Sputtering is a widely used physical vapor deposition (PVD) technique for thin-film deposition. However, there are several alternatives to sputtering that can be employed depending on the specific requirements of the application, such as film quality, thickness, substrate material, and cost. These alternatives can be broadly categorized into physical and chemical deposition methods. Physical methods include thermal evaporation, electron beam evaporation, pulsed laser deposition (PLD), and molecular beam epitaxy (MBE). Chemical methods include chemical vapor deposition (CVD), plasma-enhanced CVD (PECVD), atomic layer deposition (ALD), electroplating, sol-gel, dip coating, and spin coating. Each method has its unique advantages and limitations, making it suitable for specific applications.
Key Points Explained:
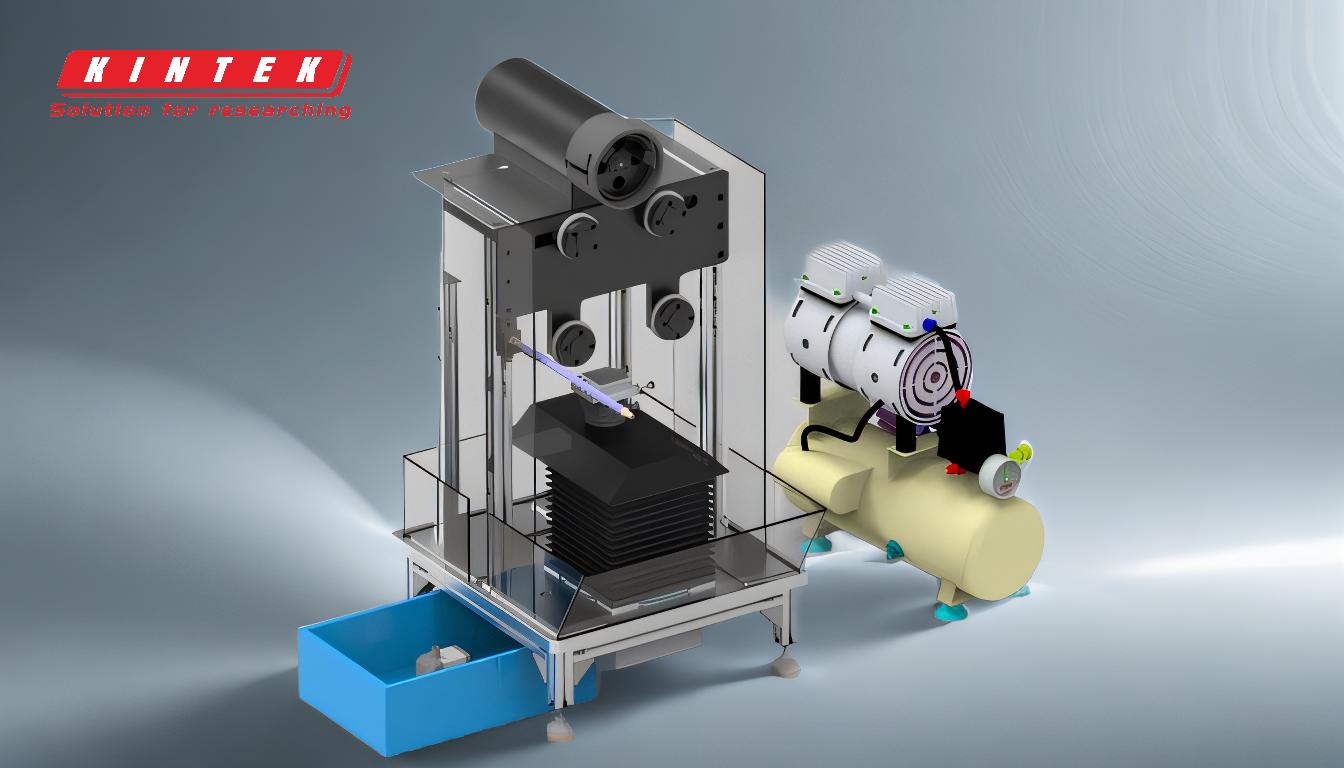
-
Thermal Evaporation:
- Process: Involves heating a material in a vacuum until it vaporizes, then condensing it onto a substrate to form a thin film.
- Advantages: Simple and cost-effective; suitable for depositing metals and simple compounds.
- Limitations: Limited to materials with low melting points; poor step coverage and adhesion on complex geometries.
-
Electron Beam Evaporation:
- Process: Uses a focused electron beam to heat and vaporize the target material in a vacuum.
- Advantages: Can deposit high-melting-point materials; provides high-purity films.
- Limitations: Expensive equipment; requires precise control of electron beam parameters.
-
Pulsed Laser Deposition (PLD):
- Process: A high-power laser pulse ablates the target material, creating a plasma plume that deposits onto the substrate.
- Advantages: Excellent for complex oxides and multi-component materials; high deposition rates.
- Limitations: Limited to small-area deposition; can cause particulate contamination.
-
Molecular Beam Epitaxy (MBE):
- Process: A highly controlled process where atomic or molecular beams are directed onto a substrate under ultra-high vacuum.
- Advantages: Produces extremely high-quality, epitaxial films with precise control over thickness and composition.
- Limitations: Extremely slow and expensive; limited to small substrates.
-
Chemical Vapor Deposition (CVD):
- Process: Involves chemical reactions of gaseous precursors to form a solid film on the substrate.
- Advantages: Excellent step coverage; can deposit a wide range of materials, including complex compounds.
- Limitations: Requires high temperatures; precursor gases can be hazardous.
-
Plasma-Enhanced CVD (PECVD):
- Process: Similar to CVD but uses plasma to enhance chemical reactions, allowing deposition at lower temperatures.
- Advantages: Lower deposition temperatures; good for temperature-sensitive substrates.
- Limitations: More complex equipment; limited to certain materials.
-
Atomic Layer Deposition (ALD):
- Process: A sequential, self-limiting process where alternating precursor gases react with the substrate to deposit one atomic layer at a time.
- Advantages: Exceptional control over film thickness and uniformity; excellent for conformal coatings.
- Limitations: Very slow deposition rates; limited material selection.
-
Electroplating:
- Process: Uses an electric current to reduce metal ions in a solution, depositing them onto a conductive substrate.
- Advantages: Cost-effective for large-area deposition; can produce thick films.
- Limitations: Limited to conductive substrates; requires post-processing for some applications.
-
Sol-Gel:
- Process: Involves the transition of a solution (sol) into a gel, which is then dried and sintered to form a thin film.
- Advantages: Can produce complex oxides and ceramics; low-temperature processing.
- Limitations: Limited to certain materials; can produce porous films.
-
Dip Coating and Spin Coating:
- Process: Dip coating involves immersing the substrate in a solution, while spin coating involves spinning the substrate to spread the solution evenly.
- Advantages: Simple and cost-effective; suitable for large-area deposition.
- Limitations: Limited to certain materials; film thickness control can be challenging.
Conclusion:
The choice of an alternative to sputtering depends on the specific requirements of the application, such as the type of material to be deposited, the desired film quality, and the substrate characteristics. Each method has its own set of advantages and limitations, making it crucial to carefully evaluate the options to achieve the best results for a given application.
Summary Table:
Method | Category | Advantages | Limitations |
---|---|---|---|
Thermal Evaporation | Physical | Simple, cost-effective, suitable for metals and simple compounds | Limited to low-melting-point materials; poor step coverage |
Electron Beam Evaporation | Physical | Deposits high-melting-point materials; high-purity films | Expensive; requires precise control of electron beam |
Pulsed Laser Deposition | Physical | Excellent for complex oxides; high deposition rates | Limited to small areas; particulate contamination |
Molecular Beam Epitaxy | Physical | High-quality epitaxial films; precise thickness and composition control | Slow, expensive; limited to small substrates |
Chemical Vapor Deposition | Chemical | Excellent step coverage; wide material range | High temperatures; hazardous precursor gases |
Plasma-Enhanced CVD | Chemical | Lower deposition temperatures; good for sensitive substrates | Complex equipment; limited material selection |
Atomic Layer Deposition | Chemical | Exceptional thickness control; excellent for conformal coatings | Slow deposition rates; limited material selection |
Electroplating | Chemical | Cost-effective for large areas; thick films | Limited to conductive substrates; requires post-processing |
Sol-Gel | Chemical | Produces complex oxides; low-temperature processing | Limited materials; porous films |
Dip/Spin Coating | Chemical | Simple, cost-effective; suitable for large areas | Limited materials; challenging thickness control |
Need help choosing the right thin-film deposition method? Contact our experts today for personalized guidance!