Physical Vapor Deposition (PVD) and Chemical Vapor Deposition (CVD) are both widely used techniques for creating thin films, but they differ significantly in their processes and resulting properties. PVD involves vaporizing a solid material in a vacuum and depositing it onto a substrate, while CVD uses chemical reactions to deposit a thin film from a gaseous precursor. PVD offers several advantages over CVD, including the ability to deposit nearly any inorganic and some organic materials, improved material properties compared to the substrate, and being more environmentally friendly than alternatives like electroplating. Additionally, PVD coatings are known for their durability, corrosion resistance, and exceptional abrasion resistance, making them suitable for high-temperature and high-impact applications. CVD, on the other hand, excels in conformal coating of irregular surfaces and is often preferred for applications requiring precise control over film composition and uniformity. However, PVD's lower environmental impact and versatility in material deposition make it a preferred choice in many industrial applications.
Key Points Explained:
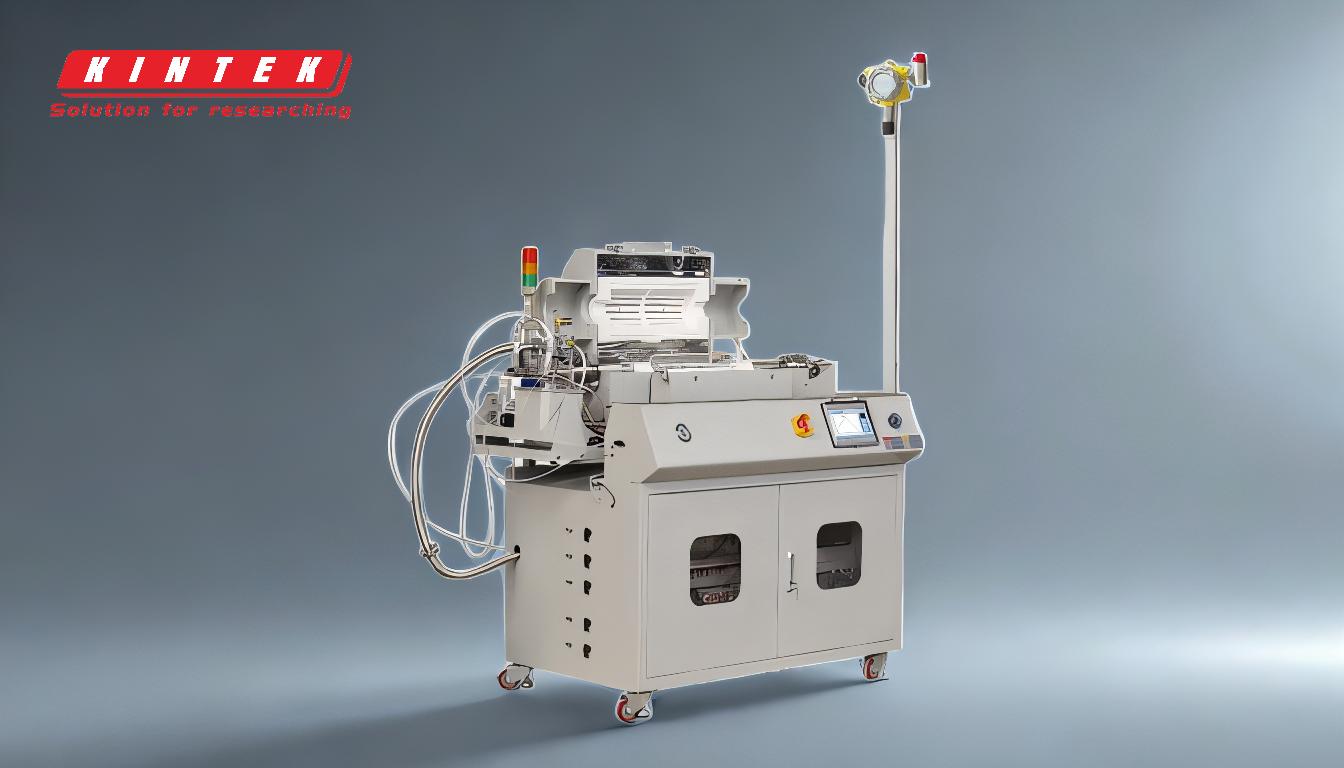
-
Material Versatility:
- PVD can deposit nearly any type of inorganic material and some organic materials, offering greater flexibility in coating applications. This versatility allows for the creation of coatings with specific properties tailored to the needs of the substrate.
- CVD, while also versatile, is often limited by the chemical reactivity of the precursors and the need for specific reaction conditions.
-
Improved Material Properties:
- PVD coatings often exhibit improved properties such as higher durability, corrosion resistance, and abrasion resistance compared to the substrate material. These properties make PVD coatings ideal for applications requiring long-lasting performance under harsh conditions.
- CVD coatings can also provide excellent properties, but they may not always match the mechanical strength and wear resistance of PVD coatings.
-
Environmental Friendliness:
- PVD is considered more environmentally friendly than traditional coating techniques like electroplating and painting. It produces fewer harmful by-products and does not require the use of toxic chemicals.
- CVD, while effective, often involves the use of toxic gases and requires extensive gas management infrastructure, which can increase environmental and safety concerns.
-
Durability and Corrosion Resistance:
- PVD coatings are known for their exceptional durability and corrosion resistance, making them suitable for high-temperature and high-impact applications. These coatings rarely require protective topcoats, reducing maintenance and long-term costs.
- CVD coatings can also provide good corrosion resistance, but they may not always offer the same level of durability as PVD coatings, especially in high-stress environments.
-
Abrasion Resistance:
- PVD coatings offer superior abrasion resistance, making them ideal for applications where the coating is subjected to frequent wear and tear. This property is particularly important in industries such as automotive, aerospace, and tool manufacturing.
- CVD coatings can provide good abrasion resistance, but they may not always match the performance of PVD coatings in highly abrasive environments.
-
High-Temperature and Impact Strength:
- PVD coatings are capable of withstanding high temperatures and impact forces, making them suitable for use in extreme conditions. This makes them a preferred choice for applications in industries such as aerospace, where components are exposed to high stress and temperature fluctuations.
- CVD coatings can also perform well at high temperatures, but they may not always offer the same level of impact resistance as PVD coatings.
-
Conformal Coating:
- CVD has an advantage in conformal coating, as it can deposit films on substrates with irregular surfaces or on large quantities of closely packed substrates. This is due to the higher pressure and laminar flow properties of CVD, which allow for uniform deposition even on complex geometries.
- PVD, while effective, is typically a line-of-sight process, meaning it may not coat hidden or recessed areas as effectively as CVD.
-
Cost and Infrastructure:
- PVD generally requires a high vacuum environment, which can increase initial setup costs. However, it often results in lower long-term costs due to reduced maintenance and longer-lasting coatings.
- CVD, while potentially less expensive in terms of initial infrastructure (due to higher operating pressures), may incur higher costs related to gas management and safety measures, especially when dealing with toxic precursors.
In summary, PVD offers several advantages over CVD, particularly in terms of material versatility, improved material properties, environmental friendliness, and durability. These benefits make PVD a preferred choice for many industrial applications, especially those requiring high-performance coatings under extreme conditions. However, CVD remains a valuable technique for applications requiring conformal coatings and precise control over film composition.
Summary Table:
Aspect | PVD | CVD |
---|---|---|
Material Versatility | Can deposit nearly any inorganic and some organic materials. | Limited by chemical reactivity and specific reaction conditions. |
Durability | Exceptional durability and corrosion resistance. | Good durability but may not match PVD in high-stress environments. |
Environmental Impact | More environmentally friendly with fewer harmful by-products. | Involves toxic gases and requires extensive gas management. |
Abrasion Resistance | Superior abrasion resistance for high-wear applications. | Good abrasion resistance but may not match PVD in highly abrasive environments. |
High-Temperature Use | Suitable for high-temperature and high-impact applications. | Performs well at high temperatures but may lack impact resistance. |
Conformal Coating | Limited by line-of-sight process. | Excels in conformal coating of irregular surfaces. |
Cost | Higher initial setup costs but lower long-term maintenance. | Potentially lower initial costs but higher gas management expenses. |
Ready to leverage the advantages of PVD for your applications? Contact us today to learn more!