Plasma-Enhanced Chemical Vapor Deposition (PECVD) is a versatile thin-film deposition technique that offers numerous benefits, particularly in applications requiring low-temperature processing and precise control over film properties. By utilizing plasma to enhance chemical reactions, PECVD enables the deposition of high-quality films at lower temperatures, making it suitable for temperature-sensitive substrates. This method also allows for tunable control over film composition, thickness, and conformality, making it ideal for applications in microelectronics, optics, and biomedical fields. Additionally, PECVD's ability to deposit films on irregular surfaces and its compatibility with mass production further enhance its industrial relevance.
Key Points Explained:
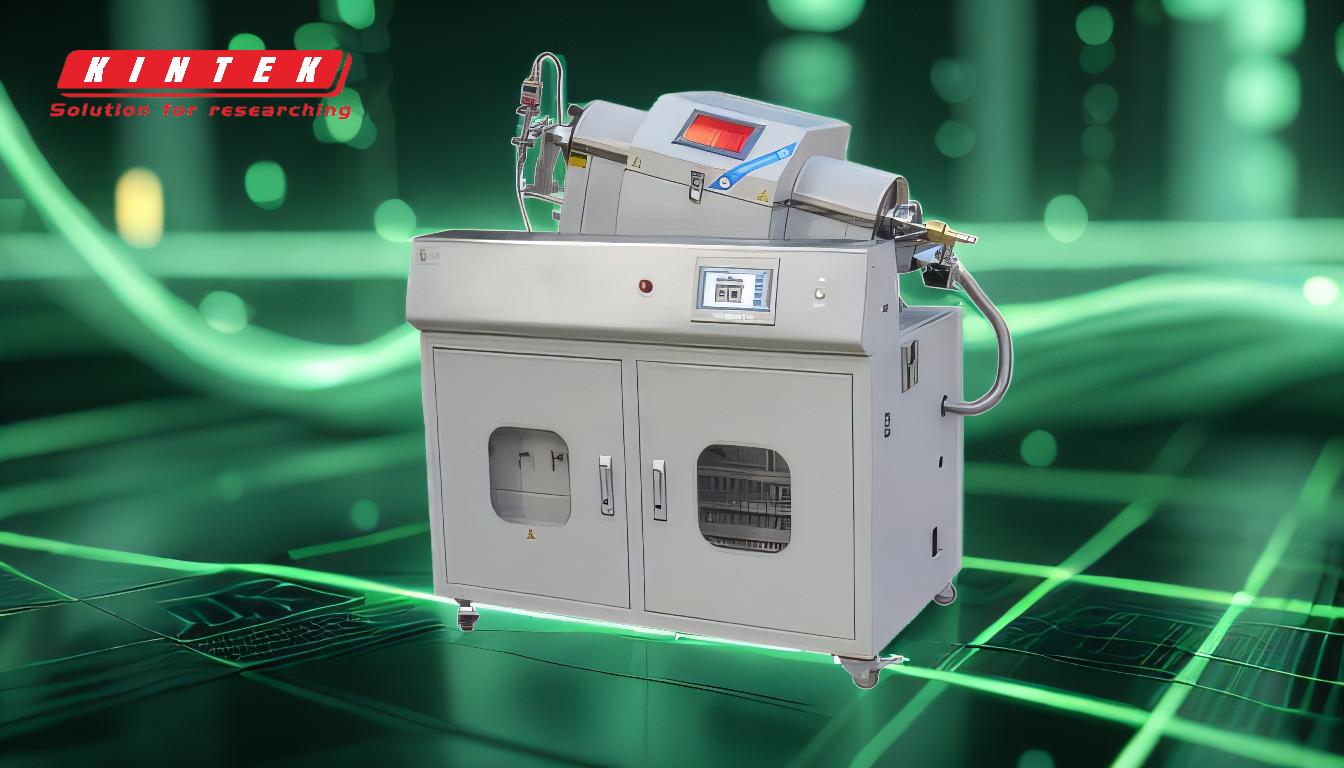
-
Lower Processing Temperatures:
- PECVD significantly reduces the processing temperature compared to traditional methods like Low-Pressure Chemical Vapor Deposition (LPCVD). While LPCVD typically operates between 425-900°C, PECVD operates at much lower temperatures, typically between 200-400°C. This is particularly beneficial for temperature-sensitive substrates, such as polymers or certain semiconductors, where high temperatures could degrade material properties or cause thermal stress.
-
Enhanced Deposition Rates:
- PECVD allows for faster deposition rates while maintaining or even improving film quality. The use of plasma excites the reacting gases, increasing their chemical activity and enabling quicker film formation. This is especially advantageous in industrial settings where high throughput and efficiency are critical.
-
Tunable Film Properties:
- One of the standout features of PECVD is its ability to precisely control the chemical composition and physical properties of the deposited films. This includes tailoring properties such as hardness, conductivity, optical transparency, and color. Such control is essential for applications in microelectronics, where specific electrical or optical characteristics are required, and in biomedical applications, where surface properties can influence biocompatibility.
-
Conformal Coating on Irregular Surfaces:
- PECVD excels at depositing uniform and conformal films on substrates with complex geometries or irregular surfaces. This is due to the plasma's ability to evenly distribute reactive species across the substrate, ensuring consistent film growth even in challenging topographies. This capability is crucial for applications like MEMS (Micro-Electro-Mechanical Systems) and advanced optical coatings.
-
Ionic Release and Chemical Instability for Biomedical Applications:
- The energetic conditions in PECVD reactors create high-energy bonding states that are relatively unstable. While this instability can be a drawback in some microelectronic applications, it is beneficial in biomedical contexts. For example, the controlled release of ions from PECVD-deposited films can enhance biocompatibility or enable therapeutic effects, such as antimicrobial activity.
-
Compatibility with Mass Production:
- PECVD is well-suited for large-scale manufacturing due to its fast deposition rates, stable film quality, and ability to handle multiple substrates simultaneously. This makes it a cost-effective solution for industries requiring high-volume production of thin films, such as solar panels, flat-panel displays, and semiconductor devices.
-
Energy Efficiency:
- By using plasma to provide the energy needed for chemical reactions, PECVD reduces the overall energy consumption compared to purely thermal CVD processes. This not only lowers operational costs but also aligns with sustainability goals by minimizing the environmental impact of thin-film manufacturing.
-
Versatility in Material Deposition:
- PECVD can deposit a wide range of materials, including silicon-based films (e.g., silicon nitride, silicon dioxide), carbon-based films (e.g., diamond-like carbon), and various metal oxides. This versatility makes it a valuable tool for diverse applications, from creating insulating layers in microelectronics to producing hard coatings for wear resistance.
In summary, PECVD offers a unique combination of low-temperature processing, high deposition rates, precise control over film properties, and versatility in material deposition. These benefits make it a preferred choice for industries requiring advanced thin-film technologies, particularly in microelectronics, optics, and biomedical fields. Its ability to deposit conformal coatings on complex geometries and its compatibility with mass production further enhance its industrial relevance, making it a cornerstone of modern thin-film manufacturing.
Summary Table:
Benefit | Description |
---|---|
Lower Processing Temperatures | Operates at 200-400°C, ideal for temperature-sensitive substrates. |
Enhanced Deposition Rates | Faster deposition with high-quality film formation. |
Tunable Film Properties | Precise control over hardness, conductivity, and optical properties. |
Conformal Coating | Uniform film deposition on complex or irregular surfaces. |
Biomedical Applications | Enables biocompatibility and therapeutic effects like antimicrobial activity. |
Mass Production Compatibility | High-throughput, cost-effective for industries like solar panels and displays. |
Energy Efficiency | Reduces energy consumption, aligning with sustainability goals. |
Versatility in Materials | Deposits silicon-based, carbon-based, and metal oxide films for diverse uses. |
Ready to leverage PECVD for your thin-film needs? Contact us today to learn more!