Plasma-enhanced chemical vapor deposition (PECVD) is a highly versatile and efficient thin-film deposition technique that leverages plasma to enhance chemical reactions at relatively low temperatures. This method offers numerous advantages, including the ability to deposit a wide range of materials with specific properties, operate at low temperatures suitable for heat-sensitive substrates, and produce high-quality, uniform films with excellent adhesion. PECVD is particularly advantageous for coating parts with complex geometries and achieving high deposition rates, making it a preferred choice in industries requiring precision and durability.
Key Points Explained:
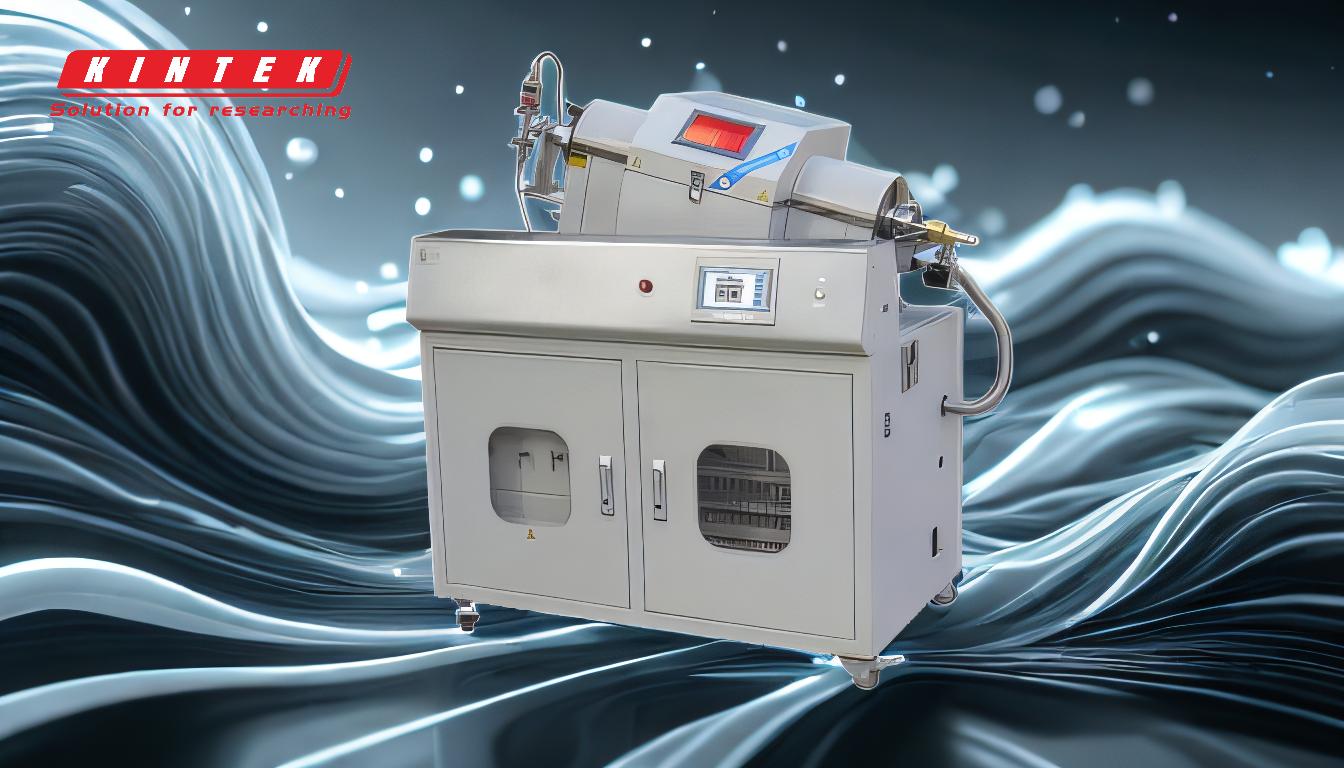
-
Low-Temperature Operation:
- PECVD allows deposition at temperatures below 200°C, significantly lower than traditional CVD methods, which require temperatures around 1,000°C. This makes it suitable for heat-sensitive substrates, such as polymers or certain metals, that would otherwise degrade at high temperatures. The low-temperature process also reduces thermal stress on the substrate, preserving its structural integrity.
-
Versatility in Material Deposition:
- PECVD can deposit a variety of materials, including diamond-like carbon (DLC) for wear resistance and silicon compounds for insulating properties. This versatility enables the customization of thin films to meet specific application requirements, such as enhancing durability, improving electrical properties, or providing optical transparency.
-
High-Quality, Uniform Films:
- The use of plasma in PECVD ensures the formation of thin films with high quality, uniform thickness, and resistance to cracking. The plasma enhances the reactivity of gas precursors, leading to better control over film composition and microstructure. This results in films with excellent optical, thermal, and electrical properties.
-
Excellent Adhesion:
- PECVD produces films with strong adhesion to the substrate, which is critical for applications requiring long-term durability. The plasma treatment of the substrate surface prior to deposition improves bonding between the film and the substrate, reducing the risk of delamination.
-
Coating Complex Geometries:
- PECVD is capable of uniformly coating parts with complex shapes and irregular surfaces. This is particularly beneficial in industries such as aerospace, automotive, and electronics, where components often have intricate designs that are challenging to coat using other methods.
-
High Deposition Rates:
- PECVD offers high deposition rates, making it efficient for mass production. The plasma-enhanced reactions accelerate the deposition process, allowing for faster production cycles without compromising film quality.
-
Energy Efficiency and Process Stability:
- Techniques like microwave plasma vapor deposition (MPCVD) within PECVD avoid the use of metal electrodes, reducing contamination and improving process stability. The concentrated gas discharge area generates high-density plasma, enhancing the efficiency of the deposition process and ensuring consistent film quality over time.
-
Applications in Advanced Materials:
- PECVD is widely used in the production of advanced materials, such as high-quality diamond films for optical and electronic applications. The ability to control film properties at the molecular level makes PECVD indispensable in the development of cutting-edge technologies.
In summary, plasma enhanced chemical vapour deposition (PECVD) combines the benefits of low-temperature processing, material versatility, and high-quality film production, making it a superior choice for a wide range of industrial applications. Its ability to coat complex geometries and achieve high deposition rates further enhances its appeal for manufacturers seeking precision and efficiency.
Summary Table:
Advantage | Description |
---|---|
Low-Temperature Operation | Deposition below 200°C, ideal for heat-sensitive substrates. |
Versatility in Material Deposition | Deposits materials like DLC and silicon compounds for tailored properties. |
High-Quality, Uniform Films | Produces films with excellent optical, thermal, and electrical properties. |
Excellent Adhesion | Ensures strong bonding to substrates for long-term durability. |
Coating Complex Geometries | Uniformly coats intricate shapes and irregular surfaces. |
High Deposition Rates | Accelerates production cycles without compromising quality. |
Energy Efficiency | Reduces contamination and improves process stability with MPCVD techniques. |
Applications in Advanced Materials | Used for high-quality diamond films and cutting-edge technologies. |
Unlock the full potential of PECVD for your industrial needs—contact our experts today!