Electron beam evaporation is a highly efficient and versatile thin-film deposition technique widely used in various industries, including semiconductors, optics, and coatings. Its advantages stem from its ability to produce high-purity, uniform, and dense films with precise control over thickness and composition. This method utilizes a focused electron beam to heat and evaporate materials in a vacuum environment, minimizing contamination and enabling the deposition of materials with high melting points. The process is highly controllable, scalable, and compatible with a wide range of materials, making it a preferred choice for applications requiring high-quality thin films.
Key Points Explained:
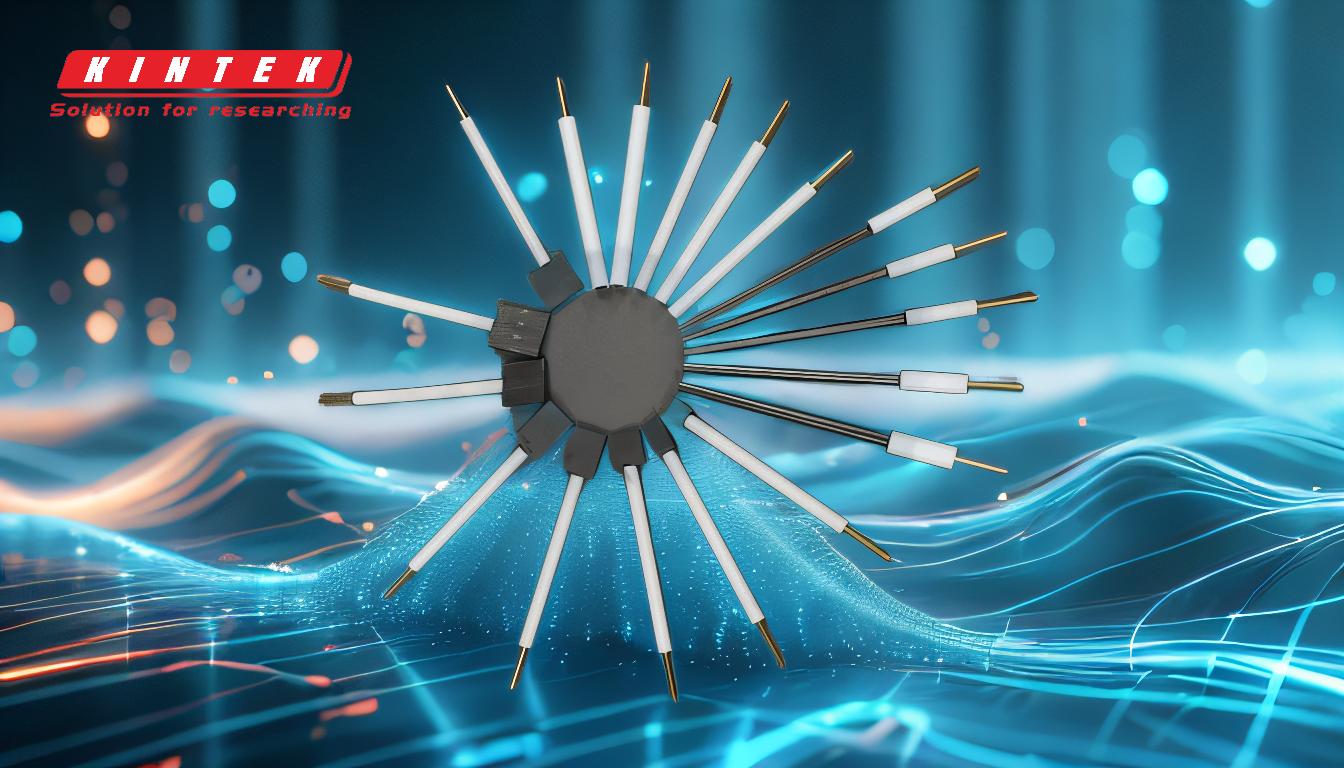
-
High Purity and Cleanliness:
- Electron beam evaporation occurs in a high-vacuum environment, which significantly reduces the presence of impurities and contaminants. This ensures the deposition of high-purity films, which is critical for applications in electronics, optics, and other high-tech industries.
- The absence of reactive gases or other contaminants during the process prevents oxidation or unwanted chemical reactions, preserving the material's intrinsic properties.
-
Versatility with High-Melting-Point Materials:
- Electron beam evaporation can deposit materials with extremely high melting points, such as tungsten, tantalum, and ceramics, which are difficult to process using other methods like thermal evaporation.
- The focused electron beam delivers concentrated energy to the target material, allowing it to reach the necessary temperatures for evaporation without affecting the surrounding environment.
-
Precise Control Over Film Thickness and Composition:
- The process allows for precise control over the deposition rate and film thickness, enabling the creation of ultra-thin films with nanometer-level accuracy.
- Multi-layer films with specific compositions can be easily achieved by sequentially evaporating different materials, making it ideal for advanced applications like optical coatings and semiconductor devices.
-
Uniform and Dense Film Formation:
- The high energy of the electron beam ensures that the evaporated material forms a dense and uniform film on the substrate, which is essential for applications requiring high mechanical strength and durability.
- The uniformity of the film is further enhanced by the ability to rotate or move the substrate during deposition, ensuring even coverage.
-
Scalability and Compatibility:
- Electron beam evaporation is scalable, making it suitable for both small-scale laboratory research and large-scale industrial production.
- It is compatible with a wide range of materials, including metals, alloys, and ceramics, making it a versatile choice for diverse applications.
-
Minimal Substrate Heating:
- Unlike some other deposition methods, electron beam evaporation minimizes heat transfer to the substrate, which is crucial for temperature-sensitive materials or substrates.
- This feature allows for the deposition of films on materials that might otherwise degrade or warp under high temperatures.
-
High Deposition Rates:
- The process offers high deposition rates, which can significantly reduce production time compared to other thin-film deposition techniques.
- This efficiency is particularly beneficial for industrial applications where throughput is a critical factor.
-
Environmental and Safety Benefits:
- The vacuum environment used in electron beam evaporation eliminates the need for hazardous chemicals or gases, making it a cleaner and safer process compared to some alternative methods.
- The absence of toxic byproducts or emissions contributes to a more environmentally friendly manufacturing process.
In summary, electron beam evaporation stands out as a superior thin-film deposition technique due to its ability to produce high-purity, uniform, and dense films with precise control. Its compatibility with high-melting-point materials, scalability, and minimal environmental impact make it an ideal choice for a wide range of advanced applications.
Summary Table:
Advantage | Description |
---|---|
High Purity and Cleanliness | High-vacuum environment reduces impurities, ensuring clean, high-purity films. |
Versatility with High-Melting Materials | Deposits materials like tungsten and ceramics, which are hard to process otherwise. |
Precise Control Over Film Thickness | Enables nanometer-level accuracy and multi-layer film creation. |
Uniform and Dense Film Formation | Produces dense, uniform films essential for durability and strength. |
Scalability and Compatibility | Suitable for both lab research and industrial production with diverse materials. |
Minimal Substrate Heating | Reduces heat transfer to substrates, ideal for temperature-sensitive materials. |
High Deposition Rates | Offers faster production times compared to other methods. |
Environmental and Safety Benefits | Cleaner, safer process with no toxic byproducts or emissions. |
Ready to elevate your thin-film deposition process? Contact us today to learn more about electron beam evaporation solutions!