material Efficiency | Minimizes waste by selective coating | Less efficient due to line-of-sight limitations |
Economic Benefits | Greater cost savings in high-precision industries | Cost-effective for simpler applications |
Learn how CVD can optimize your manufacturing process—contact our experts today!