SiC (Silicon Carbide) technology offers significant advantages over traditional materials, particularly in manufacturing and industrial applications. Its superior performance in harsh environments, cost efficiency, and ability to enhance productivity make it a preferred choice for modern equipment and consumables. Below, we explore the key advantages of SiC technology in detail.
Key Points Explained:
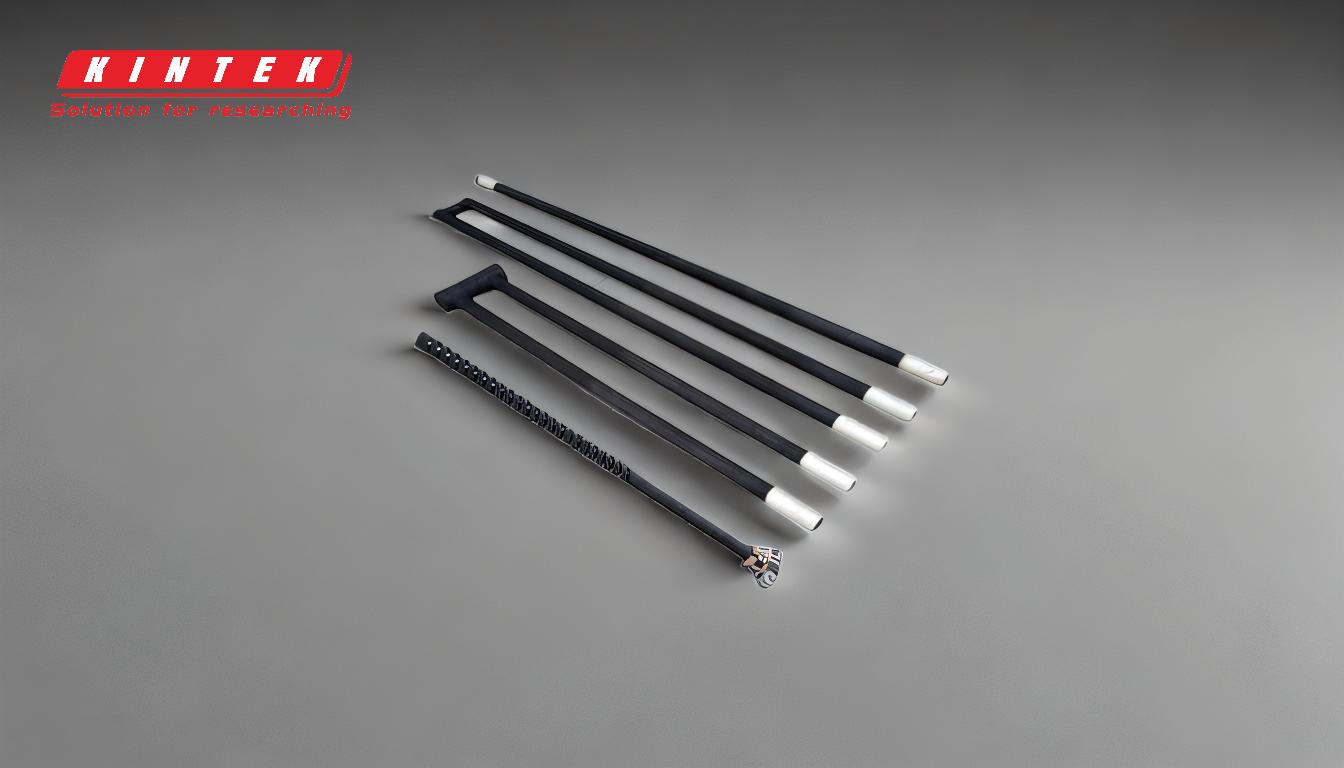
-
Outperforms Traditional Materials in Harsh Environments
- SiC exhibits exceptional resistance to chemical and plasma environments, making it ideal for industries like semiconductor manufacturing, where exposure to corrosive substances is common.
- Its durability ensures consistent performance even under extreme conditions, reducing the risk of material degradation and failure.
-
Lower Cost of Ownership
- While the initial investment in SiC-based equipment or components may be higher, its long-term benefits outweigh the costs.
- SiC extends the lifespan of manufacturing equipment, reducing the frequency of replacements and maintenance.
- Lower energy consumption and improved efficiency further contribute to cost savings over time.
-
Non-Particle Generating Properties
- SiC is non-particle generating, which is critical in cleanroom environments such as semiconductor fabrication.
- This property minimizes contamination risks, ensuring higher product quality and reducing the need for frequent cleaning or maintenance.
-
Faster Throughput and Cycle Times
- SiC enables faster processing speeds due to its high thermal conductivity and ability to withstand high temperatures.
- This results in shorter cycle times, allowing manufacturers to increase production rates and meet tighter deadlines.
-
Higher Yields
- By reducing contamination and improving process stability, SiC technology enhances overall yield rates.
- Higher yields translate to increased profitability and reduced waste, making it a valuable asset for high-precision industries.
-
Reduced Downtime
- SiC's durability and resistance to wear and tear significantly reduce equipment downtime.
- This ensures continuous operation, minimizing production interruptions and maximizing output.
-
Extended Equipment Lifespan
- SiC components are highly resistant to wear, corrosion, and thermal stress, leading to longer-lasting equipment.
- This reduces the need for frequent replacements, further lowering operational costs.
-
Elimination of Contamination
- SiC's non-reactive nature prevents contamination of sensitive materials or processes, ensuring consistent quality and reliability.
- This is particularly important in industries like pharmaceuticals, electronics, and aerospace, where even minor impurities can have significant consequences.
-
Improved Energy Efficiency
- SiC's high thermal conductivity and electrical efficiency contribute to reduced energy consumption.
- This not only lowers operational costs but also aligns with sustainability goals by minimizing energy waste.
-
Enhanced Productivity and Profitability
- By combining faster throughput, higher yields, and reduced downtime, SiC technology boosts overall productivity.
- These improvements directly impact profitability, making SiC a strategic investment for forward-thinking manufacturers.
In summary, SiC technology offers a comprehensive range of advantages, from improved performance in harsh environments to significant cost savings and enhanced productivity. Its unique properties make it an indispensable material for industries that demand precision, reliability, and efficiency.
Summary Table:
Advantage | Key Benefit |
---|---|
Harsh Environment Performance | Exceptional resistance to chemical and plasma environments, ensuring durability |
Lower Cost of Ownership | Reduced maintenance, energy savings, and extended equipment lifespan |
Non-Particle Generating | Minimizes contamination in cleanroom environments |
Faster Throughput and Cycle Times | Enables faster processing speeds and shorter cycle times |
Higher Yields | Improves process stability and reduces waste |
Reduced Downtime | Ensures continuous operation and maximizes output |
Extended Equipment Lifespan | Resists wear, corrosion, and thermal stress for longer-lasting equipment |
Elimination of Contamination | Prevents contamination in sensitive industries like electronics and aerospace |
Improved Energy Efficiency | Reduces energy consumption and aligns with sustainability goals |
Enhanced Productivity and Profitability | Boosts overall productivity and profitability |
Ready to enhance your manufacturing process with SiC technology? Contact us today to learn more!