Metal-Organic Chemical Vapor Deposition (MOCVD) is a highly advanced and specialized technique used in the semiconductor industry for the growth of thin films, particularly compound semiconductors. It offers several advantages over other deposition methods, such as LPCVD (Low-Pressure Chemical Vapor Deposition). While LPCVD is effective for conductive materials and semiconductor devices, MOCVD provides unique benefits that make it indispensable for applications requiring precise control over material composition, uniformity, and scalability. Below, we explore the key advantages of MOCVD in detail.
Key Points Explained:
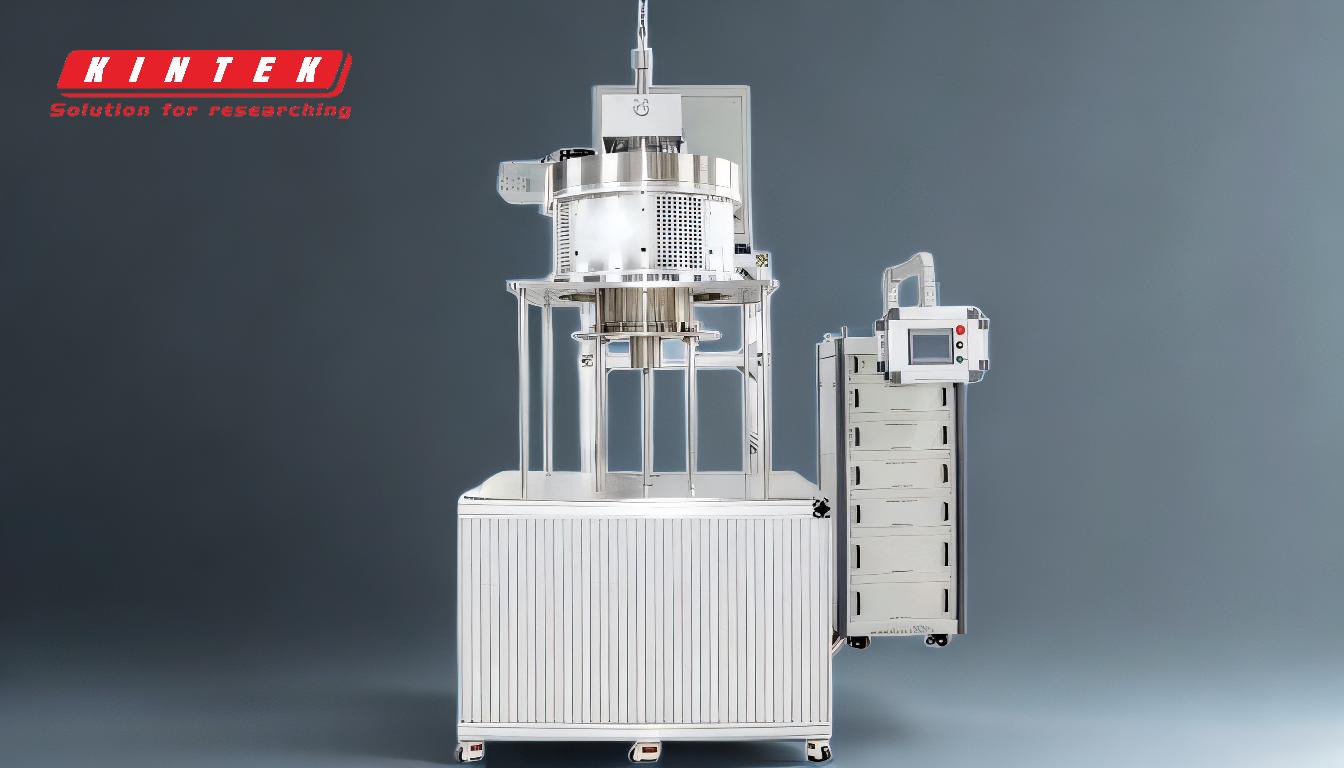
-
Precise Control Over Material Composition
- MOCVD allows for the precise control of the composition and doping levels of the deposited materials. This is achieved by using metal-organic precursors, which can be finely tuned to achieve the desired stoichiometry.
- This level of control is critical for applications such as the growth of III-V compound semiconductors (e.g., GaN, InP) used in optoelectronics and high-frequency devices.
- Unlike LPCVD, which relies on simpler chemical precursors, MOCVD's use of metal-organic compounds enables the growth of complex multi-layer structures with atomic-level precision.
-
High-Quality, Uniform Films
- MOCVD is renowned for producing high-quality, uniform films with excellent thickness control. This uniformity is essential for applications like light-emitting diodes (LEDs), laser diodes, and solar cells, where even minor variations can significantly impact performance.
- The process operates at relatively low temperatures compared to other deposition methods, reducing the risk of defects and improving the crystalline quality of the films.
- The ability to grow epitaxial layers with minimal defects ensures superior electrical and optical properties, making MOCVD ideal for high-performance devices.
-
Scalability for Mass Production
- MOCVD systems are highly scalable, making them suitable for industrial-scale production. This scalability is crucial for meeting the growing demand for semiconductor devices in industries such as telecommunications, consumer electronics, and renewable energy.
- Modern MOCVD reactors can handle multiple wafers simultaneously, significantly increasing throughput and reducing production costs.
- The ability to grow large-area films with consistent quality ensures that MOCVD remains a cost-effective solution for high-volume manufacturing.
-
Versatility in Material Deposition
- MOCVD is capable of depositing a wide range of materials, including binary, ternary, and quaternary compounds. This versatility makes it suitable for diverse applications, from infrared detectors to high-efficiency solar cells.
- The process can be adapted to grow both thin films and nanostructures, such as quantum dots and nanowires, expanding its utility in cutting-edge research and development.
- Unlike LPCVD, which is limited to simpler materials, MOCVD's flexibility enables the growth of complex heterostructures with tailored properties.
-
Low-Temperature Operation
- MOCVD operates at lower temperatures compared to other deposition techniques, such as molecular beam epitaxy (MBE). This reduces thermal stress on the substrates and minimizes the risk of unwanted diffusion or intermixing of layers.
- The lower processing temperatures also make MOCVD compatible with temperature-sensitive materials and substrates, broadening its applicability in advanced device fabrication.
-
Enhanced Process Control and Reproducibility
- MOCVD systems are equipped with advanced monitoring and control mechanisms, ensuring high reproducibility and consistency across batches.
- Parameters such as gas flow rates, temperature, and pressure can be precisely regulated, leading to highly repeatable results.
- This level of control is particularly important for industries where device performance and reliability are paramount.
-
Energy Efficiency and Environmental Benefits
- MOCVD systems are designed to minimize waste and optimize resource utilization, making them more energy-efficient compared to traditional deposition methods.
- The use of metal-organic precursors, which decompose cleanly at lower temperatures, reduces the environmental impact of the process.
- These factors contribute to the sustainability of MOCVD as a manufacturing technology, aligning with global efforts to reduce carbon footprints.
In summary, MOCVD offers unparalleled advantages in terms of material control, film quality, scalability, and versatility. Its ability to produce high-performance semiconductor devices with precision and efficiency makes it a cornerstone of modern semiconductor manufacturing. While LPCVD remains a valuable technique for certain applications, MOCVD's unique capabilities ensure its continued dominance in the field of advanced materials and device fabrication.
Summary Table:
Advantage | Description |
---|---|
Precise Control Over Composition | Achieves atomic-level precision with metal-organic precursors, ideal for III-V semiconductors. |
High-Quality, Uniform Films | Produces defect-free, uniform films essential for LEDs, lasers, and solar cells. |
Scalability for Mass Production | Handles multiple wafers simultaneously, reducing costs and increasing throughput. |
Versatility in Material Deposition | Deposits binary, ternary, and quaternary compounds for diverse applications. |
Low-Temperature Operation | Reduces thermal stress and is compatible with temperature-sensitive materials. |
Enhanced Process Control | Ensures reproducibility and consistency with advanced monitoring systems. |
Energy Efficiency | Minimizes waste and optimizes resource utilization, aligning with sustainability goals. |
Unlock the full potential of MOCVD for your semiconductor projects—contact our experts today!