A rotary kiln is a thermal processing device used to heat materials to high temperatures for various industrial applications. It consists of a rotating cylindrical drum, slightly inclined from the horizontal, which allows materials to move through it by gravity. The kiln can be heated directly or indirectly, depending on the application, and is designed to achieve specific chemical reactions or physical changes in the materials. The temperature, retention time, and movement of materials are carefully controlled to ensure efficient processing. Rotary kilns are widely used in industries such as cement production, metallurgy, and chemical processing due to their ability to handle continuous, high-temperature operations.
Key Points Explained:
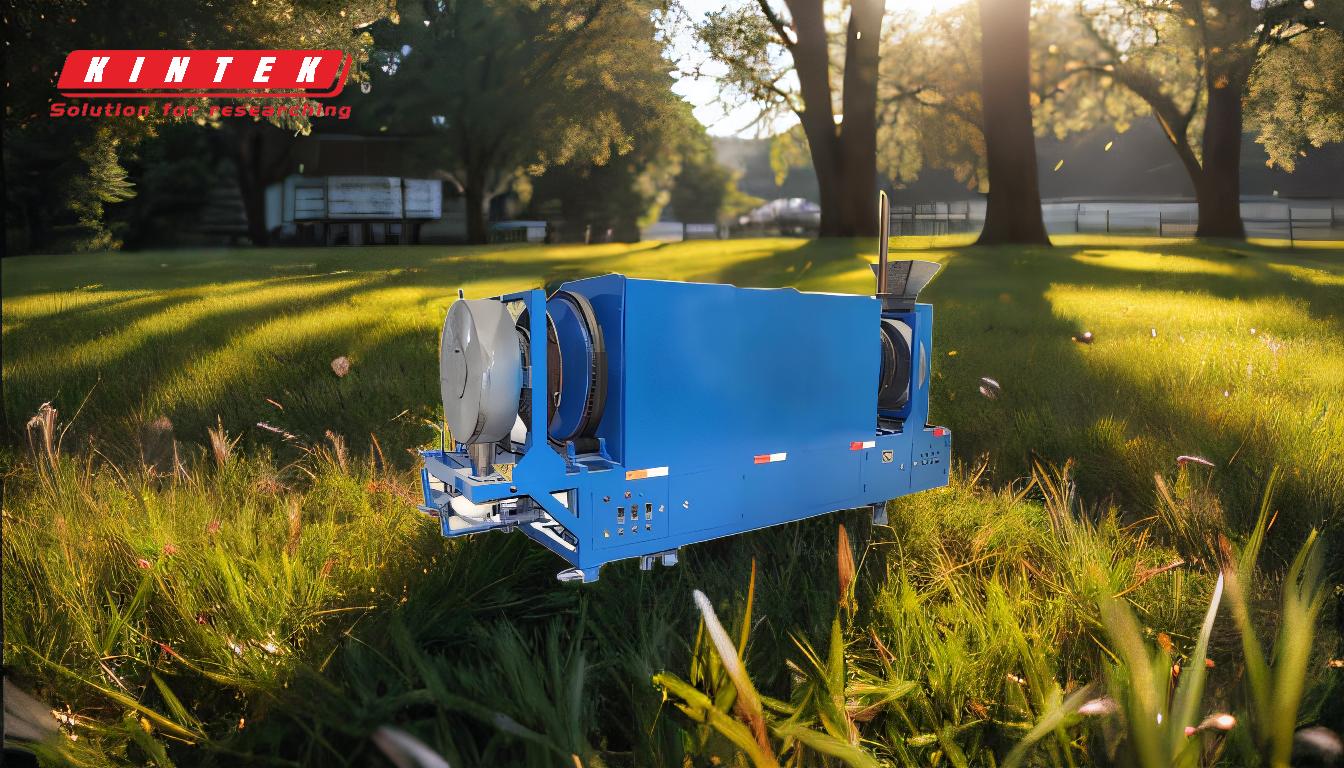
-
Basic Structure of a Rotary Kiln:
- A rotary kiln is a long, cylindrical vessel that is slightly inclined from the horizontal plane.
- The kiln rotates slowly about its longitudinal axis, allowing materials to move through it by gravity.
- The drum is typically lined with refractory materials to withstand high temperatures and protect the outer shell from heat damage.
- The kiln is equipped with rollers to support its rotation and a burner or external heating source to provide the necessary heat.
-
Heating Mechanism:
- Rotary kilns can be heated either directly or indirectly.
- Direct Heating: The heat source (e.g., a flame or hot gases) is in direct contact with the material inside the kiln. This method is commonly used in cement kilns.
- Indirect Heating: The heat source is external, and the heat is transferred to the material through the walls of the kiln. This method is often used in electric rotary kilns.
- The heating mechanism is designed to achieve the required temperature for the specific process, such as calcination, reduction, or sintering.
- Rotary kilns can be heated either directly or indirectly.
-
Material Movement and Retention Time:
- The inclination and rotation of the kiln cause the material to move from the upper (feed) end to the lower (discharge) end.
- The retention time (the time the material spends in the kiln) is controlled by adjusting the rotation speed and the angle of inclination.
- The movement of the material ensures uniform heating and mixing, which is crucial for achieving the desired chemical or physical changes.
-
Temperature Control:
- The temperature inside the kiln is carefully controlled based on the specific requirements of the process.
- Temperature profiles are determined through chemical and thermal analyses to ensure that the material reaches the necessary temperature for the reaction or change to occur.
- The kiln is equipped with sensors and control systems to monitor and adjust the temperature as needed.
-
Applications of Rotary Kilns:
- Cement Production: Rotary kilns are widely used in the production of cement clinker, where limestone and other raw materials are heated to high temperatures to form clinker.
- Metallurgy: Rotary kilns are used in the reduction of metal ores, such as iron ore, to produce metals or metal oxides.
- Chemical Processing: Rotary kilns are used in various chemical processes, including the production of lime, alumina, and other industrial chemicals.
- Waste Treatment: Rotary kilns are used in the incineration of hazardous waste and the calcination of waste materials to recover valuable components.
-
Advantages of Rotary Kilns:
- Continuous Operation: Rotary kilns allow for continuous processing of materials, making them highly efficient for large-scale industrial applications.
- Uniform Heating: The rotation of the kiln ensures that materials are heated uniformly, reducing the risk of hot spots or uneven processing.
- Versatility: Rotary kilns can be used for a wide range of materials and processes, making them a versatile tool in many industries.
- Controlled Atmosphere: The kiln can be sealed to control the atmosphere inside, allowing for processes that require specific gas compositions or pressure conditions.
-
Challenges and Considerations:
- Energy Consumption: Rotary kilns can be energy-intensive, especially in high-temperature applications. Energy efficiency is a key consideration in their design and operation.
- Maintenance: The high temperatures and mechanical stresses involved in rotary kiln operation require regular maintenance to prevent wear and tear on the refractory lining and other components.
- Material Handling: The movement of materials through the kiln must be carefully controlled to prevent blockages or uneven processing.
-
Future Trends:
- Energy Efficiency: There is a growing focus on improving the energy efficiency of rotary kilns, including the use of alternative fuels and heat recovery systems.
- Automation and Control: Advances in automation and control systems are making it easier to monitor and optimize the operation of rotary kilns, leading to better process control and reduced operational costs.
- Environmental Impact: There is increasing pressure to reduce the environmental impact of rotary kilns, particularly in terms of emissions and waste management. This is driving the development of cleaner and more sustainable kiln technologies.
In summary, rotary kilns are essential tools in many industrial processes, offering a reliable and efficient means of heating materials to high temperatures. Their design, operation, and applications are complex, but they provide significant advantages in terms of continuous processing, uniform heating, and versatility. As industries continue to evolve, rotary kilns are likely to see further advancements in energy efficiency, automation, and environmental performance.
Summary Table:
Aspect | Details |
---|---|
Structure | Cylindrical, inclined drum lined with refractory materials. |
Heating Mechanism | Direct (flame/hot gases) or indirect (external heat transfer). |
Material Movement | Controlled by rotation speed and inclination angle for uniform heating. |
Temperature Control | Sensors and control systems ensure precise temperature profiles. |
Applications | Cement production, metallurgy, chemical processing, waste treatment. |
Advantages | Continuous operation, uniform heating, versatility, controlled atmosphere. |
Challenges | High energy consumption, maintenance needs, material handling. |
Future Trends | Improved energy efficiency, automation, and reduced environmental impact. |
Interested in optimizing your industrial processes with rotary kilns? Contact our experts today for tailored solutions!