Electron beam deposition (E-Beam) is a highly versatile and efficient thin-film deposition technique with several advantages, particularly in applications requiring high purity, precision, and scalability. It involves vaporizing source materials using an electron beam in a vacuum chamber, allowing the resulting vapor to condense onto substrates. This method is favored for its ability to produce high-purity films, achieve precise and directional coatings, and enhance film adhesion and density through ion beam assistance. Additionally, E-Beam deposition is cost-effective and flexible, making it suitable for both high-precision and high-volume commercial applications.
Key Points Explained:
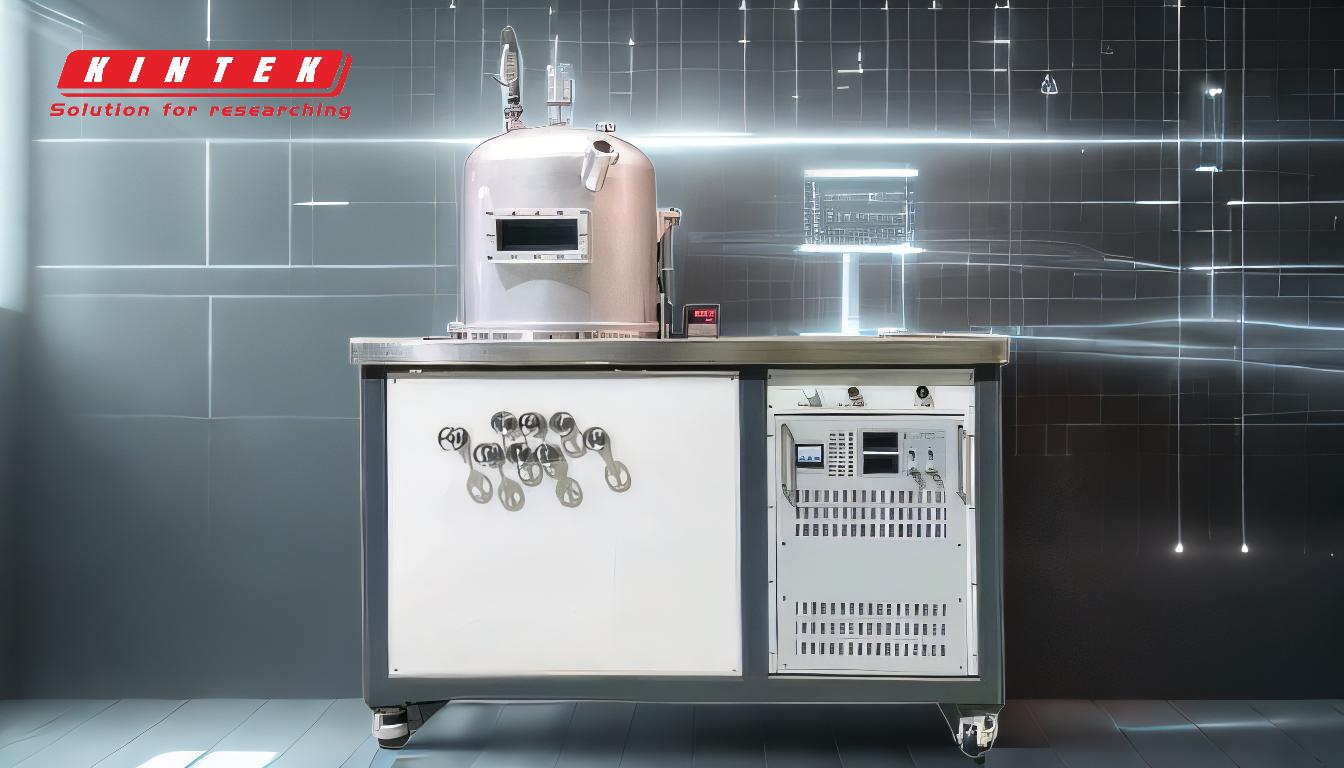
-
High-Purity Films:
- Direct Heating Mechanism: The evaporant is heated directly by the electron beam, minimizing contamination from crucible walls. This ensures high-purity films, as the process avoids almost all reactions with the crucible.
- Cooled Crucible: The use of a cooled crucible further reduces the risk of impurities, making E-Beam deposition ideal for applications requiring ultra-pure materials, such as in semiconductor and optical industries.
-
Highly Anisotropic Coating:
- Directional Vapor Deposition: The evaporant vapor moves in straight lines between the source and the substrate, enabling precise and directional coating. This is particularly useful for lift-off applications and other processes requiring controlled deposition.
- Precision and Control: The anisotropic nature of E-Beam deposition ensures uniform and consistent film thickness, which is critical for applications in microelectronics and nanotechnology.
-
Enhanced Adhesion and Density with Ion Beam Assistance:
- Ion Beam Bombardment: An ion beam within the vacuum chamber bombards the substrates before deposition, increasing the adhesion energy of the material to the substrate.
- Denser and More Robust Coatings: This results in denser, more robust coatings with less stress, improving the mechanical and thermal properties of the films. This enhancement is particularly beneficial for protective and functional coatings.
-
Precision Control and Conformal Coatings:
- Computer-Controlled Parameters: Precision computer control of heating, vacuum levels, substrate location, and rotation allows for the creation of conformal optical coatings with pre-specified thicknesses.
- Versatility in Applications: The ability to control deposition parameters with high precision makes E-Beam deposition suitable for a wide range of applications, including optical coatings, sensors, and advanced materials.
-
Efficiency in High-Temperature Applications:
- High Melting Temperature Materials: E-Beam deposition is highly efficient in transferring pure and precise metal coatings that require high melting temperatures. This makes it suitable for applications in aerospace, energy, and advanced manufacturing.
- Atomic and Molecular Level Precision: The technique achieves deposition at the atomic and molecular level, ensuring high precision and purity in the resulting coatings.
-
Cost-Effectiveness and Flexibility:
- Wider Array of Materials: E-Beam deposition uses a broader range of less expensive evaporative materials compared to other techniques like magnetron sputtering, which relies on costly sputter targets.
- Rapid Batch Processing: The method processes more rapidly in batch scenarios, making it ideal for high-volume commercial applications. This scalability is advantageous for industries requiring large-scale production of thin films.
-
Simplicity and Flexibility in Polymeric Coatings:
- Ease of Use: E-Beam deposition is simpler and more flexible for polymeric coatings compared to other techniques. This simplicity reduces operational complexity and costs.
- High-Volume Applications: The rapid processing capability in batch scenarios makes E-Beam deposition particularly suitable for high-volume commercial applications, such as in the packaging and automotive industries.
In summary, electron beam deposition offers a combination of high purity, precision, and scalability, making it a preferred choice for a wide range of industrial and scientific applications. Its ability to produce high-quality films with enhanced properties, coupled with cost-effectiveness and flexibility, underscores its importance in modern materials science and engineering.
Summary Table:
Key Advantages | Details |
---|---|
High-Purity Films | Direct heating and cooled crucibles minimize contamination for ultra-pure materials. |
Anisotropic Coating | Directional vapor deposition ensures precise and uniform film thickness. |
Enhanced Adhesion & Density | Ion beam assistance improves coating adhesion and mechanical properties. |
Precision Control | Computer-controlled parameters enable conformal coatings with pre-specified thicknesses. |
High-Temperature Efficiency | Ideal for high melting temperature materials with atomic-level precision. |
Cost-Effectiveness | Uses less expensive materials and enables rapid batch processing for high-volume production. |
**Flexibility in Polymeric Coatings | Simple and efficient for high-volume commercial applications. |
Ready to enhance your thin-film processes with electron beam deposition? Contact our experts today to learn more!