Physical vapor deposition (PVD) is a versatile and widely used technique in various industries due to its ability to produce high-quality, durable, and functional coatings. Unlike chemical vapor deposition (CVD), which relies on chemical reactions in the vapor phase, PVD involves the physical transfer of material from a source to a substrate in a vacuum environment. This process is used to create thin films with specific properties, such as improved wear resistance, corrosion resistance, and aesthetic appeal. PVD is applied in industries ranging from electronics and optics to automotive and decorative finishes, making it a critical technology in modern manufacturing and material science.
Key Points Explained:
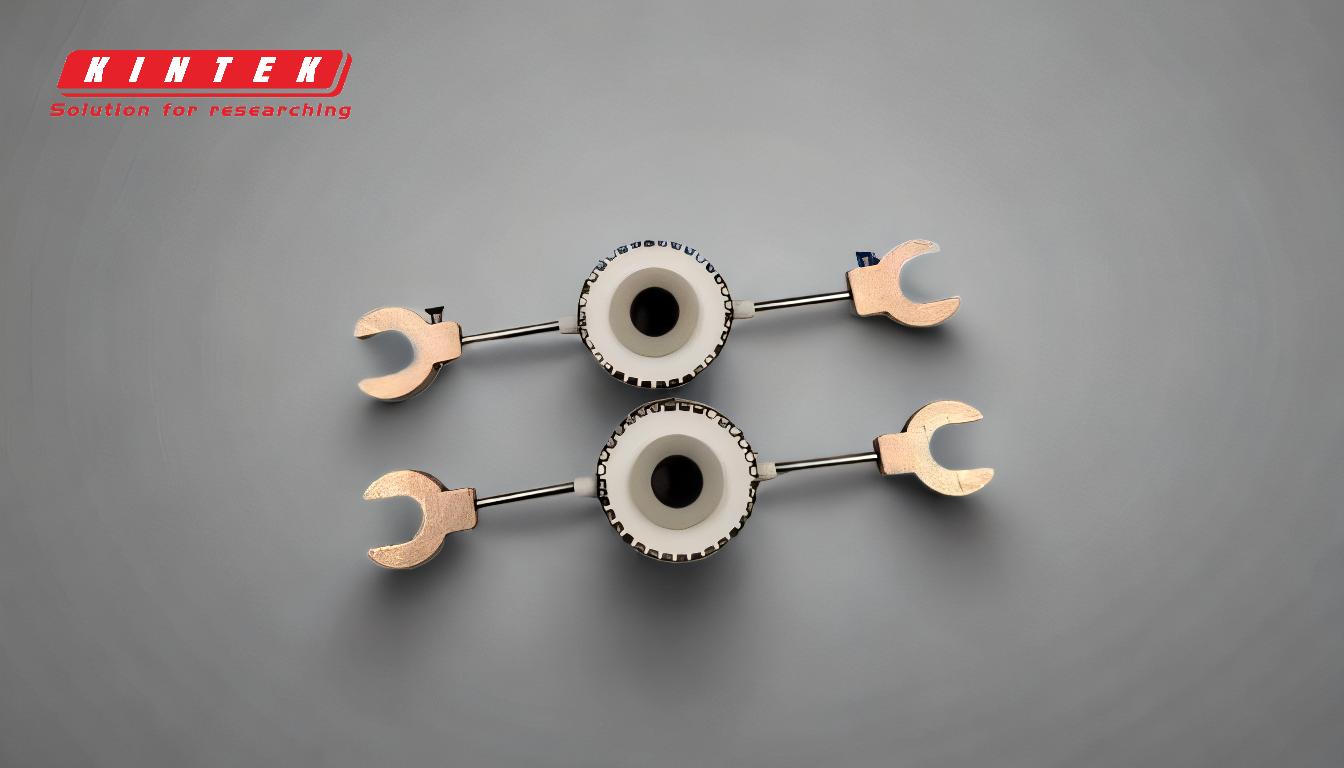
-
Electronics and Semiconductor Industry
- PVD is extensively used in the electronics and semiconductor industries to deposit thin films of metals, alloys, and compounds. These films are essential for creating conductive layers, interconnects, and barrier layers in integrated circuits and microelectronic devices.
- For example, PVD is used to deposit aluminum, copper, and titanium nitride (TiN) layers, which are critical for the performance and reliability of semiconductor devices.
- The ability to produce uniform and high-purity coatings makes PVD indispensable in the fabrication of advanced electronic components.
-
Optoelectronics and Optics
- PVD is employed in the production of optical coatings, such as anti-reflective coatings, mirrors, and filters. These coatings enhance the performance of optical devices by controlling light transmission, reflection, and absorption.
- In the optoelectronics industry, PVD is used to deposit thin films for light-emitting diodes (LEDs), solar cells, and displays. The precise control over film thickness and composition ensures optimal performance of these devices.
- For instance, PVD is used to deposit indium tin oxide (ITO) coatings, which are transparent and conductive, making them ideal for touchscreens and photovoltaic applications.
-
Automotive Industry
- PVD coatings are widely used in the automotive industry to improve the durability and aesthetics of components. Coatings such as chromium nitride (CrN) and titanium aluminum nitride (TiAlN) provide enhanced wear and corrosion resistance for engine parts, cutting tools, and decorative trim.
- The vibrant colors and finishes achieved through PVD, such as gold, black, and bronze, are used for decorative applications, including interior and exterior automotive components.
- PVD coatings also contribute to reducing friction and improving fuel efficiency in automotive systems.
-
Decorative and Architectural Applications
- PVD is used to create decorative coatings on consumer products, such as watches, jewelry, and smartphones. These coatings provide a durable and scratch-resistant finish with a wide range of colors and textures.
- In architecture, PVD coatings are applied to building materials, such as glass and metal, to enhance their appearance and durability. For example, PVD-coated stainless steel is used for façades, elevators, and interior design elements.
- The environmental benefits of PVD, such as the absence of harmful chemicals and reduced waste, make it a sustainable choice for decorative applications.
-
Tool and Die Industry
- PVD coatings are used to extend the lifespan and performance of cutting tools, molds, and dies. Coatings such as titanium nitride (TiN), titanium carbonitride (TiCN), and diamond-like carbon (DLC) provide superior hardness, wear resistance, and thermal stability.
- These coatings enable tools to operate at higher speeds and temperatures, improving productivity and reducing downtime in manufacturing processes.
- PVD-coated tools are widely used in industries such as aerospace, automotive, and metalworking.
-
Medical and Biomedical Applications
- PVD is used to deposit biocompatible coatings on medical implants and devices, such as orthopedic implants, dental instruments, and surgical tools. These coatings improve the wear resistance, corrosion resistance, and biocompatibility of medical devices.
- For example, PVD is used to deposit titanium and hydroxyapatite coatings on implants to promote osseointegration and reduce the risk of rejection.
- The ability to produce thin, uniform, and high-purity coatings makes PVD a valuable technology in the medical field.
-
Aerospace and Defense
- PVD coatings are used in the aerospace and defense industries to enhance the performance and durability of components exposed to extreme conditions. Coatings such as chromium nitride (CrN) and titanium aluminum nitride (TiAlN) provide protection against wear, corrosion, and high temperatures.
- PVD is used to coat turbine blades, engine components, and cutting tools, ensuring their reliability and longevity in demanding environments.
- The precision and consistency of PVD coatings make them ideal for critical applications in aerospace and defense.
In summary, physical vapor deposition (PVD) is a versatile and essential technology with applications across a wide range of industries. Its ability to produce high-quality, durable, and functional coatings makes it indispensable in electronics, optics, automotive, decorative, tooling, medical, and aerospace applications. The precise control over film properties and the environmental benefits of PVD further enhance its value in modern manufacturing and material science.
Summary Table:
Industry | Applications |
---|---|
Electronics & Semiconductor | Conductive layers, interconnects, barrier layers in microelectronic devices |
Optoelectronics & Optics | Anti-reflective coatings, mirrors, LEDs, solar cells, displays |
Automotive | Wear-resistant coatings, decorative finishes, fuel efficiency improvements |
Decorative & Architectural | Scratch-resistant coatings for watches, jewelry, smartphones, and building materials |
Tool & Die | Extended tool lifespan, improved hardness, wear resistance |
Medical & Biomedical | Biocompatible coatings for implants, dental instruments, surgical tools |
Aerospace & Defense | High-performance coatings for turbine blades, engine components, cutting tools |
Learn how PVD can revolutionize your industry—contact us today for expert advice!