Ion beam deposition (IBD) is a highly advanced thin-film deposition technique that offers numerous advantages, making it a preferred choice for applications requiring precision, quality, and customization. The process involves using a highly collimated ion beam to deposit materials onto a substrate, resulting in films with exceptional properties such as high density, superior adhesion, and minimal defects. IBD provides independent control over film stoichiometry and thickness, ensuring uniformity and repeatability. Additionally, its high-energy bonding properties and environmental stability make it ideal for demanding applications in optics, electronics, and other high-tech industries. The process is also highly automated, reducing the need for operator intervention while delivering consistent, high-quality results.
Key Points Explained:
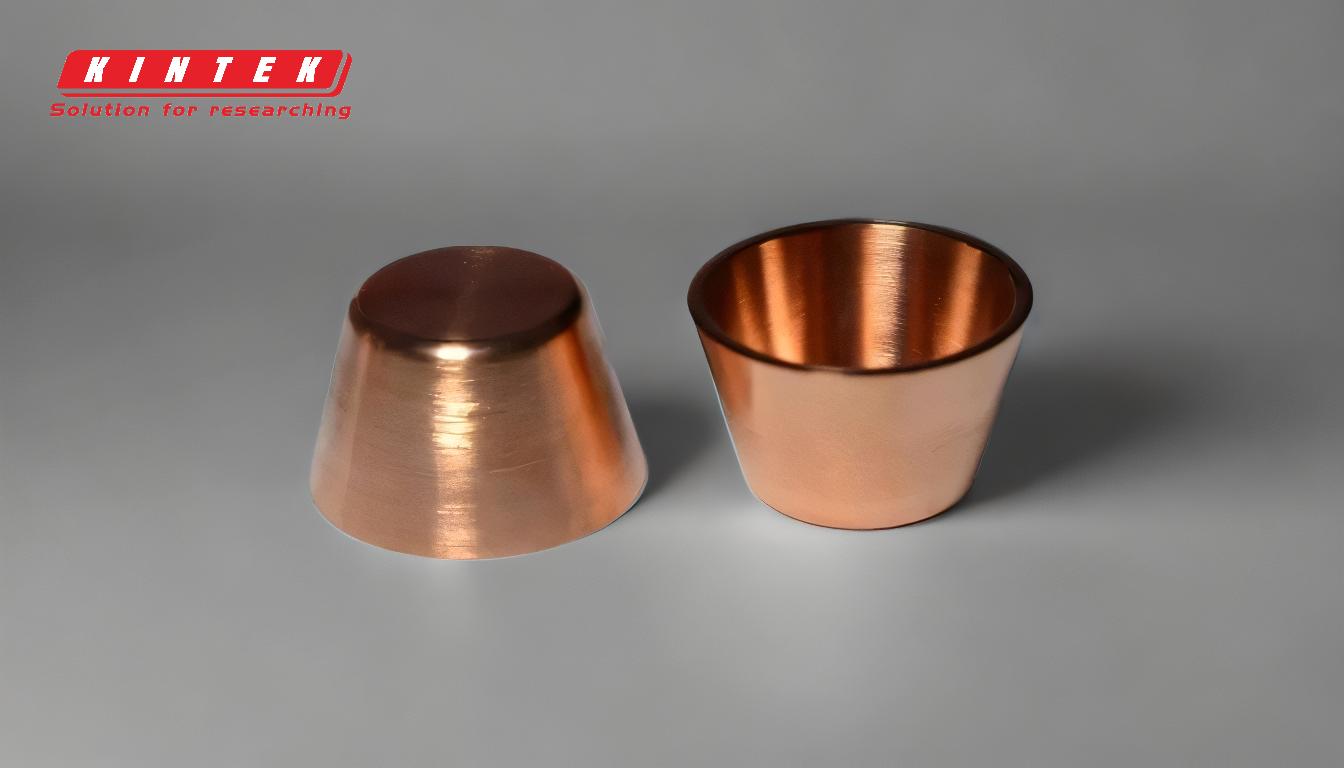
-
High Precision and Control:
- IBD offers unparalleled control over deposition parameters, such as ion current density and target sputtering rate, which are difficult to achieve with other methods.
- The highly collimated ion beam ensures that all ions possess equal energy, allowing for precise control over film stoichiometry and thickness.
- This precision enables the creation of films with extremely tight thickness tolerances and uniformity, which is critical for applications like optical coatings and semiconductor devices.
-
Superior Film Properties:
- Films produced by IBD are characterized by a dense structure, which enhances their mechanical and environmental durability.
- The process ensures superior adhesion between the film and the substrate, reducing the risk of delamination or failure.
- IBD films exhibit increased purity and fewer defects, making them suitable for high-performance applications where material quality is paramount.
-
Customization and Flexibility:
- IBD allows for a high level of customization in terms of target material composition and film properties.
- The process can be tailored to meet specific requirements, such as achieving ideal target composition or optimizing film performance for particular applications.
- This flexibility makes IBD suitable for a wide range of materials and industries, from optics to electronics.
-
Low Impact on Substrate:
- The ion beam used in IBD has a low impact on the substrate, minimizing the risk of damage or contamination.
- This is particularly important for delicate or sensitive substrates, such as those used in microelectronics or biomedical devices.
-
High-Quality Deposits:
- IBD produces high-quality deposits with low absorption and scattering, making it ideal for applications requiring high transmission, such as optical coatings.
- The films are uniform and dense, ensuring consistent performance and durability in demanding environments.
-
Environmental Stability and Durability:
- Films deposited using IBD exhibit excellent environmental stability, making them resistant to degradation from factors like moisture, temperature, and mechanical stress.
- This durability is essential for applications in harsh environments, such as aerospace or automotive industries.
-
Automation and Efficiency:
- IBD is a highly automated process, reducing the need for operator supervision and ensuring consistent, high-quality results.
- The automation also improves efficiency, making it a cost-effective solution for large-scale production.
-
Versatility in Applications:
- IBD is widely used in modern technology, including optics, electronics, and energy storage, due to its ability to produce smooth, dense, and high-performance films.
- Its versatility extends to both research and industrial applications, where it is used to develop advanced materials and coatings.
In summary, ion beam deposition stands out as a superior thin-film deposition technique due to its precision, flexibility, and ability to produce high-quality, durable films. Its advantages make it an indispensable tool in industries where performance, reliability, and customization are critical.
Summary Table:
Advantage | Description |
---|---|
High Precision and Control | Unparalleled control over deposition parameters, ensuring tight tolerances. |
Superior Film Properties | Dense, defect-free films with excellent adhesion and durability. |
Customization and Flexibility | Tailored to specific material and application requirements. |
Low Impact on Substrate | Minimizes damage or contamination, ideal for sensitive substrates. |
High-Quality Deposits | Uniform, dense films with low absorption and scattering. |
Environmental Stability | Resistant to moisture, temperature, and mechanical stress. |
Automation and Efficiency | Highly automated process for consistent, cost-effective results. |
Versatility in Applications | Suitable for optics, electronics, energy storage, and more. |
Unlock the potential of ion beam deposition for your projects—contact our experts today!