The fluidization process, particularly in fluidized bed reactors (FBRs), offers significant advantages in various industrial applications, including chemical, petroleum, and biomass processing. Key benefits include uniform particle mixing, consistent temperature gradients, and the ability to operate continuously. These features enhance reaction efficiency, prevent hot or cold spots, and eliminate the need for batch processing, making FBRs highly effective for exothermic reactions and particulate substrates like woody biomass. Additionally, FBRs improve yield for byproducts such as bio-oils and gases, making them a versatile and efficient choice for industrial processes.
Key Points Explained:
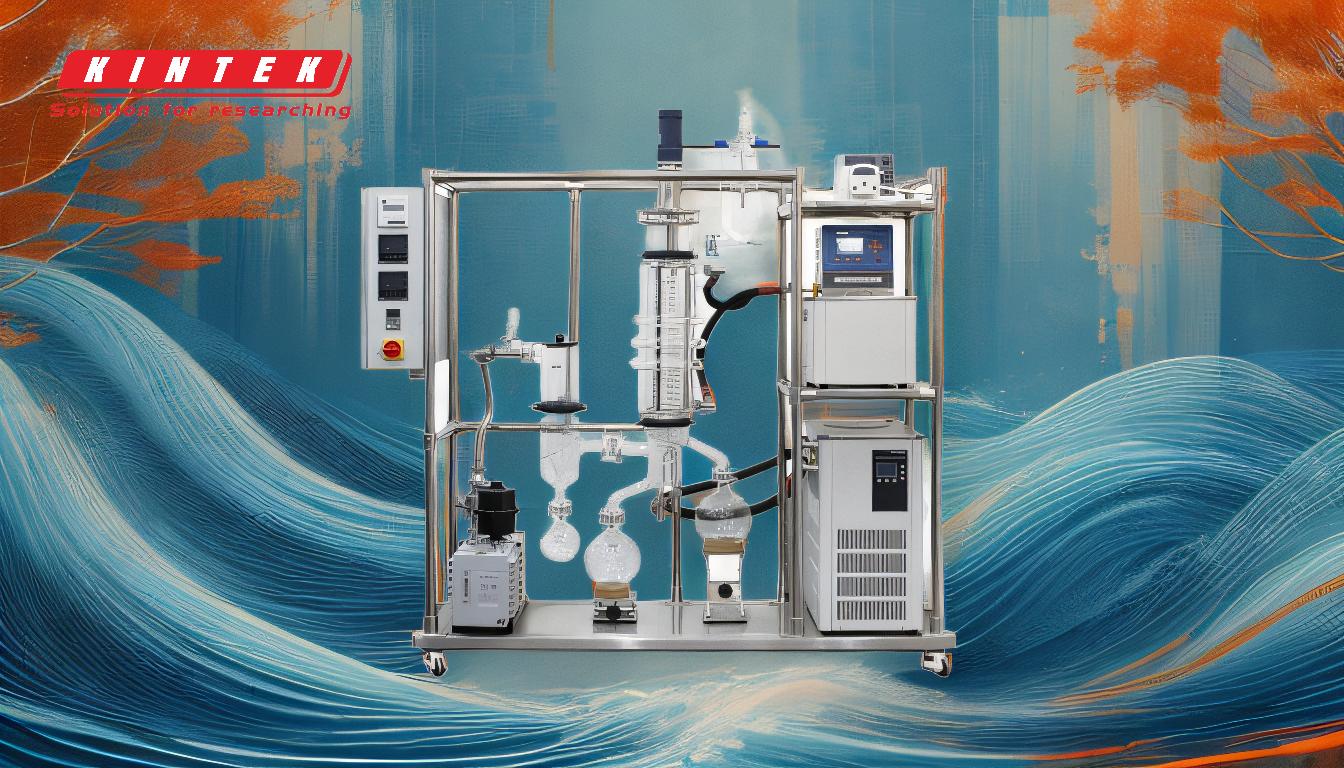
-
Uniform Particle Mixing
- Fluidized bed reactors ensure complete mixing of solid particles due to their fluid-like behavior.
- This eliminates radial and axial concentration gradients, leading to improved reaction efficiency.
- Uniform mixing is particularly beneficial for particulate substrates like woody biomass, ensuring consistent contact between reactants and catalysts.
-
Uniform Temperature Gradients
- FBRs maintain consistent temperature gradients throughout the reactor, preventing the formation of hot or cold spots.
- This uniformity is critical for exothermic reactions, where localized temperature spikes can lead to inefficiencies or safety hazards.
- The controlled temperature environment enhances the stability and predictability of the process.
-
Continuous Operation
- Unlike batch processes, FBRs can operate continuously, eliminating the need for frequent startups and shutdowns.
- Continuous operation improves production efficiency and reduces downtime, making FBRs ideal for large-scale industrial applications.
- This feature is particularly advantageous in industries like petroleum refining and chemical manufacturing, where high throughput is essential.
-
Enhanced Yield of Byproducts
- FBRs are highly effective in maximizing the yield of valuable byproducts such as bio-oils and gases.
- The fluidization process ensures optimal contact between reactants and catalysts, leading to more complete and efficient reactions.
- This makes FBRs a preferred choice for biomass processing and other applications where byproduct recovery is economically important.
-
Versatility Across Industries
- FBRs are widely used in diverse industries, including petroleum, chemical, and biomass processing.
- Their ability to handle particulate substrates and exothermic reactions makes them adaptable to a range of processes.
- This versatility, combined with their efficiency and continuous operation, positions FBRs as a cornerstone technology in modern industrial operations.
-
Improved Reaction Efficiency
- The fluid-like behavior of solid materials in FBRs ensures thorough mixing and optimal reaction conditions.
- This leads to faster reaction rates and higher conversion efficiencies compared to traditional reactors.
- The elimination of concentration gradients further enhances the overall performance of the reactor.
-
Scalability and Cost-Effectiveness
- FBRs are scalable, making them suitable for both small-scale and large-scale industrial applications.
- Their continuous operation reduces operational costs by minimizing energy consumption and downtime.
- The ability to handle a wide range of materials and reactions further contributes to their cost-effectiveness.
-
Environmental Benefits
- The efficient use of reactants and catalysts in FBRs reduces waste generation and improves resource utilization.
- The controlled temperature environment minimizes the risk of harmful emissions or byproducts.
- These environmental benefits align with sustainability goals and regulatory requirements in various industries.
By leveraging these advantages, fluidized bed reactors provide a robust and efficient solution for a wide range of industrial processes, making them a preferred choice for applications requiring high efficiency, scalability, and continuous operation.
Summary Table:
Advantage | Key Benefit |
---|---|
Uniform Particle Mixing | Ensures complete mixing, eliminating concentration gradients for better efficiency. |
Uniform Temperature Gradients | Prevents hot or cold spots, ideal for exothermic reactions. |
Continuous Operation | Eliminates batch processing, reducing downtime and improving throughput. |
Enhanced Byproduct Yield | Maximizes bio-oils and gases, optimizing resource utilization. |
Versatility Across Industries | Adaptable to petroleum, chemical, and biomass processing. |
Improved Reaction Efficiency | Faster reaction rates and higher conversion efficiencies. |
Scalability and Cost-Effectiveness | Suitable for small- and large-scale applications, reducing operational costs. |
Environmental Benefits | Reduces waste and harmful emissions, aligning with sustainability goals. |
Ready to enhance your industrial processes with fluidized bed reactors? Contact our experts today to learn more!