The sputtering process is a highly advantageous deposition technique widely used in various industries, including microelectronics, semiconductors, and surface coating. It involves ejecting atoms from a solid target material into a gas phase using high-energy ions, which are then deposited onto a substrate within a vacuum chamber. This process offers superior film densification, reduced residual stresses, high deposition rates, and excellent control over film thickness and uniformity. Additionally, it enables in-situ substrate cleaning and is suitable for applications requiring precise morphological quality, such as controlling surface roughness, grain size, and stoichiometry.
Key Points Explained:
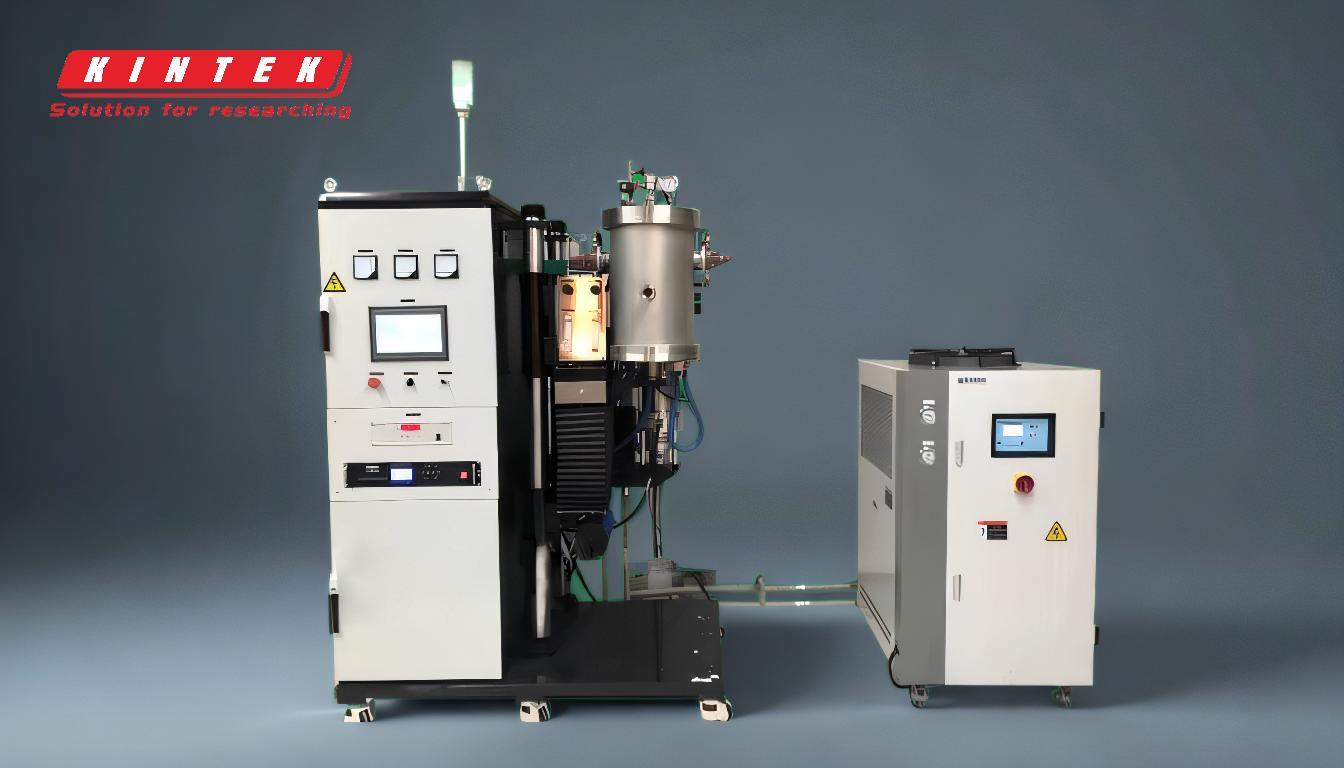
-
Better Film Densification:
- Sputtering produces dense and high-quality films due to the high-energy nature of the process. The ejected atoms have sufficient energy to form tightly packed layers on the substrate, resulting in films with minimal voids or defects. This is particularly beneficial for applications requiring robust and durable coatings.
-
Reduced Residual Stresses:
- The process operates at low or medium temperatures, which minimizes thermal stress on the substrate. This is crucial for delicate materials or components that could warp or degrade under high temperatures. The reduced stress also enhances the adhesion and longevity of the deposited film.
-
High Deposition Rates:
- Sputtering allows for high deposition rates, making it efficient for producing thick films without compromising quality. Unlike other deposition methods, there are no inherent thickness limits, enabling the creation of coatings tailored to specific industrial requirements.
-
In-Situ Substrate Cleaning:
- The vacuum chamber environment facilitates substrate cleaning before deposition. This step, often achieved through cathodic etching, removes surface contaminants and ensures better adhesion of the deposited material. It eliminates the need for separate cleaning processes, saving time and resources.
-
Precise Control Over Film Thickness and Uniformity:
- By adjusting process parameters such as power, pressure, and deposition time, sputtering offers exceptional control over film thickness and uniformity. This precision is vital for applications like semiconductor manufacturing, where even minor variations can impact performance.
-
Versatility in Material Deposition:
- Sputtering can deposit a wide range of materials, including metals, alloys, dielectrics, and nitrides. Techniques like direct current (DC) sputtering and radio frequency (RF) sputtering further enhance its versatility, making it suitable for diverse applications, from microelectronics to optical coatings.
-
Enhanced Morphological Quality:
- For applications requiring superior surface morphology, sputtering excels in controlling factors like roughness, grain size, and stoichiometry. This makes it ideal for industries where surface quality is more critical than deposition speed, such as in advanced semiconductor devices.
-
Advancements in Magnetron Sputtering:
- Magnetron sputtering, a specialized form of the process, offers even higher deposition rates and greater control. It is particularly effective for depositing dielectric and nitride films, which are essential in microelectronics. Ongoing research continues to improve its efficiency and expand its applications.
In summary, the sputtering process stands out for its ability to produce high-quality, uniform films with precise control over thickness and morphology. Its versatility, efficiency, and ability to operate at lower temperatures make it a preferred choice for a wide range of industrial applications.
Summary Table:
Advantage | Description |
---|---|
Better Film Densification | Produces dense, high-quality films with minimal voids or defects. |
Reduced Residual Stresses | Operates at low/medium temperatures, minimizing thermal stress on substrates. |
High Deposition Rates | Enables efficient production of thick films without quality compromise. |
In-Situ Substrate Cleaning | Cleans substrates in vacuum chambers, ensuring better adhesion. |
Precise Control Over Films | Adjusts power, pressure, and time for exact thickness and uniformity. |
Versatility in Materials | Deposits metals, alloys, dielectrics, and nitrides for diverse applications. |
Enhanced Morphological Quality | Controls surface roughness, grain size, and stoichiometry for superior quality. |
Magnetron Sputtering Advancements | Offers higher deposition rates and greater control for microelectronics. |
Unlock the full potential of sputtering for your applications—contact our experts today!